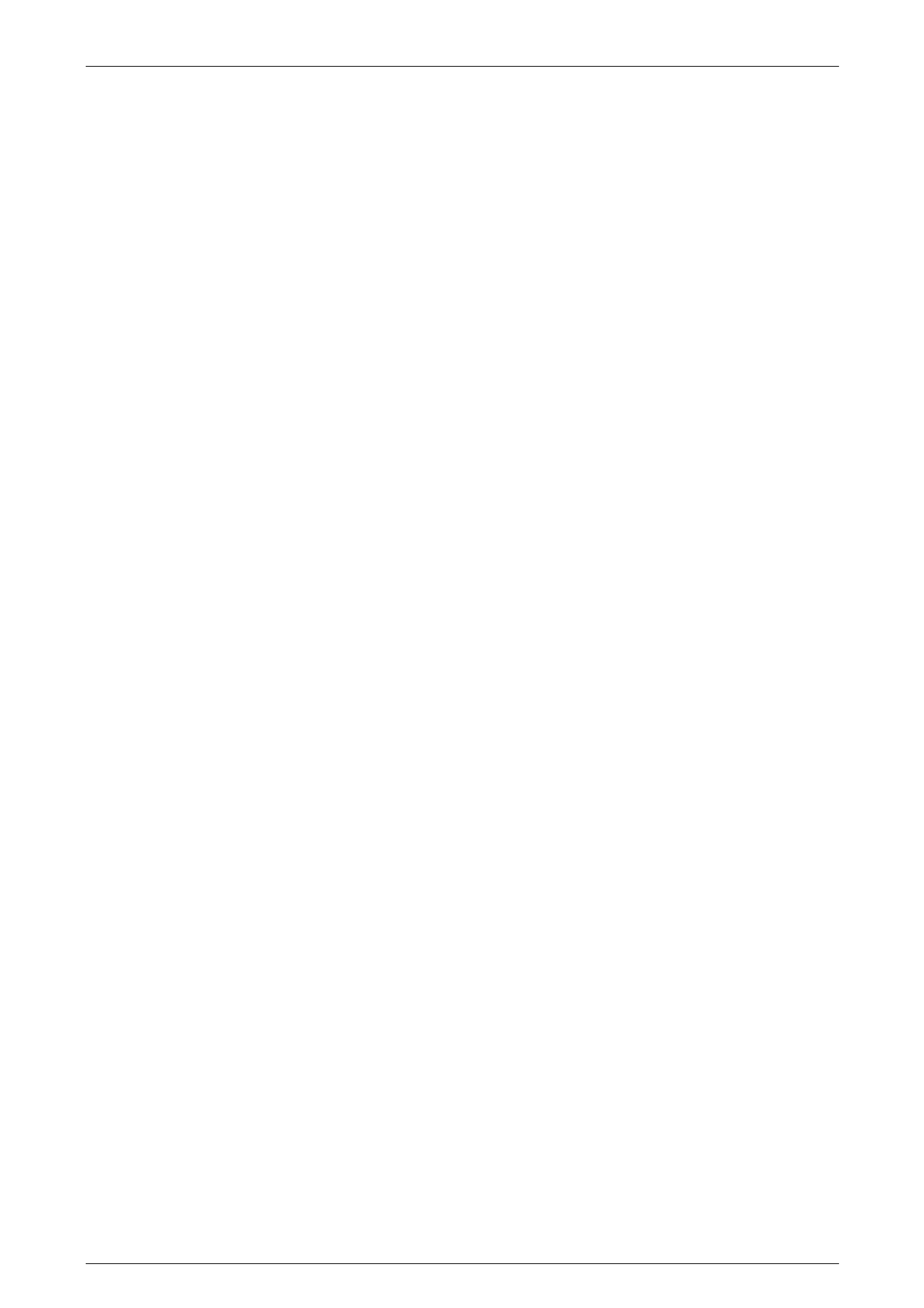
Manual Transmission – GEN III V8 Page 7B2-8
Legend – Transmission Components
1 Plate, Transmission Adaptor
2 Plug
3 Pin, Dowel (2 places)
4 Pin, Dowel (2 places)
5 Bushing, Shift Rail
6 Seal, Input Shaft
7 Shim, Input Shaft
8 Cup, Input Shaft Bearing
9 Bearing, Input Shaft Tapered
10 Shaft, Input
11 Cup, Input Shaft Bearing
12 Blocker Ring, 4th Gear
13 Ring, Snap
14 Synchroniser Assembly, 3rd/4th
15 Spring, 3rd/4th Synchroniser
16 Key, 3rd/4th Synchroniser
17 Hub, 3rd/4th Synchroniser
18 Ring, 3rd/4th Synchroniser
19 Blocker Ring, 3rd Gear
20 Gear, 3rd Speed
21 Bearing, 3rd Gear Needle
22 Bearing, Mainshaft Small Tapered
23 Mainshaft
24 Bearing, 2nd Gear Needle
25 Gear, 2nd Speed
26 Washer, Thrust
27 Cone, Inner
28 Cone, Friction
29 Blocker Ring, 2nd Gear
30 Synchroniser Assembly, 1st/2nd
31 Spring, 1st/2nd Synchroniser
32 Key, 1st/2nd Synchroniser
33 Hub, 1st/2nd Synchroniser
34 Ring, 1st/2nd Synchroniser
35 Blocker Ring, 1st Gear
36 Cone, Friction
37 Cone, Inner
38 Washer, Thrust
39 Ring, Snap
40 Bearing, 1st Gear Needle
41 Gear, 1st Speed
42 Bearing, Mainshaft Large Tapered
43 Cup, Mainshaft Bearing
44 Case, Transmission
45 Bolt, Shift Lever Guide
46 Bolt, Shift Lever Guide
47 Bolt, Shift Detent Cover
48 Cover, Shift Detent
49 Bushing, Shift Rail
50 Pin, Front Offset Lever Roll
51 Lever, Front Offset
52 Spring, Shift Detent
53 Ball, Shift Detent
54 Bolt, Shift Guide Plate
55 Plate, Shift Guide
56 Enhancer, Shift
57 Magnet (2 places)
58 Pin, Dowel (2 places)
59 Switch, Back-Up Lamp
60 Plug, Fill
61 Gear, 5th/6th Driven
62 Synchroniser Assembly, Reverse
63 Spring, Reverse Synchroniser
64 Key, Reverse Synchroniser
65 Hub, Reverse Synchroniser
66 Ring, Reverse Synchroniser
67 Retainer, Reverse Synchroniser Key
68 Washer, Thrust
69 Ring, Snap
70 Blocker Ring, Reverse Gear
71 Washer, Wave
72 Bearing, Reverse Gear Needle
73 Gear, Reverse
74 Washer, Thrust
75 Ring, Snap
76 Spacer
77 Bearing, Rear Mainshaft Tapered
78 Spacer
79 Ring, Snap
80 Ring, Snap
81 Ring, Speedometer Pulse
82 Ring, Snap
83 Ring, Snap
84 Cup, Mainshaft Bearing Rear
85 Housing, Transmission Extension
86 Sensor, Electronic Speed
87 Bolt, Speed Sensor
88 Gasket, Shifter Assembly Cover
89 Bushing, Shift Rail
90 Lever, Rear Offset Shift
91 Pin, Rear Offset Shift Lever Roll
92 Cup, Isolator
93 Shifter Assembly
94 Bolt, Shifter Assembly
95 Sleeve, Insulating
95a Distance Piece, Shift Cover Bolt
96 Cover, Shifter Assembly
97 Screw, Shifter Assembly Cover
98 Boot, Shifter
99 Seal and Boot, Rear Output
100 Bolt, Transmission Extension Housing
101 Plug, Drain
102 Shim, Countershaft
103 Cup, Countershaft Bearing
104 Bearing, Countershaft Tapered
105 Countershaft
106 Bearing, Countershaft Tapered
107 Cup, Countershaft Bearing
108 Washer, Thrust
109 Gear, 6th Drive
110 Bearing, 6th Gear Needle
111 Fork, Reverse Shift
112 Pad, Reverse Shift Fork
113 Circlip
114 Blocker Ring, 6th Gear
115 Spacer
116 Ring, Snap
117 Synchroniser Assembly, 5th/6th
118 Spring, 5th/6th Synchroniser
119 Key, 5th/6th Synchroniser
120 Hub, 5th/6th Synchroniser
121 Ring, 5th/6th Synchroniser
122 Fork, 5th/6th Shift
123 Pad, 5th/6th Shift Fork
124 Circlip
125 Blocker Ring, 5th Gear
126 Gear, 5th Drive
127 Bearing, 5th Gear Needle
128 Extension, Countershaft
129 Bearing, Countershaft Extension
Tapered
130 Cup, Countershaft Extension Bearing
131 Shim, Countershaft Extension
132 Funnel, Oil
133 Bolt, Reverse Idler Shaft Bracket
134 Bracket, Reverse Idler Shaft
135 Washer, Reverse Idler Gear Thrust
136 Gear, Reverse Idler
137 Bearing, Reverse Idler Gear Roller
138 Shaft, Reverse Idler Gear
139 Washer, Reverse Idler Gear Thrust
140 Rail Assembly, 5th/6th, Reverse Shift
141 Pin, Roll
142 Collar
143 Rail, Shift
144 Lever, 5th/6th Shift Rail
145 Pad, 5th/6th Shift Rail Lever
146 Bushing, 5th/6th Shift Rail Lever
147 Pin, Roll
148 Lever, Reverse Shift Rail
149 Rail Assembly, 1st/2nd, 3rd/4th Shift
150 Fork, 1st/2nd Shift
151 Pad, 1st/2nd Shift Fork
152 Link, Shift
153 Rail, 1st/2nd 3rd/4th Shift
154 Pin, Roll
155 Pin, Selector
156 Plate, Interlock
157 Link, Shift
158 Fork, 3rd/4th Shift
159 Pad, 3rd/4th Shift Fork
160 Solenoid, Reverse Lockout
161 O-Ring, Reverse Lockout Solenoid
162 Body Assembly, Reverse Lockout
163 Bolt, Reverse Lockout Assembly
164 O-Ring, Reverse Lockout Asm
165 Circlip
166 Plunger, Reverse Lockout
167 Spring, Reverse Lockout Outer
168 Collar, Reverse Lockout
169 ‘C’ Clip
170 Spring, Reverse Lockout Inner
171 Body, Reverse Lockout
172 Housing, Clutch
173 Bolt, Clutch Housing to Adaptor
174 Assembly, Clutch Slave Cylinder
175 Bolt, Clutch Slave Cylinder
176 Bolt, Transmission Adaptor Plate
177 Spacer
178 Tube, Vent
179 Fitting, Vent Tube
180 O-Ring, Mainshaft
Page 7B2- 8