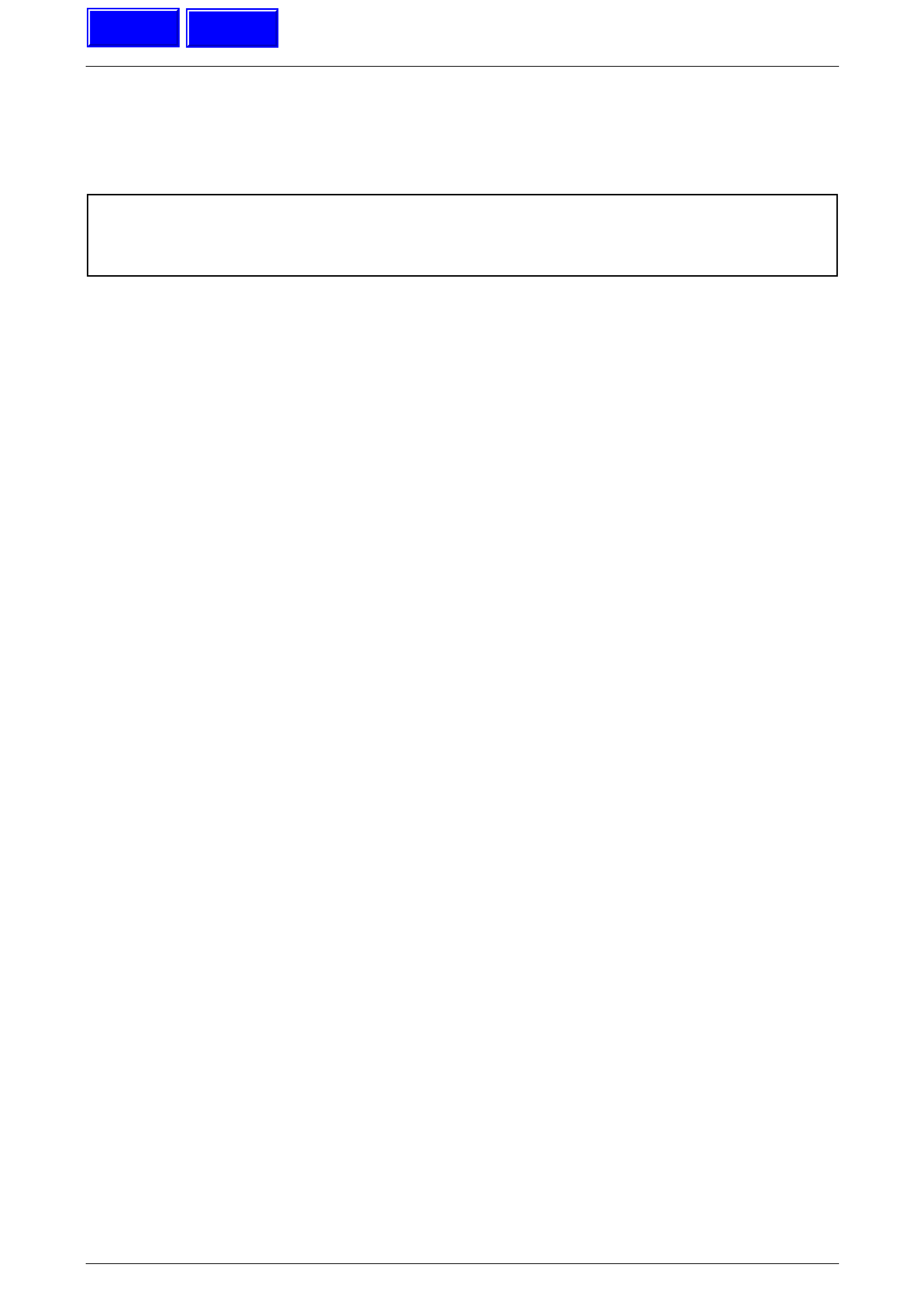
Front Final Drive, Bearing Housing & Driveshafts Page 4B3–1
Page 4B3-1
Section 4B3
Front Final Drive, Bearing Housing & Driveshafts
ATTENTION
Before performing any Service Operation or other procedure described in this Section, refer to Section 00
Warnings, Cautions and Notes for correct workshop practices with regard to safety and/or property damage.
1 General Description ...............................................................................................................................3
1.1 Final Drive Assembly Identification ..................................................................................................................... 4
1.2 Final Drive Maintenance........................................................................................................................................ 5
Maintenance........................................................................................................................................................... 5
Driveshaft Bearings and Constant Velocity Joints.............................................................................................. 5
Differential Carrier Assembly.............................................................................................................................. 5
Final Drive Assembly Breather........................................................................................................................... 5
Lubrication ............................................................................................................................................................. 6
2 Minor Service Operations......................................................................................................................7
2.1 Checking Final Drive Lubricant Level.................................................................................................................. 7
2.2 Changing/Flushing Final Drive Lubricant............................................................................................................ 8
2.3 Pinion Oil Seal........................................................................................................................................................ 9
Replace................................................................................................................................................................... 9
2.4 Driveshaft Assembly ........................................................................................................................................... 10
Remove................................................................................................................................................................. 10
Reinstall................................................................................................................................................................ 12
2.5 Driveshaft Outer Constant Velocity Joint.......................................................................................................... 15
Remove................................................................................................................................................................. 15
Reinstall................................................................................................................................................................ 17
2.6 Driveshaft Inner Tripot Joint............................................................................................................................... 18
Disassemble......................................................................................................................................................... 18
Inspect .................................................................................................................................................................. 20
Reassemble.......................................................................................................................................................... 20
2.7 Bearing Housing/Final Drive Carrier Outer Oil Seal.......................................................................................... 22
Replace................................................................................................................................................................. 22
2.8 Pinion Oil Seal...................................................................................................................................................... 24
Replace................................................................................................................................................................. 24
2.9 Pinion Flange ....................................................................................................................................................... 25
Replace................................................................................................................................................................. 25
3 Major Service Operations....................................................................................................................26
3.1 Bearing Housing Assembly ................................................................................................................................ 26
Remove................................................................................................................................................................. 26
GEN III V8 Engine............................................................................................................................................ 26
All AWD............................................................................................................................................................ 27
Disassemble......................................................................................................................................................... 27
Inspect .................................................................................................................................................................. 29
Reassemble.......................................................................................................................................................... 30
Reinstall................................................................................................................................................................ 32