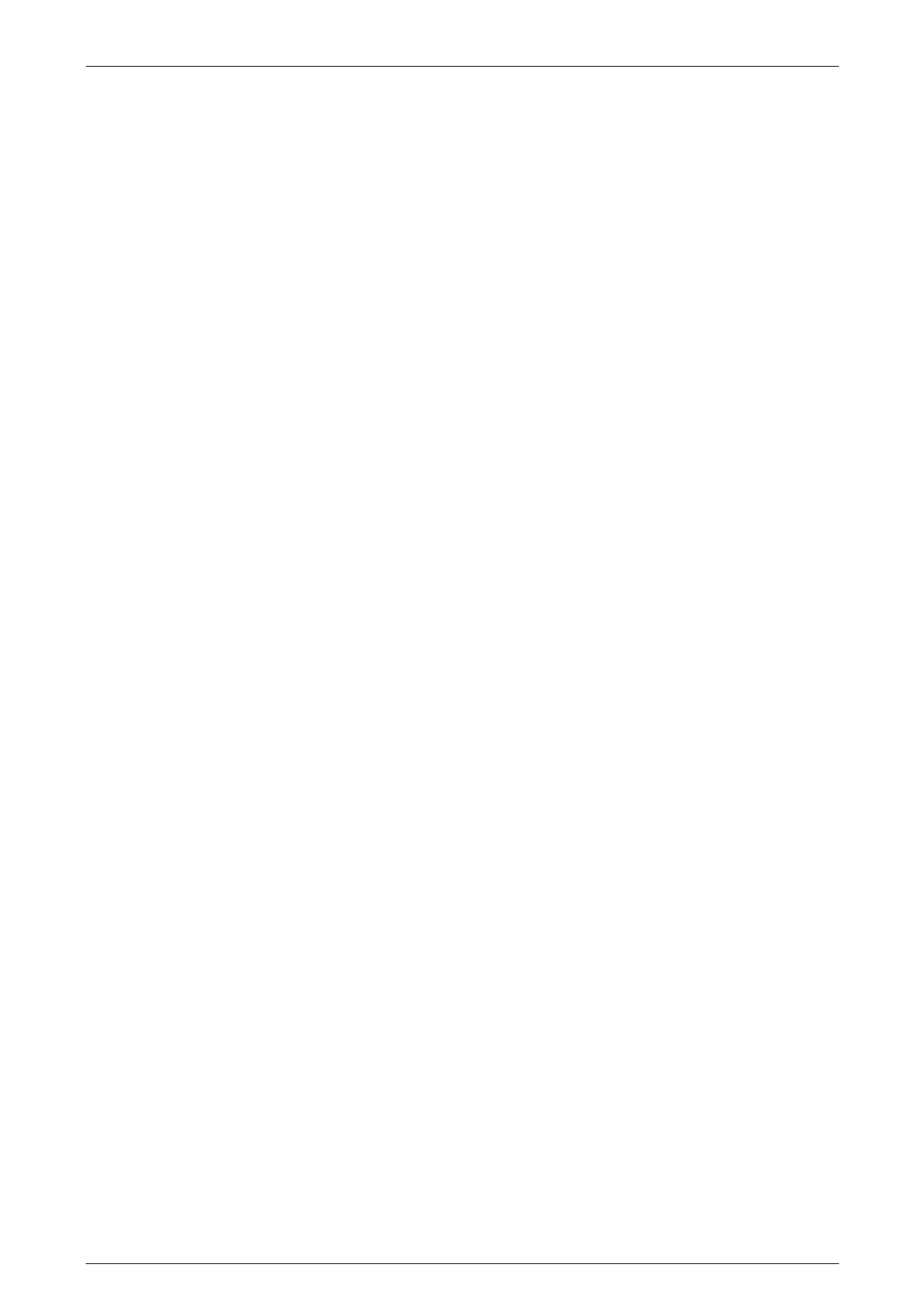
Powertrain Management – GEN III V8 – Diagnostics Page 6C3-2–6
Page 6C3-2–6
Conditions for Clearing the DTC ...................................................................................................................... 138
Test Description................................................................................................................................................. 138
DTC P0230 Diagnostic Table............................................................................................................................. 139
5.24 DTC P0135 or P0155 – Heated Oxygen Sensor Heater Control Circuit......................................................... 141
DTC Description................................................................................................................................................. 141
Circuit Description............................................................................................................................................. 141
Additional Information....................................................................................................................................... 141
Conditions for Running the DTC...................................................................................................................... 141
Current Monitor .............................................................................................................................................. 141
Resistance Out of Range............................................................................................................................... 141
Conditions for Setting the DTC......................................................................................................................... 142
Conditions for Clearing the DTC ...................................................................................................................... 142
Test Description................................................................................................................................................. 142
DTC P0135 or P0155 Diagnostic Table............................................................................................................. 142
5.25 DTC P0131, P0132, P0134, P0151, P0152, P0154, P0171, P0172, P0174 or P0175 – Heated Oxygen Sensor
Reference Circuit............................................................................................................................................... 144
DTC Description................................................................................................................................................. 144
Circuit Description............................................................................................................................................. 144
Additional Information....................................................................................................................................... 144
Conditions for Running the DTC...................................................................................................................... 145
DTC P0131, P0132, P0151 and P0152.......................................................................................................... 145
DTC P0134 and P0154 .................................................................................................................................. 145
DTC P0171, P0172, P0174 and P0175.......................................................................................................... 145
Conditions for Setting the DTC......................................................................................................................... 146
DTC P0131 and P0151 .................................................................................................................................. 146
DTC P0132 and P0152 .................................................................................................................................. 146
DTC P0134 and P0154 .................................................................................................................................. 146
DTC P0171 and P0174 .................................................................................................................................. 146
DTC P0172 and P0175 .................................................................................................................................. 146
Conditions for Clearing the DTC ...................................................................................................................... 146
DTC P0131, P0132, P0134, P0151, P0152, P0154, P0171, P0172, P0174 or P0175 Diagnostic Table.......... 146
5.26 DTC P0351, P0352, P0353, P0354, P0355, P0356, P0357 or P0358 – Ignition Control Circuits.................... 148
DTC Description................................................................................................................................................. 148
Circuit Description............................................................................................................................................. 148
Additional Information....................................................................................................................................... 148
Conditions for Running the DTC...................................................................................................................... 148
Conditions for Setting the DTC......................................................................................................................... 148
Conditions for Clearing the DTC ...................................................................................................................... 149
Test Description................................................................................................................................................. 149
DTC P0351, P0352, P0353, P0354, P0355, P0356, P0357 or P0358 Diagnostic Table................................... 149
5.27 DTC P1626, P1630 or P1631 – Immobiliser Signal.......................................................................................... 151
DTC Description................................................................................................................................................. 151
Circuit Description............................................................................................................................................. 151
Additional Information....................................................................................................................................... 151
Conditions for Running the DTC...................................................................................................................... 152
DTC P1626 .................................................................................................................................................... 152
DTC P1630 .................................................................................................................................................... 152
DTC P1631 .................................................................................................................................................... 152
Conditions for Setting the DTC......................................................................................................................... 152
DTC P1626 .................................................................................................................................................... 152
DTC P1630 .................................................................................................................................................... 152
DTC P1631 .................................................................................................................................................... 152
Conditions for Clearing the DTC ...................................................................................................................... 152
Test Description................................................................................................................................................. 152
DTC P1626, P1630 or P1631 Diagnostic Chart ................................................................................................ 152
5.28 DTC P0112, P0113, P1111 or P1112 – Intake Air Temperature Sensor Circuit ............................................. 154
DTC Description................................................................................................................................................. 154
Circuit Description............................................................................................................................................. 154
Additional Information....................................................................................................................................... 154