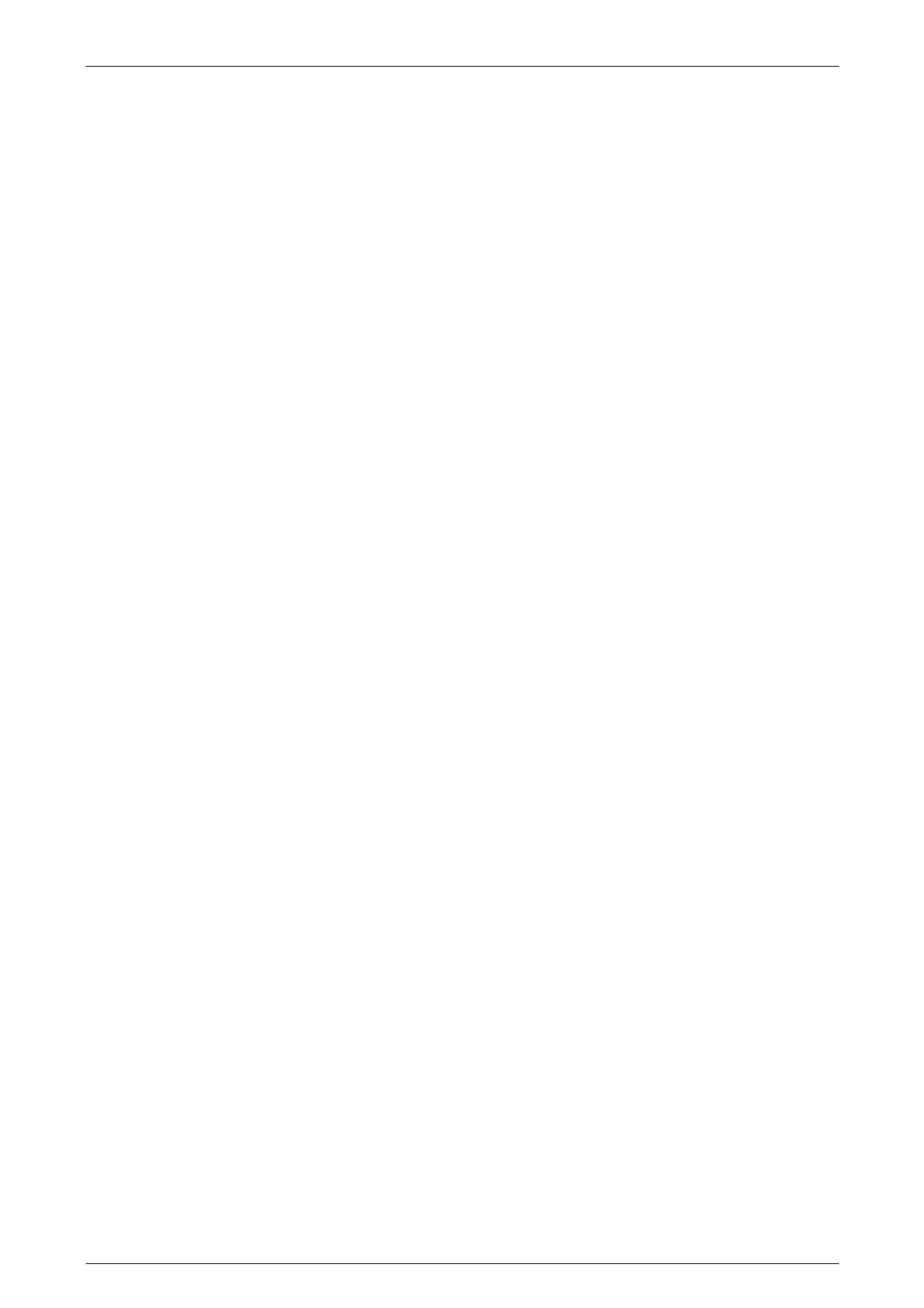
Automatic Transmission – 5L40-E – Electrical Diagnosis Page 7E – 2
Page 7E2 – 2
2 Automatic Transmission Diagnostic Information and Procedures.................................................26
2.1 Introduction.......................................................................................................................................................... 26
2.2 General Diagnostic Procedures.......................................................................................................................... 27
Diagnostic System Check – Vehicle................................................................................................................... 27
Symptoms Diagnostics ....................................................................................................................................... 27
Diagnostic Trouble Code (DTC) Tables ............................................................................................................. 27
Multiple DTCs Fault Condition............................................................................................................................ 27
2.3 Diagnostic System Check – Automatic Transmission (5L40-E) ...................................................................... 28
Description........................................................................................................................................................... 28
Diagnostic Aids.................................................................................................................................................... 28
Test Description................................................................................................................................................... 28
Diagnostic System Check – Automatic Transmission ..................................................................................... 29
3 Tech 2 – Automatic Transmission......................................................................................................30
3.1 Introduction.......................................................................................................................................................... 30
3.2 Automatic Transmission Data Lists................................................................................................................... 31
Ignition ON:...................................................................................................................................................... 31
Engine Running................................................................................................................................................ 31
F0: Transmission Data......................................................................................................................................... 31
F0: Transmission Data List Definitions ............................................................................................................. 32
F1: TCC Data......................................................................................................................................................... 35
F1: TCC Data List Definitions ........................................................................................................................... 35
F2: 1-2 Shift Data .................................................................................................................................................. 37
F2: 1-2 Shift Data List Definitions ..................................................................................................................... 37
F3: 2-3 Shift Data .................................................................................................................................................. 39
F3: 2-3 Shift Data List Definitions ..................................................................................................................... 39
F4: 3-4 Shift Data .................................................................................................................................................. 40
F4: 3-4 Shift Data List Definitions ..................................................................................................................... 41
F5: 4-5 Shift Data .................................................................................................................................................. 42
F5: 4-5 Shift Data List Definitions ..................................................................................................................... 42
F6: Pressure Control Solenoid Data ................................................................................................................... 44
F6: Pressure Control Solenoid Data................................................................................................................. 44
F7: Transmission Adapts..................................................................................................................................... 45
F0: 1-2 Adapt Data ........................................................................................................................................... 45
F1: 2-3 Adapt Data ........................................................................................................................................... 46
F2: 3-4 Adapt Data ........................................................................................................................................... 47
F3: 4-5 Adapt Data ........................................................................................................................................... 48
F4: Steady State Adapt Data............................................................................................................................ 50
F8: System Identification..................................................................................................................................... 51
3.3 Tech 2 – Output Controls.................................................................................................................................... 52
4 Automatic Transmission Diagnostic Trouble Code Charts.............................................................55
DTC P0115 – GMLAN Engine Coolant Temperature Fault (No valid GMLAN signal)..................................... 55
DTC P0120 – Throttle Position Signal (No valid GMLAN signal) ..................................................................... 57
DTC P0218 – Transmission Fluid Over-Temperature ....................................................................................... 59
DTC P0562 – System Voltage Low ..................................................................................................................... 63
DTC P0563 – System Voltage High..................................................................................................................... 66
DTC P0572 – Brake Switch ‘Stuck Off’............................................................................................................... 68
DTC P0573 – Brake Switch ‘Stuck On’............................................................................................................... 71
DTC P0601 – TCM ROM Test............................................................................................................................... 73
DTC P0602 – No Start Calibration....................................................................................................................... 75
DTC P0603 – Power-Up Copy of NVM to RAM................................................................................................... 77
DTC P0604 – RAM Test........................................................................................................................................ 79
DTC P0711 – Transmission Fluid Temperature Sensor Circuit – Performance Test ..................................... 81
DTC P0712 – Transmission Fluid Temperature Sensor Circuit – Low Input (High Temperature)................. 85
DTC P0713 – Transmission Fluid Temperature Sensor Circuit – High Input (Low Temperature)................. 87
DTC P0716 – Transmission Input Speed Sensor – Performance Signal Drop................................................ 89
DTC P0717 – Transmission Input Speed Sensor – Low Input, No Activity..................................................... 93
DTC P0722 – Transmission Output Speed Sensor – Low Input....................................................................... 97