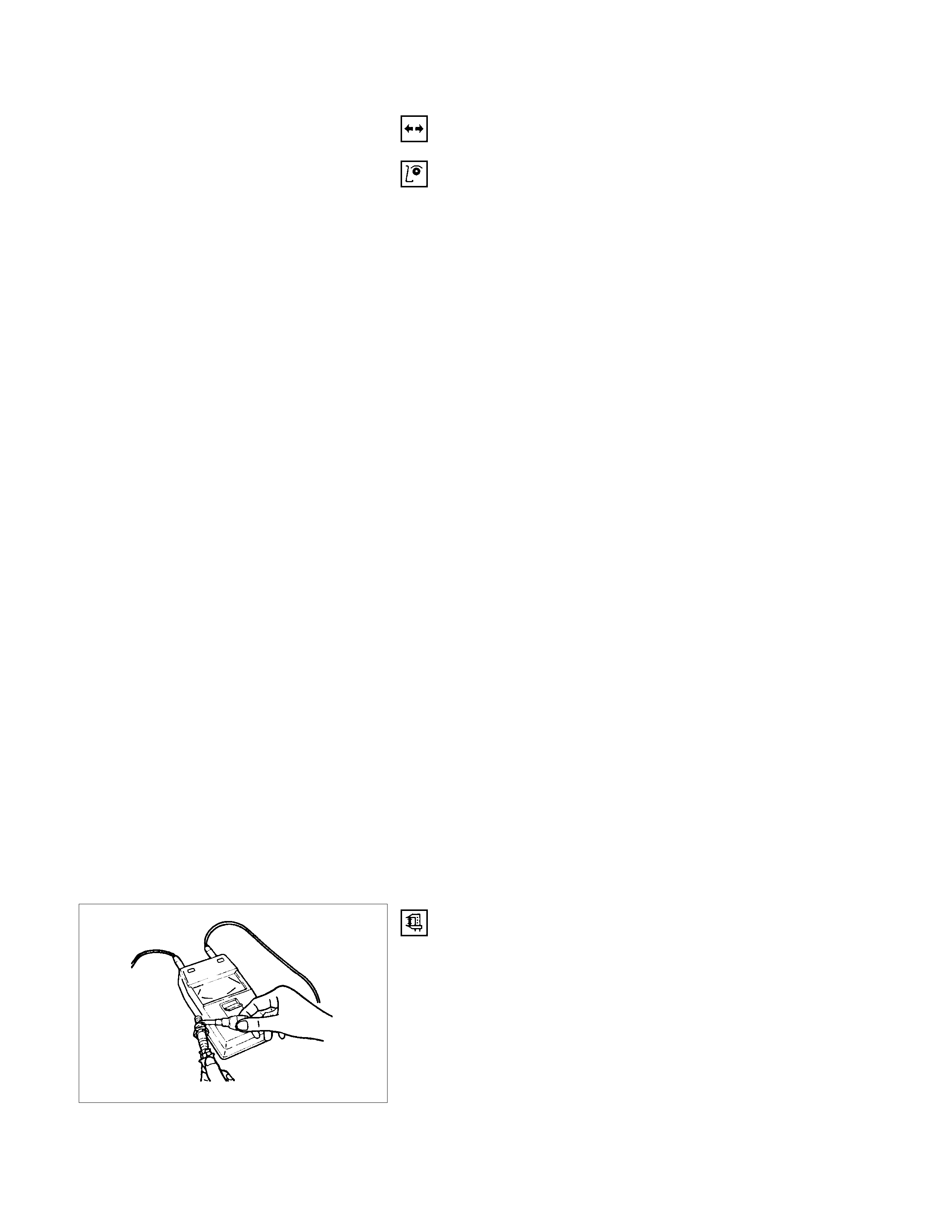
SPARK PLUG
REMOVAL
1. Remove spark plugs.
INSPECTION AND REPAIR
The spark plug affects entire engine performance and
therefore its inspection is very important.
•Check electrode and insulator for presence of cracks, and
replace if any.
•Check electrode for wear, and replace if necessary.
•Check gasket for damage, and replace if necessary.
•Measure insulation resistance with an ohmmeter, and
replace if faulty.
•Adjust spark plug gap to 1.0 - 1.1 mm (0.027 in) - 0.8 mm
(0.031 in).
•Check fuel and electrical systems if spark plug is extremely
dirty.
•Use spark plugs having low heat value (hot type plug) if f uel
and electrical systems are normal.
•Use spark plugs having high heat value (cold type plug) i
insulator and electrode are extremely burned.
SOOTY SPARK PLUGS
Much deposit of carbon or oil on the electrode and insulator of
spark plug reduces the engine performance.
Possible causes:
•Too rich mixture
•Presence of oil in combustion chamber
•Incorrectly adjusted spark plug gap
BURNING ELECTRODES
This fault is characterized by scorched or heavily oxidized
electrode or blistered insulator nose.
Possible causes:
•Too lean mixture
•Improper heat value
MEASURING INSULATION RESISTANCE
•Measure insulation resistance using a 500 volt megaohm
meter.
•Replace spark plugs if measured value is out of standard.
Insulation resistance: 50 MΩ
ΩΩ
Ω or more