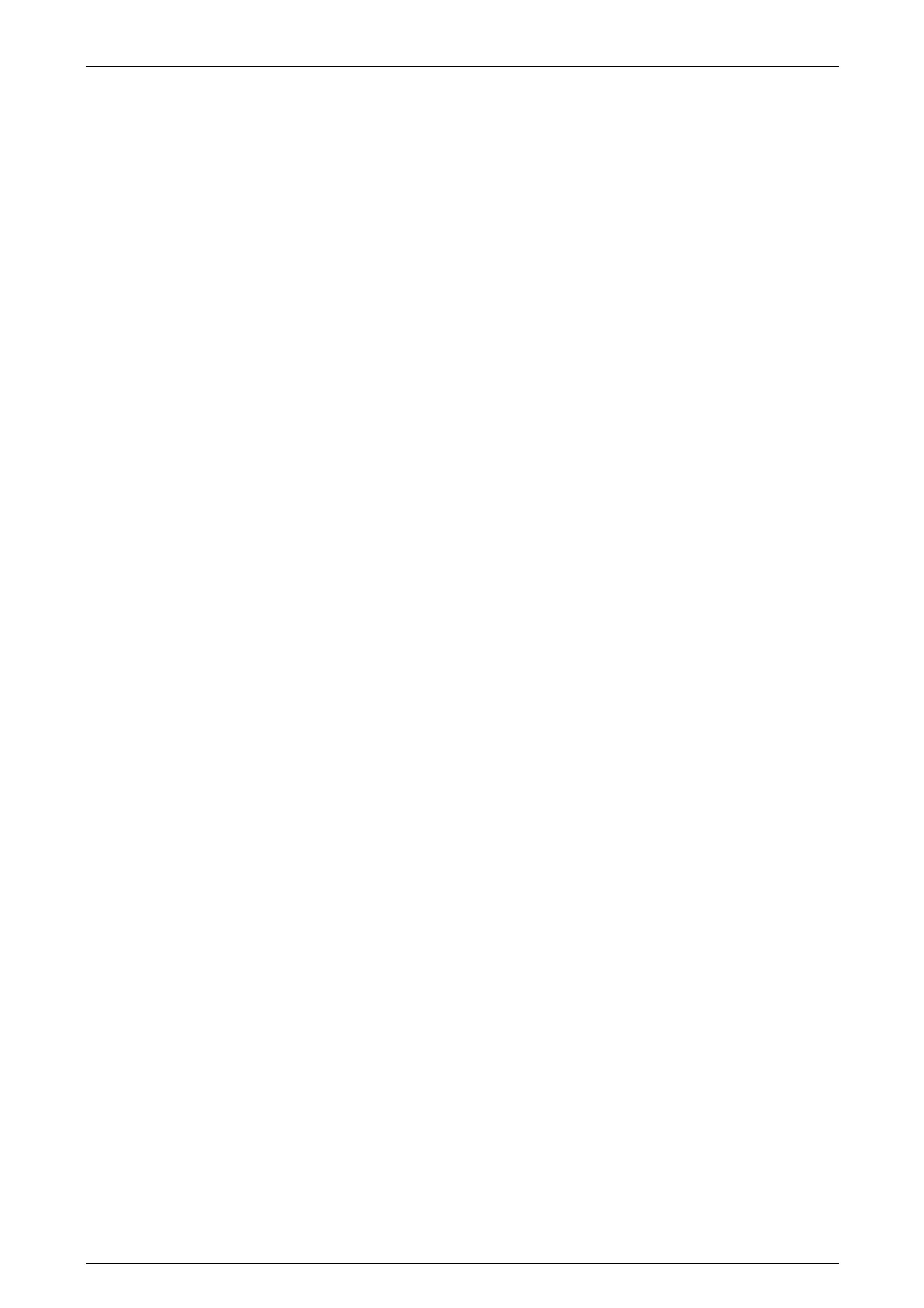
Rear Suspension 4A1 – 2
4A1-2
3.10 Rear Shock Absorbers and/or Bushing............................................................................................................. 54
Remove................................................................................................................................................................. 54
Lower Bushing, Replace ..................................................................................................................................... 55
Reinstall................................................................................................................................................................ 56
3.11 Additional Control Arm ....................................................................................................................................... 57
Inspect .................................................................................................................................................................. 57
Remove................................................................................................................................................................. 58
Disassemble......................................................................................................................................................... 58
Reassemble.......................................................................................................................................................... 58
Reinstall................................................................................................................................................................ 59
3.12 Rear Wheel Alignment Checking........................................................................................................................ 60
Camber and Toe Check....................................................................................................................................... 60
Preliminary Checks and Information................................................................................................................. 60
Rear Wheel Toe Adjustment ............................................................................................................................... 61
4 Service Operations – Automatic Level Ride Suspension ................................................................62
4.1 Initial Air Charge.................................................................................................................................................. 62
4.2 Air Leak Test ........................................................................................................................................................ 63
4.3 Relieving System Air Pressure........................................................................................................................... 64
4.4 Compressor Assembly........................................................................................................................................ 65
Remove................................................................................................................................................................. 65
Disassemble......................................................................................................................................................... 66
Reassemble.......................................................................................................................................................... 66
Reinstall................................................................................................................................................................ 67
4.5 Air Lines ............................................................................................................................................................... 68
Remove................................................................................................................................................................. 68
Reinstall................................................................................................................................................................ 69
4.6 Automatic Level Ride Shock Absorber.............................................................................................................. 70
Remove................................................................................................................................................................. 70
Reinstall................................................................................................................................................................ 71
4.7 Ride Height Sensor.............................................................................................................................................. 72
Remove................................................................................................................................................................. 72
Reinstall................................................................................................................................................................ 73
5 Diagnosis......................................................................................................................................................74
5.1 Checking and Testing Shock Absorbers........................................................................................................... 74
Leakage Criteria................................................................................................................................................... 74
5.2 Diagnosis – Automatic Level Ride Suspension................................................................................................ 75
Equipment ............................................................................................................................................................ 75
Ride Height Sensor Reset................................................................................................................................... 75
5.3 Preliminary Diagnostic Procedure ..................................................................................................................... 76
5.4 Compressor Assembly Test – Motor.................................................................................................................. 77
5.5 Compressor Assembly Test – Solenoid ............................................................................................................ 78
5.6 Ride Height Sensor Test – Compressor ............................................................................................................ 79
5.7 Ride Height Sensor Test – Solenoid .................................................................................................................. 80
5.8 Wiring Diagram – Automatic Level Ride Suspension....................................................................................... 81
5.9 Wiring Harness Layout – Automatic Level Ride Suspension .......................................................................... 82
6 Specifications.......................................................................................................................................83
Rear Suspension Service Alignment Data......................................................................................................... 83
Rear Spring Details.............................................................................................................................................. 83
Rear Shock Absorber Details.............................................................................................................................. 84
Rear Stabiliser Bar Details.................................................................................................................................. 84
7 Torque Wrench Specifications............................................................................................................85
8 Special Tools ........................................................................................................................................86