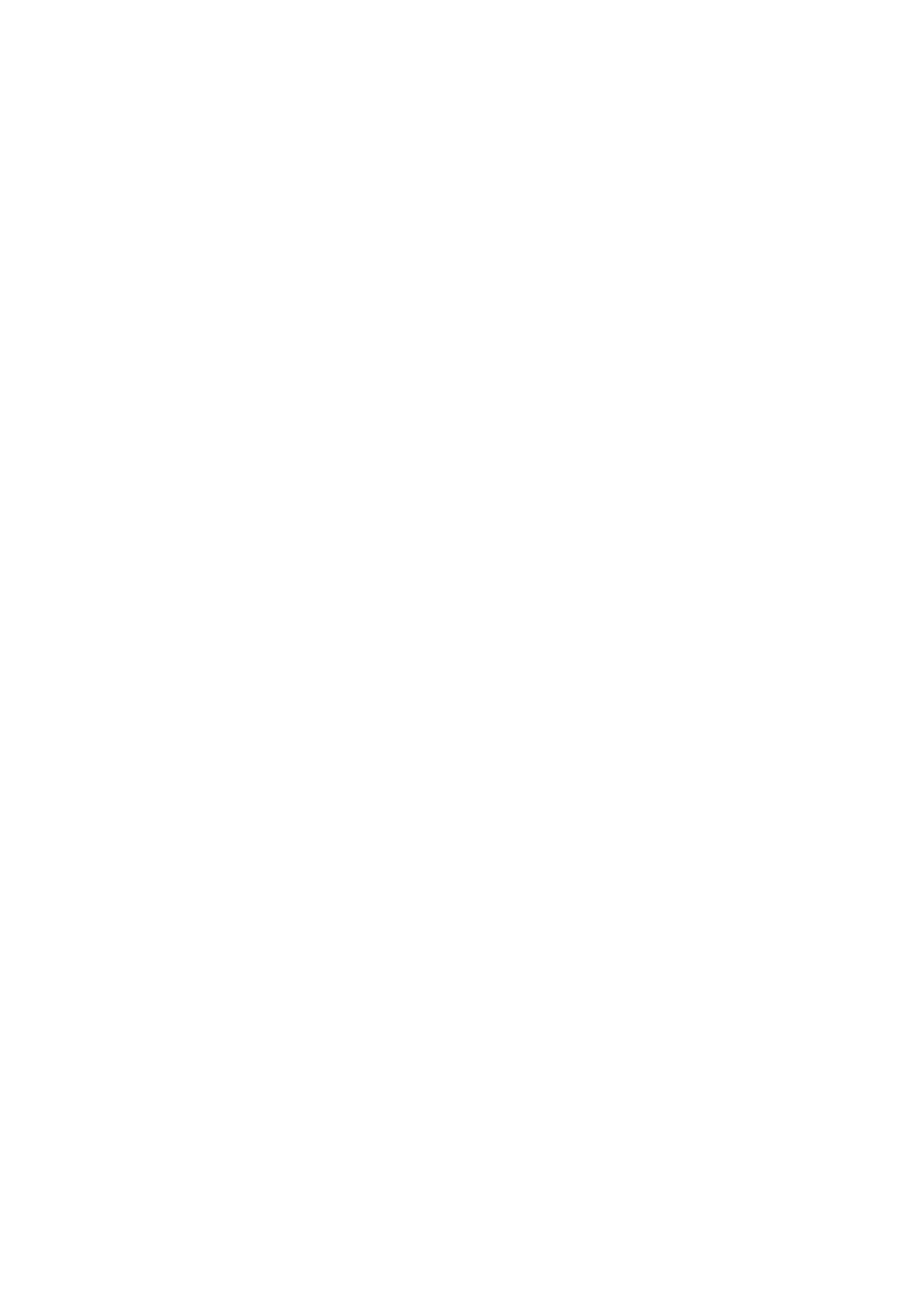
12. TORQUE WRENCH SPECIFICATIONS
Nm
Lower steering column shroud screw................................... 0.5 - 2
Instrument panel end cap cover attaching screws ............... 1 - 3
Instrument panel compartment attaching screws................. 1 - 3
Instrument panel compartment lock striker attaching screws 1 - 3
Centre console securing screws........................................... 1 - 3
Centre console bin retaining nuts......................................... 1 - 3
Transmission console retaining screws................................ 1 - 3
Centre console storage compartment securing screws ....... 1 - 3
Demist nozzle retaining screws............................................ 1 - 3
Front dash speaker retaining screws.................................... 1 - 2
Instrument panel carrier end panel attachment screws........ 1 - 3
Instrument facia assembly retaining screws......................... 1 - 3
Centre facia assembly securing screws............................... 1 - 3
Heater and air conditioning controls securing screws.......... 1 - 3
Combined instruments assembly securing screws .............. 1 - 3
Instrument panel carrier retaining screws............................. 7 - 12
Instrument panel lower trim right side rail assembly
retaining screws.................................................................... 1 - 3
Centre facia side extension support rail attaching screws.... 1 - 3
Support steering column bracket inner securing screws...... 3 - 5
Passenger air bag support rail securing screws................... 2.5 - 5
Lower left side rail connecting screws.................................. 1 - 3
Instrument panel carrier rail assembly securing screws....... 1 - 3
Passenger side air bag securing nuts .................................. 15 - 25
TXV attaching cap screws.................................................... 4 - 4.5
Heating, ventilation and air conditioning unit attachment
screws to the passenger compartment ................................ 6 - 14
Heating, ventilation and air conditioning unit attachment
screws to the engine bay...................................................... 2 - 5
Evaporator tube plate securing screws ................................ 4.0 - 4.5
Washer faced tube plate retaining bolt................................. 7.5 - 12.5
TXV Pipe bracket retaining bolt........................................... 7.5 - 12.5
Compressor suction and discharge hose retaining nut ........ 7.5 - 12.5
FDR pipe flange nut.............................................................. 7.5 - 12.5
Condensor discharge pad retaining nut................................ 7.5 - 12.5
Condensor inlet pad fitting nut.............................................. 7.5 - 12.5
Compressor retaining bolts (V8)........................................... 40 - 60
A/C idler pulley retaining nut (V8)......................................... 40 - 60
A/C hose pad fitting retaining nut (V8).................................. 26 - 42
Idler pulley mounting bracket retaining nut (V6)................... 20 - 30
Idler pulley retaining bolt....................................................... 40 - 50