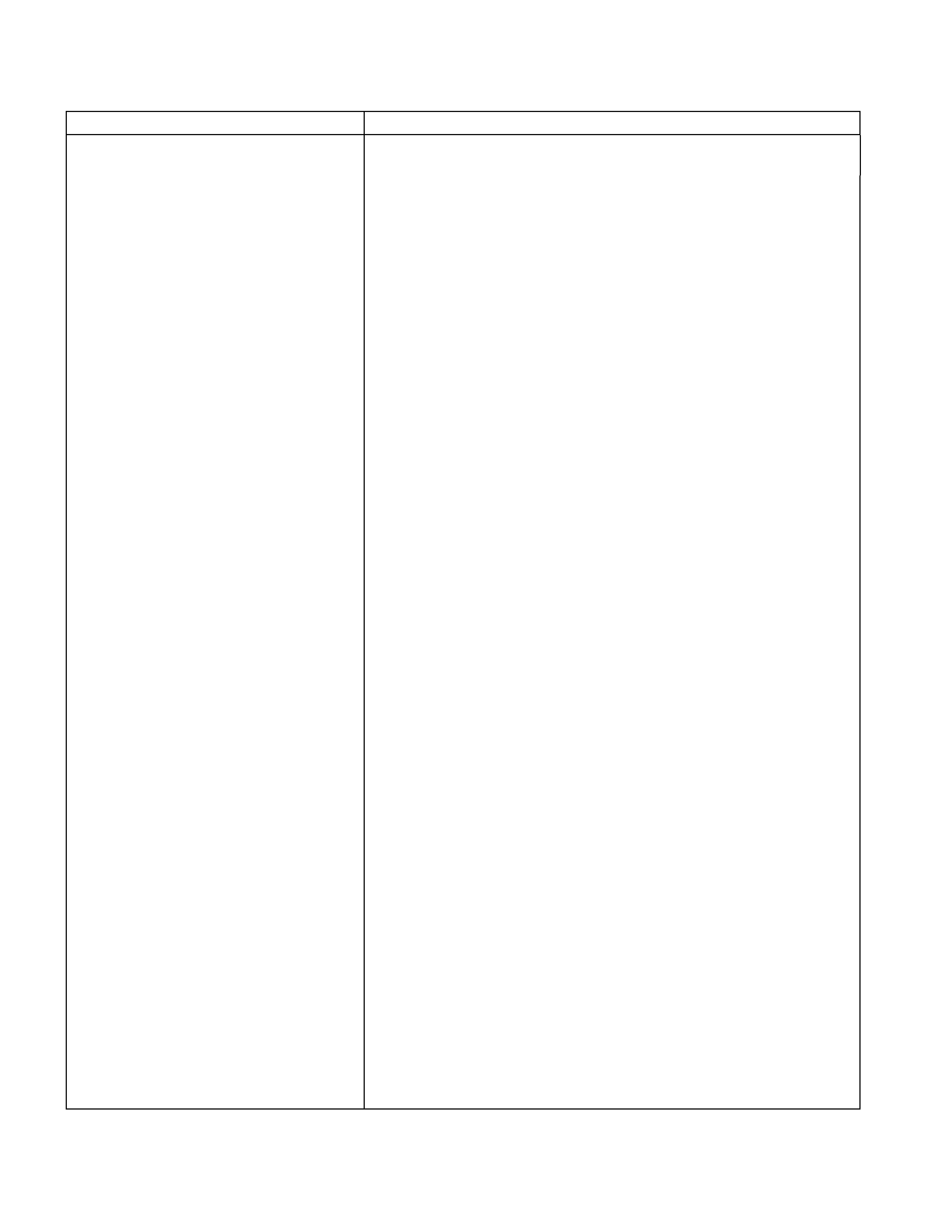
MAIN DATA AND SPECIFICATIONS
Engine - General C22NE
Engine type Four-cycle, water cooled cross-flow with single over head camshaft
Micro-computer control, fuel injection
Combustion chamber type (Volume) Hemispherical (43.3cm3)
Timing train system Belt drive
No.of cylinders-bore × stroke mm (in) 4-86.0×94.6 (3.39×3.72)
Bore Spacing (C/L to C/L) 93.0 mm
Firing Order 1-3-4-2
Bore×Stroke 86.0×94.6mm
Total piston displacement cm3 (in3) 2,198 (134.39)
Combustion Chamber Volume 43.3 cm
No.of piston ring compression ring : 2 ,oil ring :1
Compression pressure kg/cm2 (psi/pa) 17.8 (253/1746)
Ignition timing (BTDC) No adjustment
Idling speed :rpm (WO/AC,W/AC)
Acoff 825
Valve clearances (At cold)
Intake mm (in) 0 (0) (Hydraulic valve lash adjustment)
Exhaust mm (in) 0 (0) (Hydraulic valve lash adjustment )
Intake valves
Open at (BTDC) deg 29
Close at (ABDC) deg 65
Exhaust valves
Open at (BBDC) deg 66
Close at (ATDC) deg 29
Ignition system Fully transistorized battery ignition
Distributor type Not applicable, Electronic Spark Timing control
Distributor advance type Not applicable, Electronic Spark Timing control
Spark plug type RN9YC4
Spark plug gap mm (in) 1.0--1.1 (0.039--0.043)
Lubrication system
Lubricating method Fully flow pressure circulation
Special engine oil (API grade) SE,SF,SG or SH grade
Oil pressure (psi/Pa) rpm (21.3/147)/825 (SAE 10W-30/API SE grade) engine oil after warm-
up
Oil pump type Gear
Oil filter type Cartridge full flow
Oil capacity lit. (US/UK gal.) with Oil Filter change 4.5litres
without Oil Filter change 4.25 (1.07/0.93) litres
Cooling system
Radiator type Corrugated fin with reserve tank
Coolant capacity lit. (US/UK gal.) 2.3 (0.66/0.55)
Water pump type Centrifugal
Thermostat Wax pellet with jiggle hole
Fuel system Electronically controlled Multi Port Fuel Injection System
Fuel pump ty pe Electric