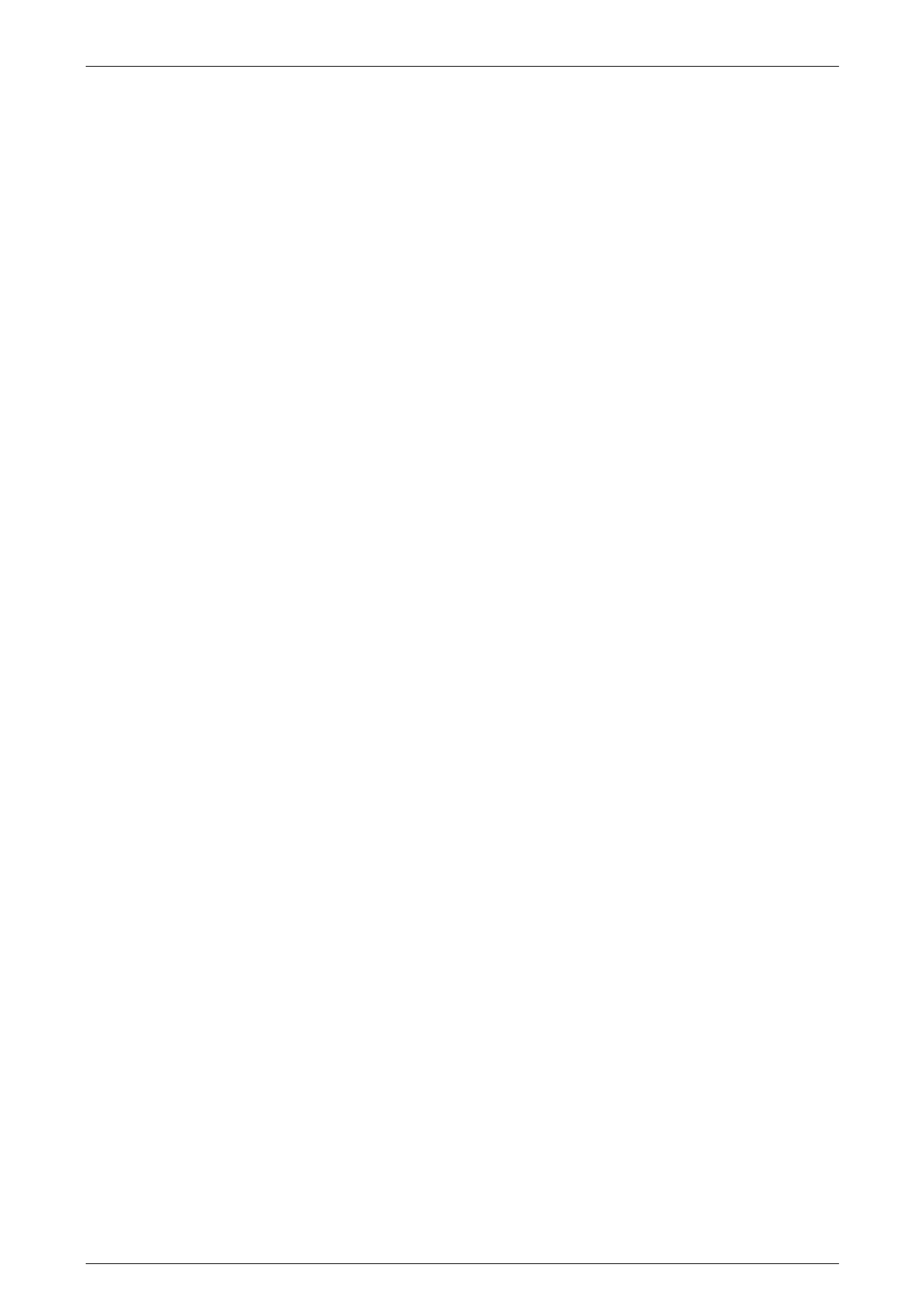
Steering Page 9–2
Page 9–2
3 Service Operations...............................................................................................................................24
3.1 Steering Wheel Assembly................................................................................................................................... 24
Remove................................................................................................................................................................. 24
Disassemble......................................................................................................................................................... 26
Rear Cover....................................................................................................................................................... 26
Steering Wheel Inflatable Restraint Retaining Clip........................................................................................... 27
Horn Bar Stereo Control Switch Assembly....................................................................................................... 28
Active Select Shift Control Paddle Assembly................................................................................................... 29
Reassemble.......................................................................................................................................................... 30
Active Select Shift Control Paddle Assembly................................................................................................... 30
Horn Bar Stereo Control Switch Assembly....................................................................................................... 30
Rear Cover....................................................................................................................................................... 31
Reinstall................................................................................................................................................................ 31
3.2 Steering Column Covers..................................................................................................................................... 32
Remove................................................................................................................................................................. 32
Reinstall................................................................................................................................................................ 32
3.3 Ignition Barrel and Lock Cylinder....................................................................................................................... 33
Remove................................................................................................................................................................. 33
Reinstall................................................................................................................................................................ 34
3.4 Ignition Switch ..................................................................................................................................................... 35
Remove................................................................................................................................................................. 35
Test ....................................................................................................................................................................... 35
Reinstall................................................................................................................................................................ 36
3.5 Steering Column Assembly ................................................................................................................................ 37
Remove................................................................................................................................................................. 37
Inspect .................................................................................................................................................................. 39
Disassemble......................................................................................................................................................... 39
Non-serviced Components............................................................................................................................... 39
Clock Spring Assembly .................................................................................................................................... 39
Tilt/ Reach Handle............................................................................................................................................ 40
Reinstall................................................................................................................................................................ 40
3.6 Power Steering Fluid Level Check ..................................................................................................................... 41
V6 Engine ............................................................................................................................................................. 41
GEN III V8 Engine................................................................................................................................................. 41
3.7 Drive Belt Adjustment ......................................................................................................................................... 42
3.8 Tie-rod Socket...................................................................................................................................................... 43
Remove................................................................................................................................................................. 43
Reinstall................................................................................................................................................................ 43
3.9 Steering Gear Boot.............................................................................................................................................. 44
Remove................................................................................................................................................................. 44
Reinstall................................................................................................................................................................ 45
3.10 Power Steering Gear Assembly.......................................................................................................................... 46
Remove................................................................................................................................................................. 46
Disassemble......................................................................................................................................................... 48
Clean and Inspect ............................................................................................................................................ 56
Reassemble.......................................................................................................................................................... 57
Reinstall................................................................................................................................................................ 67
3.11 Power Steering Fluid Reservoir.......................................................................................................................... 69
Remove................................................................................................................................................................. 69
V6 Engine......................................................................................................................................................... 69
GEN III V8 Engine............................................................................................................................................ 70
Reinstall................................................................................................................................................................ 70
V6 and GEN III V8 Engine................................................................................................................................ 70