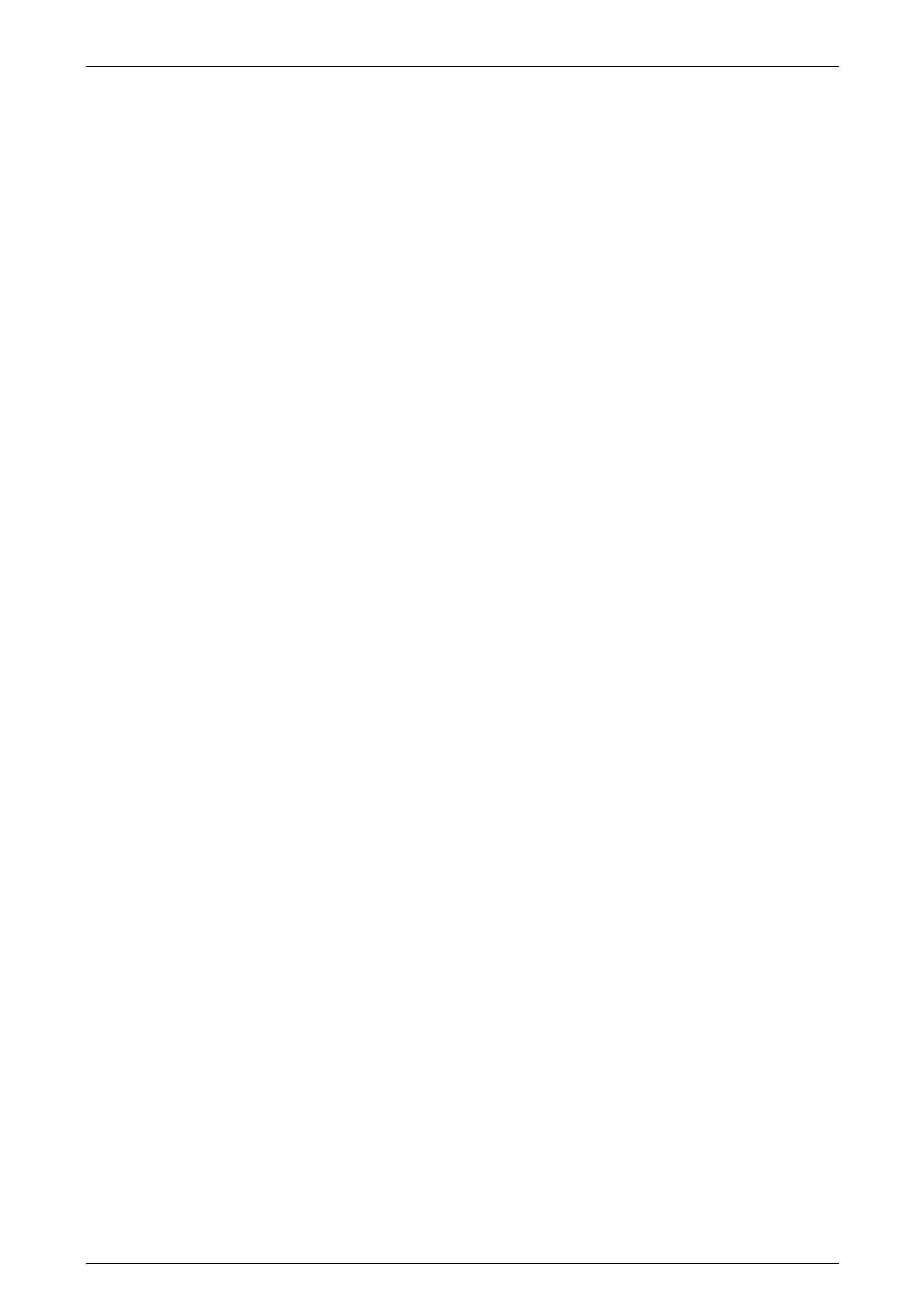
Automatic Transmission – 5L40-E – On-Vehicle Servicing 7E4 – 2
7E4 – 2
3.5 Fluid Pressure Test Plug..................................................................................................................................... 30
Replace................................................................................................................................................................. 30
3.6 Transmission Mount and Mount Plate ............................................................................................................... 31
Inspect .................................................................................................................................................................. 31
Remove................................................................................................................................................................. 32
Reinstall................................................................................................................................................................ 33
3.7 Output Drive Flange and Oil Seal....................................................................................................................... 34
Remove................................................................................................................................................................. 34
Reinstall................................................................................................................................................................ 36
3.8 Extension Housing .............................................................................................................................................. 38
Remove................................................................................................................................................................. 38
Reinstall................................................................................................................................................................ 39
3.9 Transmission Internal Electrical Harness.......................................................................................................... 40
Replace................................................................................................................................................................. 40
3.10 Manual Shaft Oil Seal .......................................................................................................................................... 43
Replace................................................................................................................................................................. 43
3.11 Manual Shaft Position Switch............................................................................................................................. 45
Remove................................................................................................................................................................. 45
Reinstall................................................................................................................................................................ 47
3.12 Input Speed Sensor............................................................................................................................................. 49
Replace................................................................................................................................................................. 49
3.13 Output Speed Sensor.......................................................................................................................................... 50
Replace................................................................................................................................................................. 50
3.14 1-2 Shift Solenoid................................................................................................................................................. 51
Replace................................................................................................................................................................. 51
3.15 2-3 Shift Solenoid................................................................................................................................................. 52
Replace................................................................................................................................................................. 52
3.16 4-5 Shift Solenoid................................................................................................................................................. 54
Replace................................................................................................................................................................. 54
3.17 Pressure Control Solenoid.................................................................................................................................. 55
Replace................................................................................................................................................................. 55
3.18 Torque Converter Clutch (TCC) PWM Solenoid................................................................................................ 57
Replace................................................................................................................................................................. 57
3.19 Solenoid Leak Testing......................................................................................................................................... 59
3.20 Control Valve Body and Accumulator Assembly.............................................................................................. 60
3.21 Transmission Control Module (TCM)................................................................................................................. 61
Remove................................................................................................................................................................. 61
Reinstall................................................................................................................................................................ 61
TCM Programming Procedure............................................................................................................................ 62
3.22 5L40-E Automatic Transmission ........................................................................................................................ 63
Remove................................................................................................................................................................. 63
Reinstall................................................................................................................................................................ 68
Transmission Final Test and Inspection............................................................................................................ 70
3.23 Torque Converter and/or Seal............................................................................................................................. 71
Replace................................................................................................................................................................. 71
4 Specifications.......................................................................................................................................74
5 Torque Wrench Specifications............................................................................................................76
6 Special Tools ........................................................................................................................................77