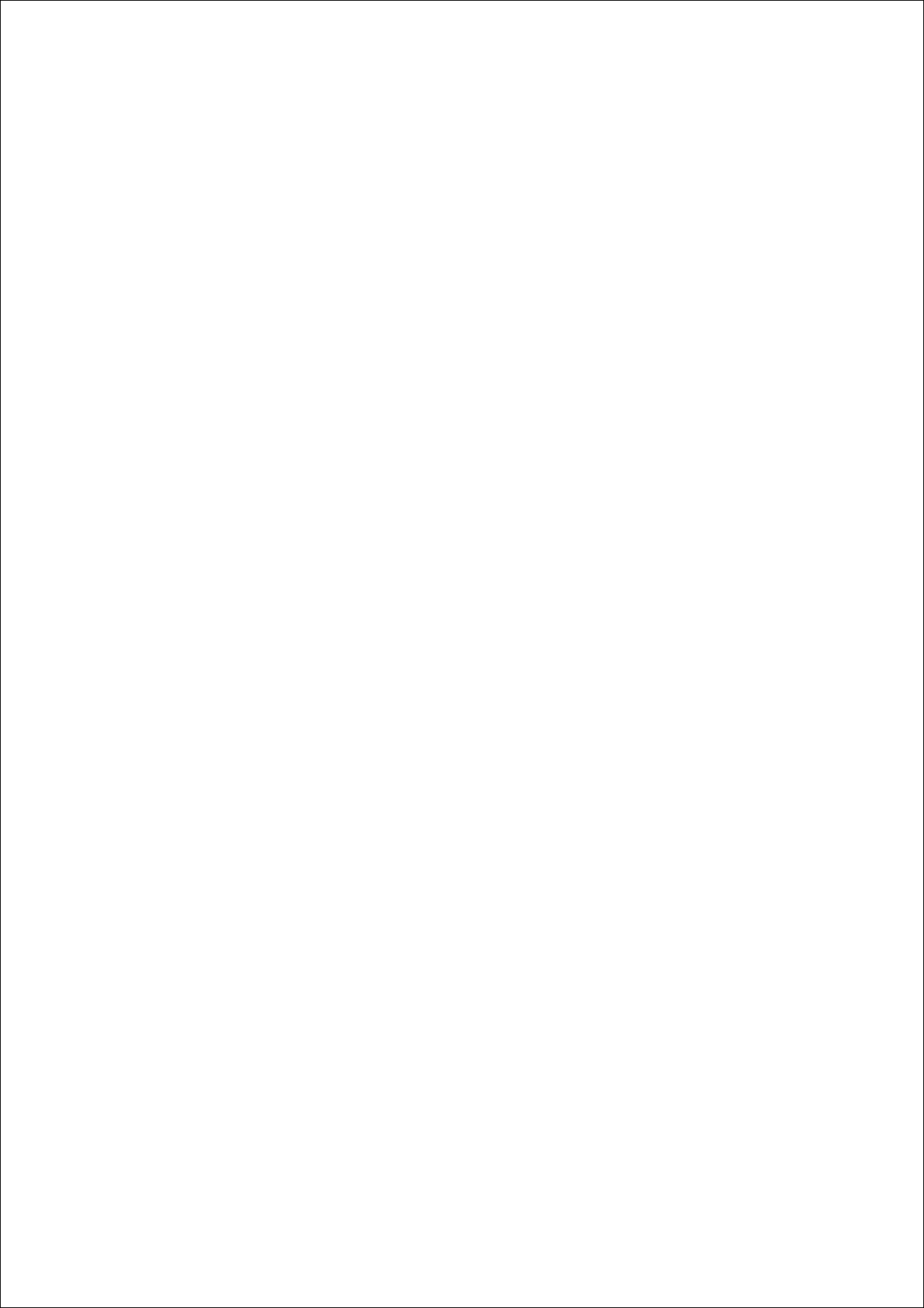
CHART A - DIAGNOSTIC CIRCUIT CHECK
CIRCUIT DESCRIPTION
When investigating any complaint of an ECC
problem or malfunction, always begin diagnosis
with the following diagnostic circuit check. This
check is a preliminary procedure that checks to
ensure the ECC is communicating on the serial
data line as well as helping to identify a problem or
malfunction and directing the reader to the
appropriate diagnostic chart in this Section.
With TECH 2 connected to the DLC and the
ignition switched on, TECH 2 should display serial
data communication. If TECH 2 does not display
serial data, the serial data circuit maybe open of
shorted.
There are several other control modules that are
connected to the serial data line (PCM, BCM,
ABS/ASR, ECC, instruments and SDM). Any one
of these control m odules c ould cause a f ault on the
serial data line. This fault could result in TECH 2
not being able to display serial data.
Test Description:
The numbers below refer to step numbers in
diagnostic chart ‘A’
1. This test checks if the ECC control module is
being powered up.
2. This test checks if the ECC control module has
detected and stored a current Diagnostic
Trouble Code.
3. This test determines if TECH is being powered
up.
4. This test checks if tech can communicate with
the ECC control module. If tech 2 cannot
communicate with the ECC control module, you
will not be able to determine which DTC has
been stored in the control module’s memory.
5. Determines which DTC has been stored in the
control module’s memory.
6. This test determines if a DTC was current and
has rectified. An intermittent problem has
caused this DTC to be stored.
7. During this test the ECC control module re-
calibrates the air mix doors, an incorrectly
calibrated air mix door will cause incorrect
operation of the ECC system.
8. Checks accuracy of ECC sensors.
9. During this test the operation of the air
conditioning section of the ECC system is
checked.
Notes on Diagnostic Chart:
1. Refer to 1.1 TECH 2 DIAGNOSTICS in this
Section for connecting and using TECH 2.
2. Refer to 1.2 TECH 2 TEST MODES AND
DISPLAYS FOR ECC DIAGNOSIS in this
Section for further information on programming
of the ECC.
3. ECC sensors can be checked using the
following procedure and should als o be check ed
in the order as listed:
In car temperature sensor - connect TECH 2 to
DLC, select Body / Electronic Climate Control /
Data Display / Data List and scroll to In Car
Temperature Sensor. Using a digital