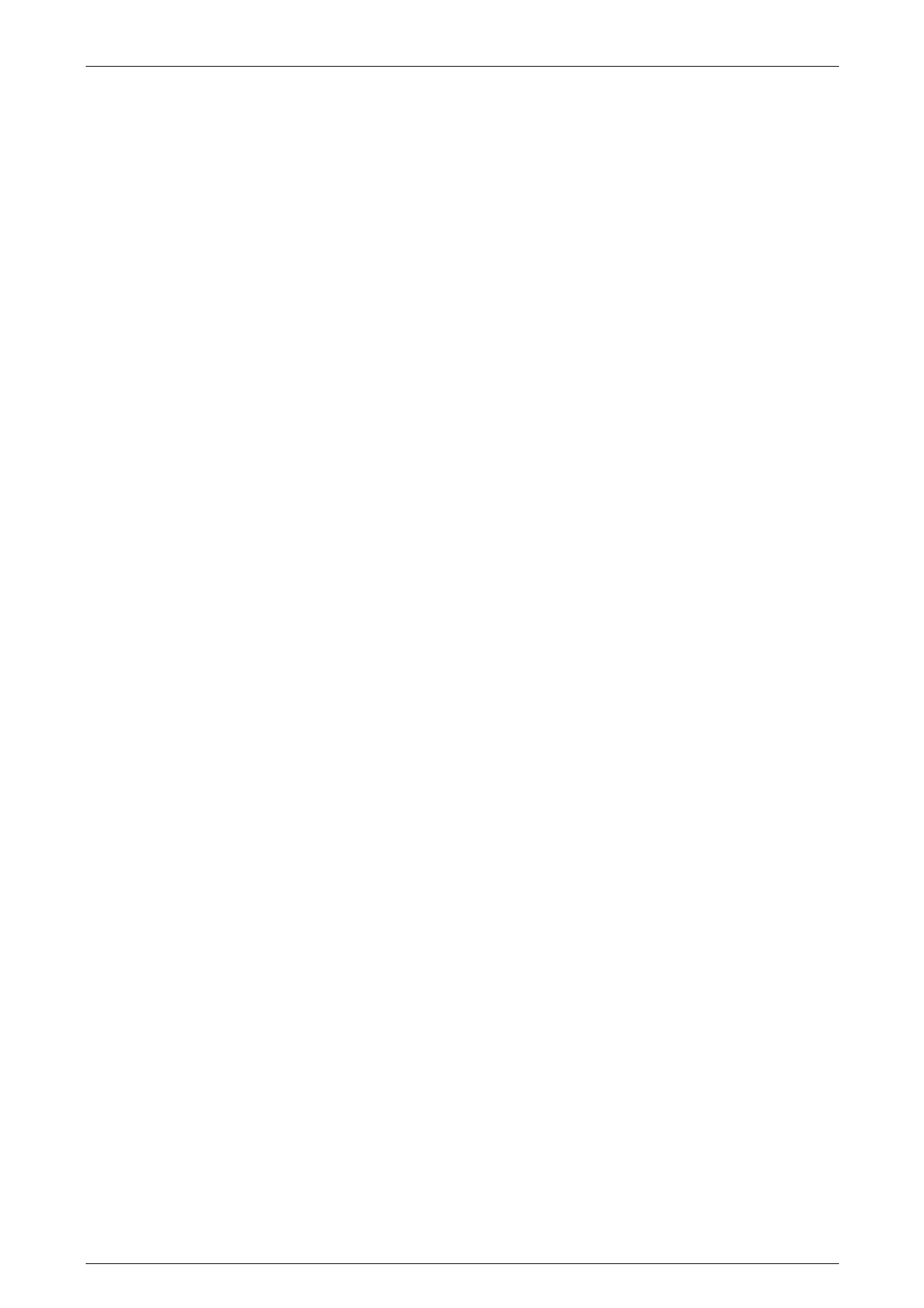
Automatic Transmission – 4L65E – On-vehicle Servicing Page 7D4–2
Page 7D4–2
3.6 Shift Selector Assembly, AWD ........................................................................................................................... 38
Remove................................................................................................................................................................. 38
Disassemble......................................................................................................................................................... 39
Lower Housing Assembly................................................................................................................................. 39
Patch Harness and Switch............................................................................................................................... 42
Upper Cover, Boot and Selector Knob............................................................................................................. 42
Reinstall................................................................................................................................................................ 42
3.7 Neutral Start and Back-up Lamp Switch, Except AWD ..................................................................................... 43
Remove................................................................................................................................................................. 43
Reinstall................................................................................................................................................................ 43
Adjust.................................................................................................................................................................... 44
3.8 Neutral Start and Back-up Lamp Switch, AWD ................................................................................................. 45
Remove................................................................................................................................................................. 45
Reinstall................................................................................................................................................................ 46
Adjust.................................................................................................................................................................... 46
3.9 Vehicle Speed Sensor, Except AWD.................................................................................................................. 47
Remove................................................................................................................................................................. 47
Reinstall................................................................................................................................................................ 47
3.10 Vehicle Speed Sensor, AWD............................................................................................................................... 48
Remove................................................................................................................................................................. 48
Reinstall................................................................................................................................................................ 48
3.11 Manual Shaft Oil Seal .......................................................................................................................................... 49
Replace................................................................................................................................................................. 49
3.12 Transmission Support and Mount, Except Coupe and AWD........................................................................... 51
Remove................................................................................................................................................................. 51
Reinstall................................................................................................................................................................ 51
3.13 Transmission Support and Mount, Coupe ......................................................................................................... 53
Remove................................................................................................................................................................. 53
Reinstall................................................................................................................................................................ 53
3.14 Extension Housing and Rear Bush, Except AWD............................................................................................. 55
Remove................................................................................................................................................................. 55
Reinstall................................................................................................................................................................ 56
3.15 Extension Housing Oil Seal, Except AWD......................................................................................................... 57
Replace................................................................................................................................................................. 57
3.16 Transmission Support and Adaptor Housing, AWD......................................................................................... 58
Remove and Reinstall.......................................................................................................................................... 58
3.17 Shift Solenoid Locations..................................................................................................................................... 59
Location and Identification ................................................................................................................................. 59
3.18 1 – 2 Accumulator Assembly.............................................................................................................................. 60
Remove................................................................................................................................................................. 60
Clean and Inspect................................................................................................................................................ 60
Reinstall................................................................................................................................................................ 60
3.19 Control Valve Body Harness............................................................................................................................... 61
Remove................................................................................................................................................................. 61
Reinstall................................................................................................................................................................ 63
3.20 Control Valve Body.............................................................................................................................................. 65
Remove................................................................................................................................................................. 65
Disassemble, Clean, Inspect and Reassemble.................................................................................................. 66
Reinstall................................................................................................................................................................ 66
3.21 Spacer Plate, Check Balls, Filter Screens and 3 – 4 Accumulator .................................................................. 70
Remove................................................................................................................................................................. 70
Clean and Inspect................................................................................................................................................ 71
Reinstall................................................................................................................................................................ 72
3.22 Filler Tube and Breather Hose............................................................................................................................ 75
Remove................................................................................................................................................................. 75
Reinstall................................................................................................................................................................ 76