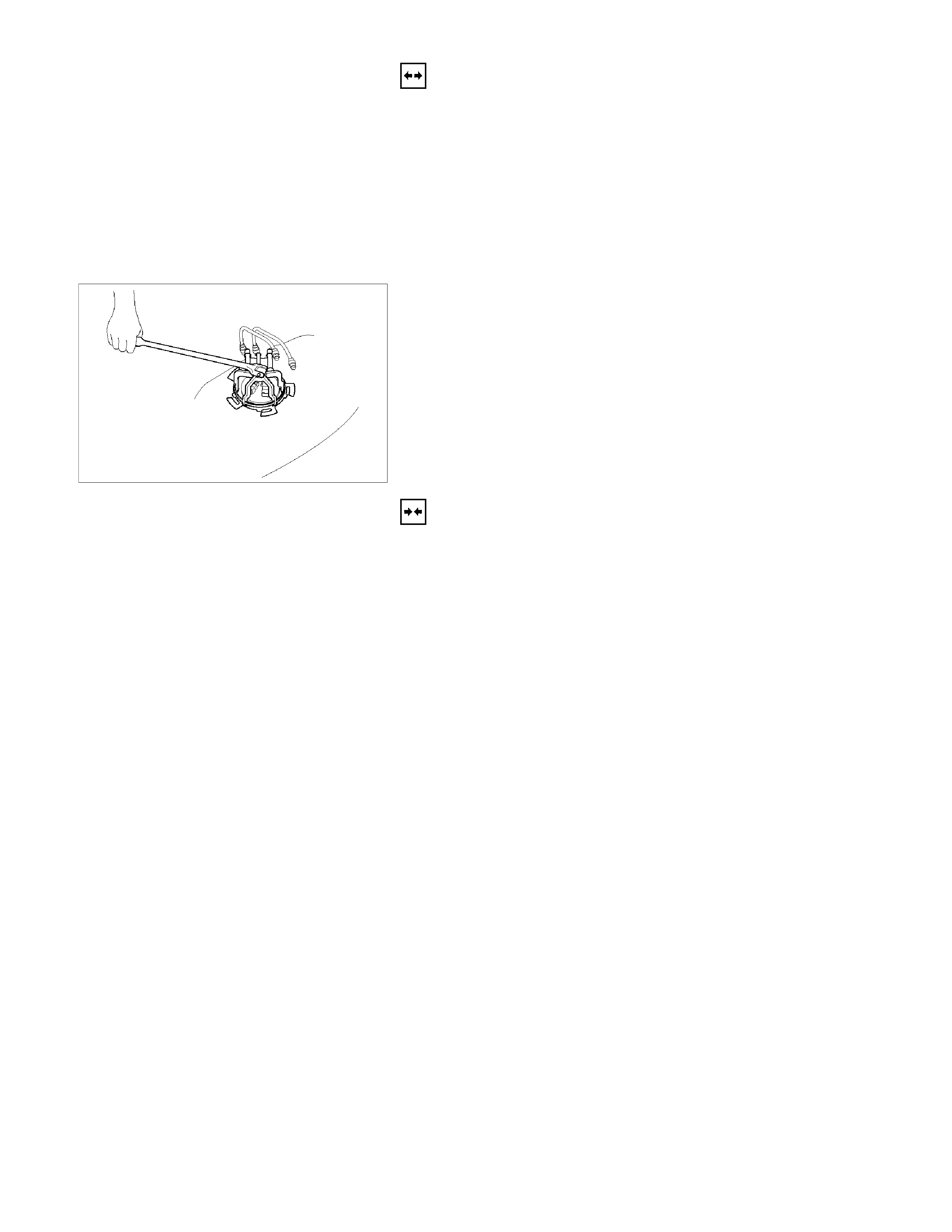
Removal
CAUTION: When repair to the fuel system has been
completed, start engine and check the fuel system for
loose connection or leakage. For the fuel system
diagnosis, see Section “Driveability and Emission".
1. Remove fuel tank assembly (10). Refer to “Fuel Tank
Removal" in this section.
2. Disconnect the quick connector of the fuel tube (6)
from fuel gauge unit.
3. Disconnect the quick connector of the evapo tube (7)
from fuel gauge unit.
140R100035
4. Remove the retainer ring (8) from the fuel tank with
the removal tool 5-8840-2602-0.
5. Slowly remove the fuel gauge unit (4) from the fuel
tank, being careful not to bend the float arm.
NOTE:
Cover opening for the fuel gauge unit on fuel tank to
prevent any foreign matter from entering.
6. Discard fuel gauge unit seal (9) because it is not
reusable.
Installation
1. Clean the seal surface of the fuel tank and the fuel
gauge unit.
NOTE:
If there is foreign matter on the seal surface, it may cause
a fuel leak.
2. Install the new fuel gauge unit seal (9) to opening of
the fuel tank, fitting the seal along the groove.
3. Install the fuel gauge unit (4) into the fuel tank, being
careful not to bend the float arm.
4. Ensure that the flange on the fuel gauge unit is fitted
into the groove in the opening of the fuel tank and
seated firmly on the fuel gauge unit seal.
5. Carefully lock the retainer ring (8) to the fuel tank with
the remover tool 5-8840-2602-0.
6. Connect the quick connector of the evapo tube (7) to
the fuel gauge unit.
7. Connect the quick connector of the fuel tube (6) to the
fuel gauge unit.
NOTE:
Refer to “Fuel Tube/Quick Connector Fittings” in this
section when performing any repairs.