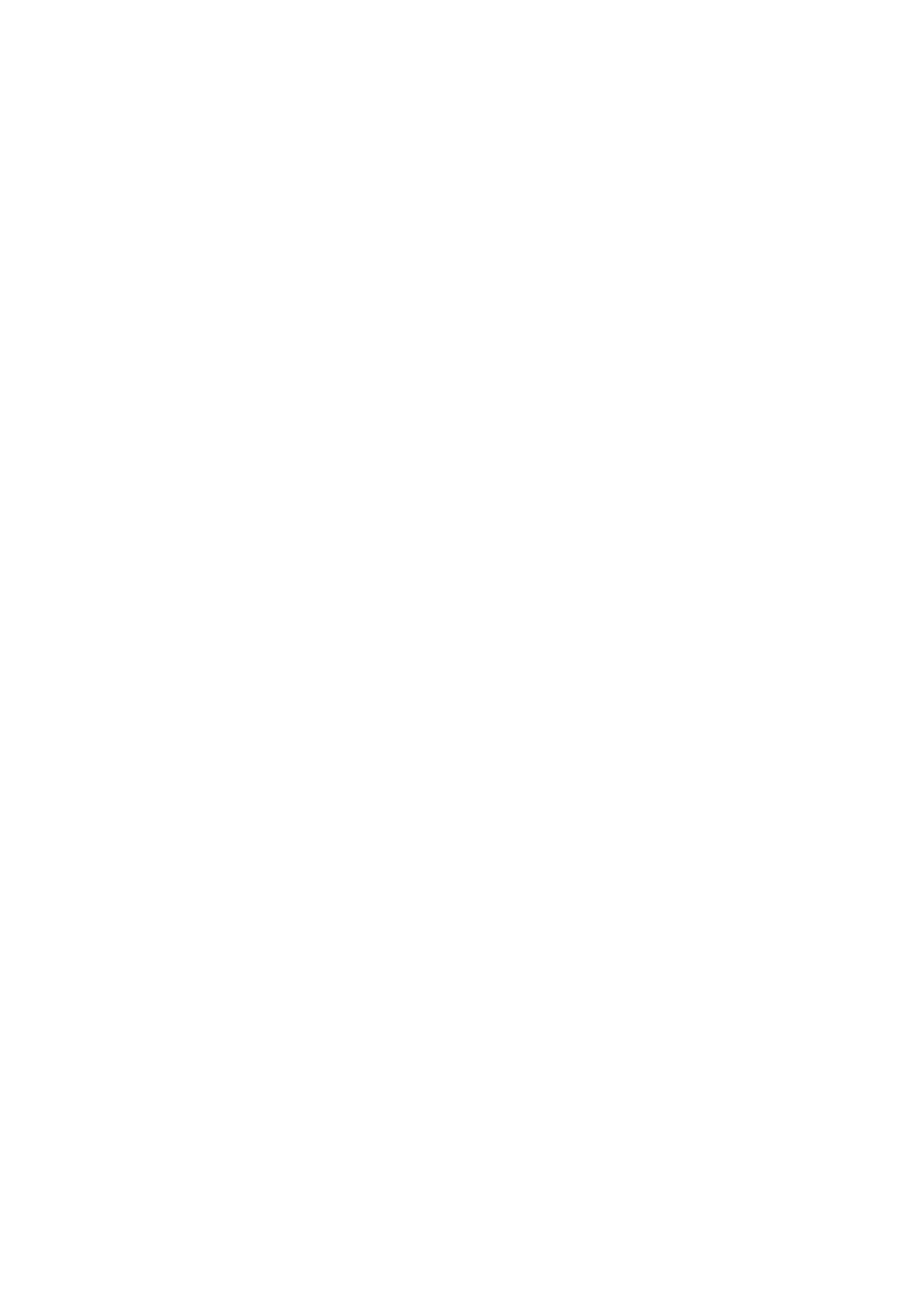
B4 - INTAKE AIR TEMPERATURE (IAT) INPUT SIGNAL
The PCM sends a 5 volt signal voltage to the IAT sensor, which is a temperature - variable-resistor called a
thermistor. The sensor is also connected to earth, and will alter the signal voltage according to incoming air
temperature. As the air temperature increases, the voltage seen on this terminal decreases. At 0 degrees C, the
voltage will be above 4 volts. At normal operating temperature (10 degrees C to 80 degrees C) the voltage will be
less than 4 volts.
B5 - ENGINE COOLANT TEMPERATURE (ECT)INPUT SIGNAL
The PCM sends a 5 volt signal voltage out to the engine coolant temperature sensor, which is a temperature-
variable-resistor called thermistor. The sensor, being also connected to earth, will alter the voltage according to
engine coolant temperature. As the engine coolant temperature increases, the voltage seen on terminal B5
decreases. At 0 degrees C engine coolant temperature the voltage will be above 4 volts. At normal operating
temperature (85 degrees C to 100 degrees C) the voltage will be less than 2 volts.
B6 - TRANSMISSION FLUID TEMPERATURE (TFT) INPUT SIGNAL
- AUTO TRANS ONLY
The PCM sends a 5 volt signal voltage out to the transmission fluid temperature sensor, which is a temperature-
variable-resistor called thermistor. The sensor, being also connected to earth, will alter the voltage according to
transmission fluid temperature. As the fluid temperature increases, the voltage seen on terminal B6 will decrease.
B7 - EGR/A/C PRESSURE SENSOR REFERENCE VOLTAGE
This voltage should always be 5 volts anytime the ignition is "ON." It is a regulated voltage output from the PCM,
and supplies 5 volts to the A/C Pressure Transducer and EGR valve.
B8 - BATTERY VOLTAGE FEED
- HOT AT ALL TIMES -
This supplies the PCM with full-time +12 volts. It stays hot even when the ignition is turned off. It receives its voltage
through the "ENGINE" fuse F25. This PCM terminal could be called the power supply and "MEMORY" terminal.
B9 - NOT USED
B10 - LINEAR EGR VALVE PINTLE POSITION
This voltage is a indication to the PCM the position of the EGR valve pintle position. A low voltage indicates a fully
extended pintle (closed valve). A voltage near 5 volts indicates a retracted pintle (open valve).
B11 - THROTTLE POSITION (TP) SENSOR
The TP sensor input voltage, which follows actual throttle changes, is variable from 0 to 5 volts. Typically the voltage
is less than 1 volt at idle, and 4 to 5 volts at wide-open throttle.
B12 - INJECTOR CIRCUIT VOLTAGE MONITOR INPUT SIGNAL
The injector voltage monitor line is used so that the PCM will know the exact voltage the fuel injectors are operating
at. This voltage signal is used to modify the fuel injector pulse width calculation.
C - D TERMINAL CONNECTOR
C1 - TORQUE CONVERTER CLUTCH ENABLE SOLENOID CONTROL
- AUTO TRANS ONLY
The PCM is used to either open or provide a path to earth for the torque converter solenoid. When the PCM
provides a path to earth, the TCC solenoid is considered ON and voltage should be near 0 volts. The PCM uses
both the TCC enable solenoid and the TCC "PWM" solenoid to control the torque converter clutch. (See TCC PWM
solenoid terminal E1)
C2 - 1 - 2 SHIFT SOLENOID CONTROL
- AUTO TRANS ONLY -
The PCM is used to either open or provide a path to earth for the 1-2 shift solenoid. When the PCM provides a path
to earth, the 1-2 shift solenoid is considered "ON" and the voltage should read 0 volts.
C3 - 2 - 3 SHIFT SOLENOID CONTROL
- AUTO TRANS ONLY
The PCM is used to either open or provide a path to earth for the 2-3 shift solenoid. When the PCM provides a path
to earth, the 2-3 shift solenoid is considered "ON" and the voltage should read 0 volts.
C4 - CANISTER PURGE SOLENOID CONTROL
The PCM operates a normally closed solenoid valve, which controls vacuum to purge the evaporative emissions
storage canister of stored gasoline vapours. The PCM turns "ON" the pulse width modulated control of the purge
solenoid, to control purging of the stored vapours. If the PCM is not energising the purge solenoid, the voltage
measured at this terminal should equal battery voltage. If the PCM is controlling the solenoid, the measured voltage
will be between battery voltage and 0.50 volts.