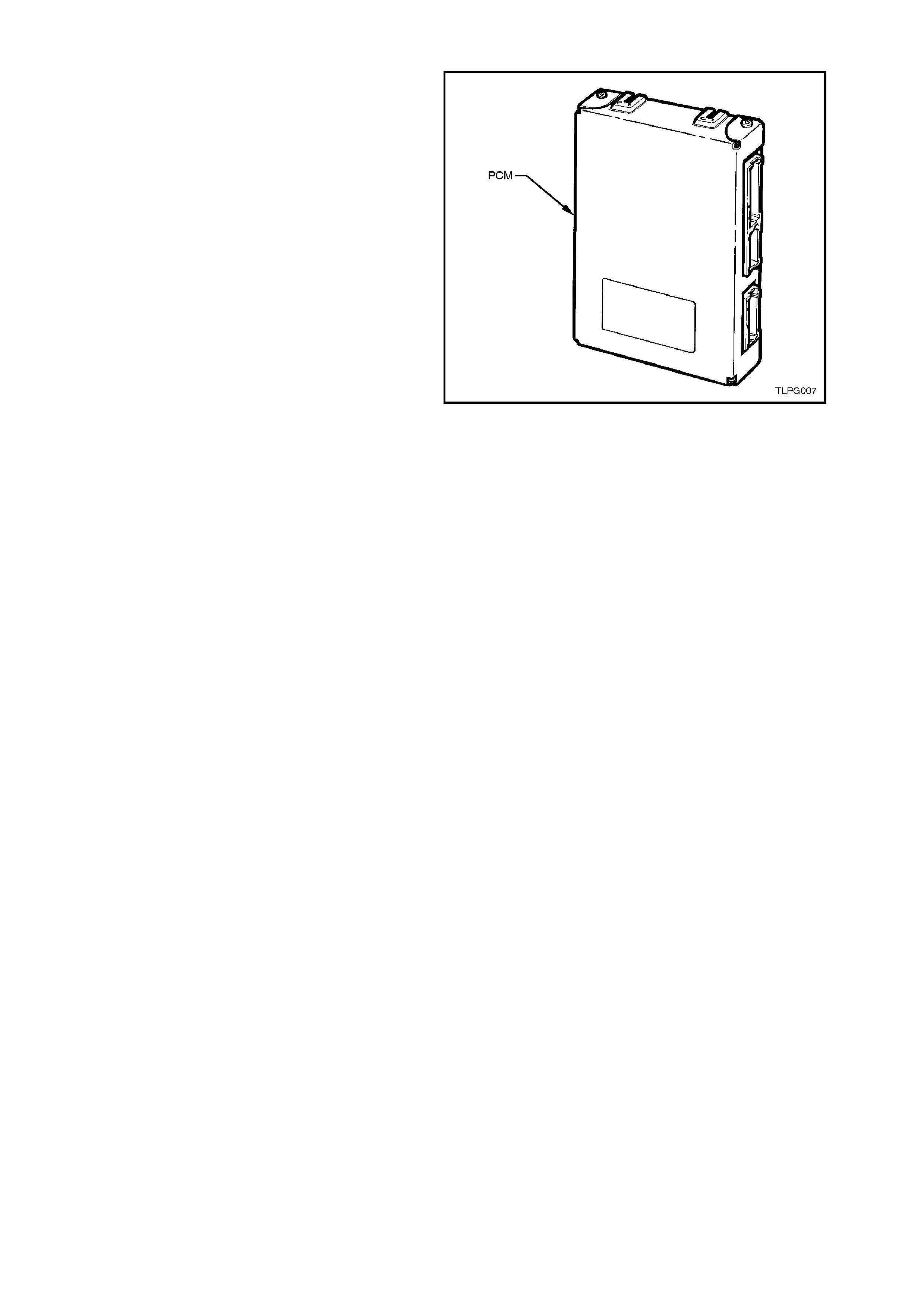
1.18 POWERTRAIN CONTROL MODULE
The Powertrain Control Module (PCM) when fitted
with the correct LPG PROM is c apable of operating
in either of two operating m odes, PETRO L or LPG.
The m ode that the PCM is operating in is stored in
the memory of the PCM so that the engine s tarts in
the same mode on the next ignition cycle.
PETROL MODE
When operating in the petrol mode, the LPG
system is turned off and the vehicle will operate on
petrol, with full engine management control in the
same manner as a vehicle that is not fitted with
LPG. In this mode, the instrument cluster fuel
gauge will show the amount of petrol in the petrol
fuel tank.
LPG MODE
When operating in the LPG mode, the engine
managem ent system is switched to the LPG mode,
and the LPG system is turned on, enabling the
vehicle to operate on LPG. When the PCM
switches to the LPG mode it energises the LPG
relay. The LPG relay supplies power to the ADP
and the smart unit via fuse F9.
In this mode the LPG lamp will be turned on and
the instrument cluster fuel gauge will show the
amount of LPG in the LPG cylinder.
The PCM controls the flow of LPG, by sending a
signal to the sm art unit via circuit 937 W /G wire on
receiving this signal the smart unit energises the
solenoid valve. The smart unit also energises the
LPG lockoff via circuit 965 BLU/O wire.
Figure 1-23
In the LPG m ode, the f ollowing c hanges have been
made so the engine can operate on LPG.
NOTE:
These changes only effect the operation of the
PCM when operating in LPG mode.
Injector Pulse Width
The injector pulse width is set to zero in all LPG
operating modes, except during engine cranking
or, on when the vehicle runs in “engine valve
recession protection mode”.
During engine cranking the amount of petrol
delivered is determined by the engine coolant
temperature and the engine crank time. The
injection of petrol during engine cranking is to aid
engine starting.
when operating in the LPG mode, and under
conditions of high speed / high load, a small
amount of petrol is injected into the engine to
protect the engine from engine valve seat
recession. When petrol is injected under these
conditions, it is refer red to as the engine valve seat
recession protection mode.