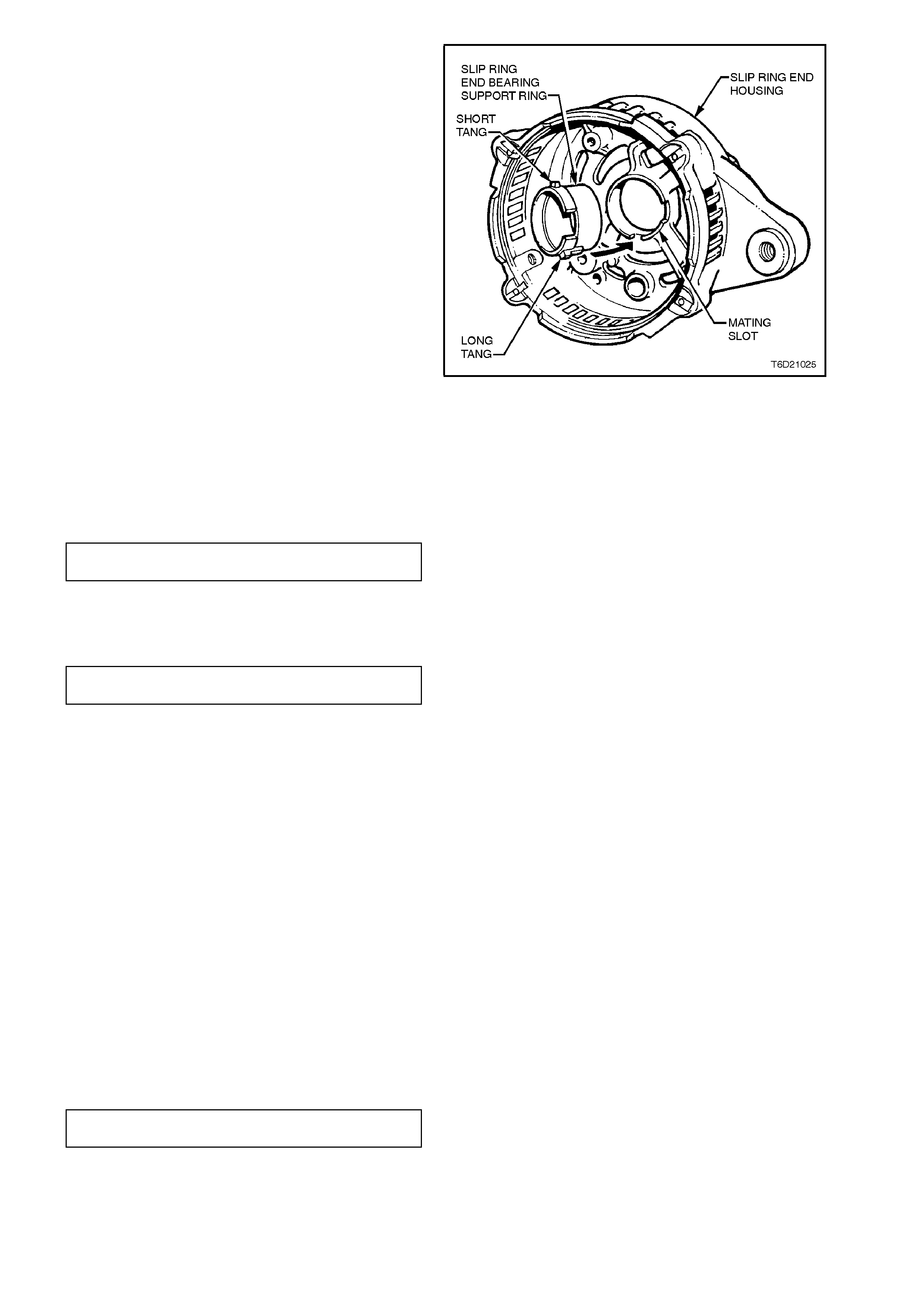
8. Inspect the slip ring end bearing support ring
for signs of damage, especially cracks. If in
any doubt replace the ring by pressing it into
the slip ring end housing by hand. DO NOT
USE EXCESSIVE FORCE.
IMPORTANT:
The slip ring end bearing support ring will only
locate correc tly into the slip ring end housing in one
location, i.e. with the long tang on its outer diam eter
locating into the mating slot in the slip ring end
housing.
9. Apply heat sink compound to both sides of
new rectifier positive heat sink mica washers.
Assemble mica washers to positive heat sink
with washer having largest hole fitted over the
B+ terminal bolt. The other mica washer is
fitted on the positive heat sink , ar ound the hole
for the retaining screw.
10. Install spacer over B+ terminal bolt and
assemble rectifier into slip ring end housing.
Assemble ins ulating washer, f lat washer , wave
washer and nut to B+ terminal, leaving nut
finger tight.
Figure 6D2-1-28
11. Install and tighten rectifier retaining screws to
the correct torque specification.
RECTIFIER RETAINING SCREW
TORQUE SPECIFICATION 2.2 - 3.2 Nm
Tighten B+ terminal nut to the correct torque
specification.
B+ TERMINAL NUT
TORQUE SPECIFICATION 7.5 - 8.5 Nm
12. To refit the stator, ensure that the mating
surfaces of the stator frame, drive end and slip
ring end housings are clean and free from
damage.
Fit the stator into the slip ring end housing,
noting the correct lead positioning. Fit the
stator leads into the wire loops in the rectifier.
Using a pair of pointed nose pliers, squeeze
the loops to retain the stator leads prior to
soldering. Solder the leads into position using
60/60 resin cored solder.
Once completed, ensure the leads will clear
the internal fan when the rotor is assembled
into the stator.
13. Assem ble rotor and dr ive end housing into the
stator and slip ring end plate assembly,
aligning marks made during disassembly.
14. Reinstall through bolts and tighten evenly, and
to the correct torque specification.
THROUGH BOLT
TORQUE SPECIFICATION 3.8 - 5.5 Nm