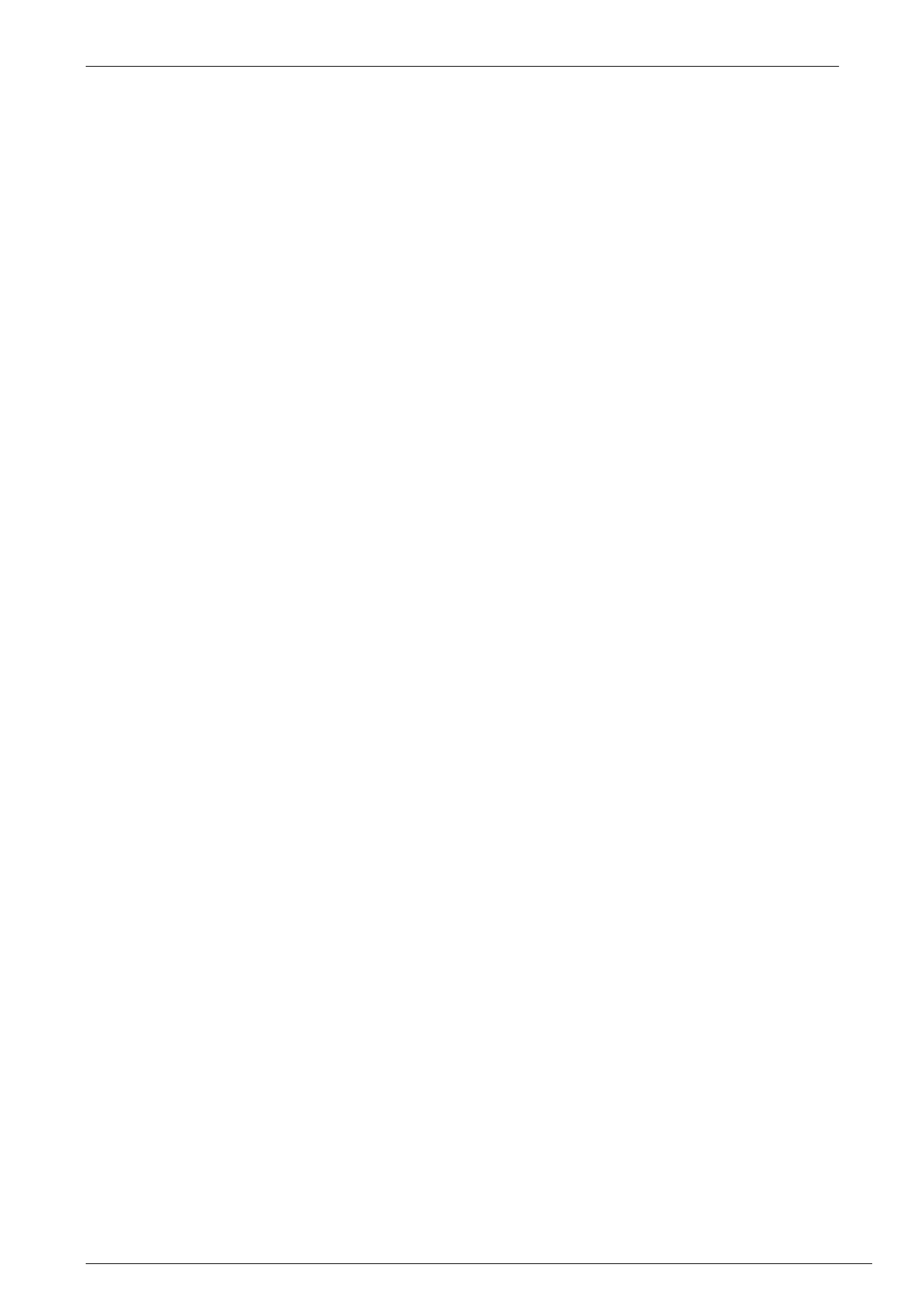
Diagnostics – All ABS 8.0 Variants Page 5B10 – 1
Page 5B10 – 2
Conditions for Running the DTC........................................................................................................................ 31
C0035 00 – C0040 00...................................................................................................................................... 31
C0035 05 – C0040 05...................................................................................................................................... 31
C0035 0F – C0040 0F...................................................................................................................................... 32
C0035 28 – C0040 28...................................................................................................................................... 32
C0035 64 – C0040 64...................................................................................................................................... 32
Conditions for Setting the DTC........................................................................................................................... 32
Action Taken When the DTC Sets ...................................................................................................................... 32
Conditions for Clearing the DTC ........................................................................................................................ 32
Additional Information......................................................................................................................................... 32
Test Description................................................................................................................................................... 33
DTC C0035 or C0040 Diagnostic Table.............................................................................................................. 33
6.3 DTC C0045 or C0050 – Rear Wheel Speed Sensor Circuit Fault......................................................................35
DTC Descriptors................................................................................................................................................... 35
Diagnostic Fault Information .............................................................................................................................. 35
Circuit/System Description................................................................................................................................. 35
Conditions for Running the DTC........................................................................................................................ 35
C0045 00 – C0050 00...................................................................................................................................... 35
C0045 05 – C0050 05...................................................................................................................................... 35
C0045 0F – C0050 0F...................................................................................................................................... 36
C0045 28 – C0050 28...................................................................................................................................... 36
C0045 64 – C0050 64...................................................................................................................................... 36
Conditions for Setting the DTC........................................................................................................................... 36
Action Taken When the DTC Sets ...................................................................................................................... 36
Conditions for Clearing the DTC ........................................................................................................................ 36
Additional Information......................................................................................................................................... 36
Test Description................................................................................................................................................... 37
DTC C0045 or C0050 Diagnostic Table.............................................................................................................. 37
6.4 DTC C0060, C0065, C0070, C0075 – Hydraulic Modulator Front Solenoid Fault............................................ 39
DTC Descriptors................................................................................................................................................... 39
Diagnostic Fault Information .............................................................................................................................. 39
Circuit Description............................................................................................................................................... 39
Conditions for Running the DTC........................................................................................................................ 39
Conditions for Setting the DTC........................................................................................................................... 39
Action Taken When the DTC Sets ...................................................................................................................... 40
Conditions for Clearing the DTC ........................................................................................................................ 40
Additional Information......................................................................................................................................... 40
Test Description................................................................................................................................................... 40
DTC C0060, C0065, C0070, C0075 Diagnostic Table......................................................................................... 41
6.5 DTC C0080, C0085, C0090, C0095 – Hydraulic Modulator Rear Solenoid Fault ............................................. 42
DTC Descriptors................................................................................................................................................... 42
4 Channel ABS 8.0........................................................................................................................................... 42
3 Channel ABS 8.0........................................................................................................................................... 42
Diagnostic Fault Information .............................................................................................................................. 42
Circuit Description............................................................................................................................................... 43
Conditions for Running the DTC........................................................................................................................ 43
Conditions for Setting the DTC........................................................................................................................... 43
Action Taken When the DTC Sets ...................................................................................................................... 43
Conditions for Clearing the DTC ........................................................................................................................ 43
Additional Information......................................................................................................................................... 43
Test Description................................................................................................................................................... 43
DTC C0080, C0085, C0090, C0095 Diagnostic Table......................................................................................... 44
6.6 DTC C0110 – Hydraulic Modulator Pump Motor Circuit Fault.......................................................................... 45
DTC Descriptors................................................................................................................................................... 45
Diagnostic Fault Information .............................................................................................................................. 45
Circuit Description............................................................................................................................................... 45
Conditions for Running the DTC........................................................................................................................ 45
Conditions for Setting the DTC........................................................................................................................... 45
Action Taken When the DTC Sets ...................................................................................................................... 45
Conditions for Clearing the DTC ........................................................................................................................ 45