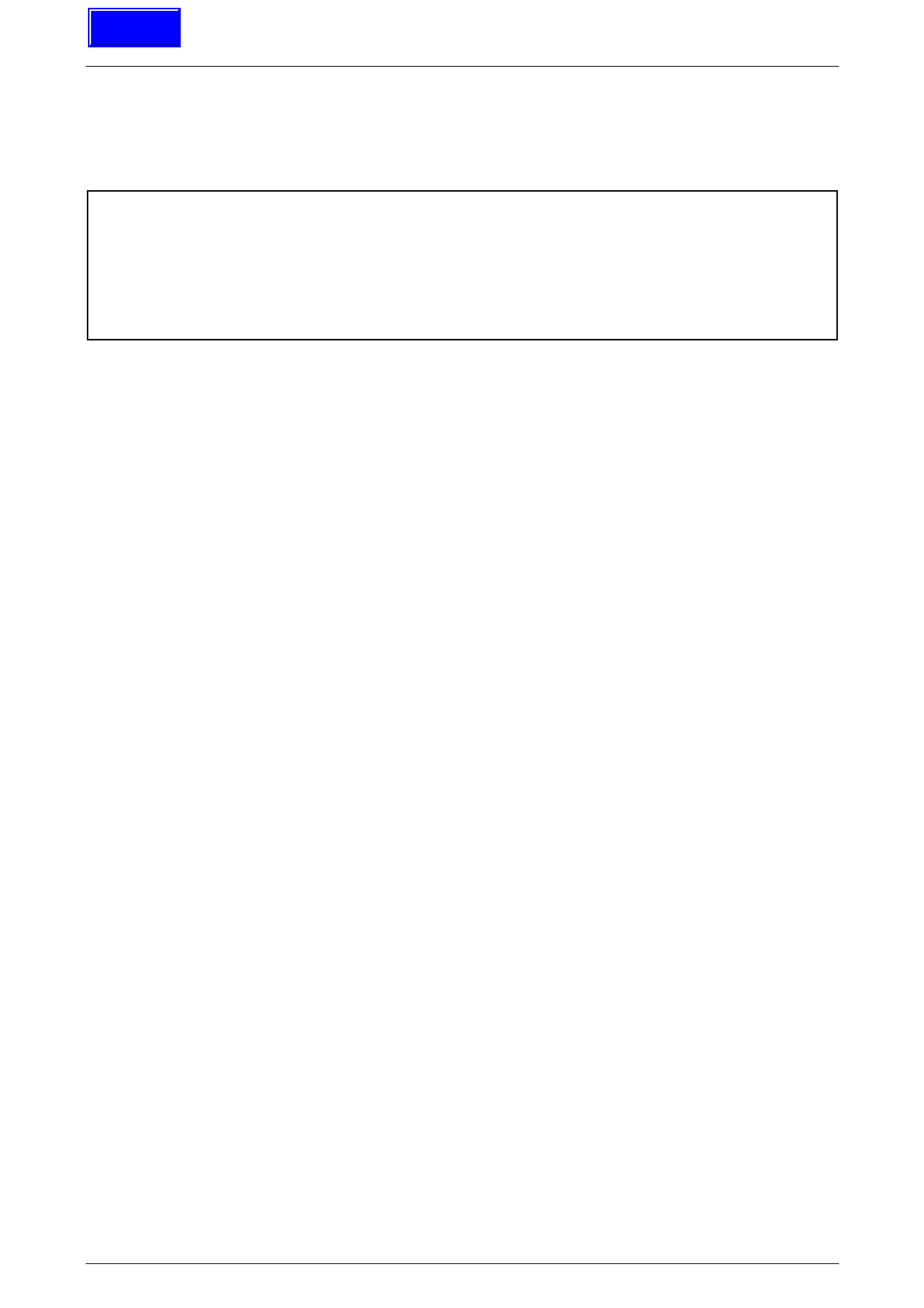
Transmissions, Final Drive And Propeller Shaft Page F-1
Page F-1
Section F
Transmissions, Final Drive And Propeller Shaft
ATTENTION
HSV vehicles are equipped with a Supplemental Restraint System (SRS). An SRS consists of seat belt pre-
tensioners (fitted to all front seats), a driver’s-side air bag , a passenger’s-side air bag and left and right hand
side air bags. Refer to CAUTIONS, Section 12M Occupant Protection System in the MY 2005 VZ Coupe Series
Service Information before performing any service operation on or around SRS components, the steering
mechanism or wiring. Failure to follow the CAUTIONS could result in personal injury or unnecessary SRS
system repairs.
1 Purpose...................................................................................................................................................2
2 Transmissions........................................................................................................................................3
2.1 Automatic Transmission....................................................................................................................................... 3
Electrical Diagnosis............................................................................................................................................... 3
Hydraulic/Mechanical Diagnosis.......................................................................................................................... 3
On-vehicle Servicing.............................................................................................................................................. 3
Unit Repair.............................................................................................................................................................. 3
2.2 Manual Transmission ............................................................................................................................................ 4
Service Operations ................................................................................................................................................ 4
Clutch...................................................................................................................................................................... 4
3 Final Drive & Drive Shafts .....................................................................................................................5
3.1 General Information............................................................................................................................................... 5
3.2 Final Drive Assembly Identification...................................................................................................................... 6
3.3 Service Operations ................................................................................................................................................ 7
3.4 Diagnosis................................................................................................................................................................ 8
3.5 Specifications......................................................................................................................................................... 9
4 Propeller Shafts & Universal Joints ...................................................................................................10
4.1 General Information............................................................................................................................................. 10
4.2 Service Operations .............................................................................................................................................. 11
4.3 Diagnosis.............................................................................................................................................................. 12
4.4 Specifications....................................................................................................................................................... 13
5 Rear Final Drive and Drive Shafts ......................................................................................................14
5.1 General Information............................................................................................................................................. 14
5.2 Major Service Operations.................................................................................................................................... 15
Final Drive Assembly Unit Repair....................................................................................................................... 15
Reassemble ..................................................................................................................................................... 15
5.3 Pinion Flange ....................................................................................................................................................... 22
Replace (Vehicles With a Rear Rubber Coupling)............................................................................................. 22
Using Old Oil Seal............................................................................................................................................ 22
6 Special Tools ........................................................................................................................................25