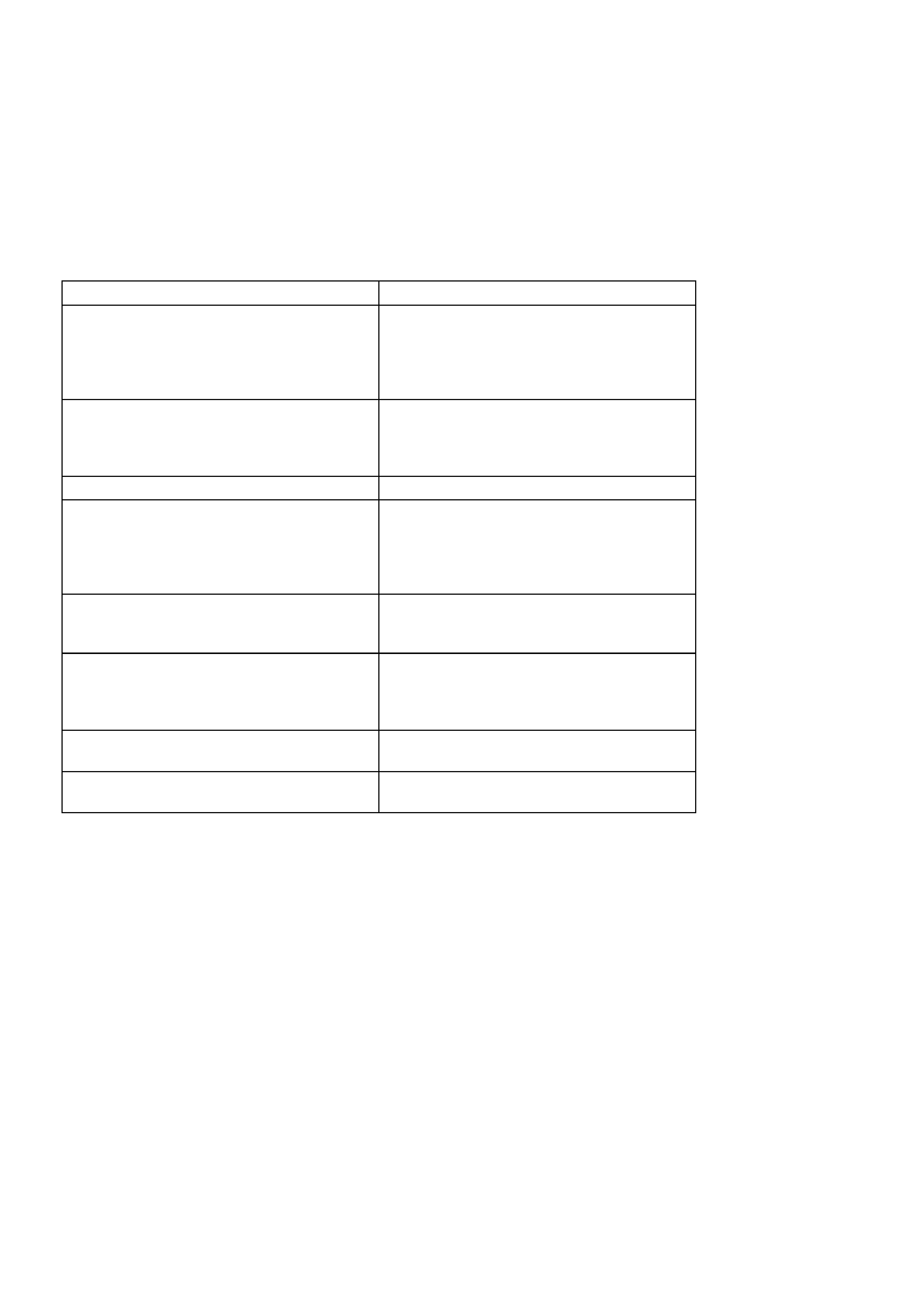
3. DIAGNOSIS
Many starting problems can be categorised within the following classifications:
1. The starter motor will not crank the engine.
2. The engine will crank at normal speed, but will not start.
3. The starter cranks the engine very slowly.
If the engine is cranked over by the starter motor at the normal speed, but will not start, the problem is in the ignition
system, fuel system or engine, rather than a fault in the starting system.
Before removing the starter motor, when investigating a starting problem, follow the procedures outlined in the
accompanying diagnostic charts.
SYMPTOM PROBABLE FAULT
A. Speed, torque and current low. A. High resistance in motor. Check field to
terminal connection, condition of
brushes and their connections and
check for dirty brushes or burnt
commutator.
B. Speed and torque low, current high. B. Tight or worn bearings, bent armature
shaft, insufficient end play, armature
fouling pole shoe, short-circuited
armature, earthed armature or field coil.
C. Speed and current high, torque low. C. Short circuited windings in field coil.
D. Armature does not rotate. No current. D. Open circuited armature, field coils or
solenoid. If commutator is badly burned,
there may be poor contact between
brushes and commutator, owing to
excessively worn or sticking brushes.
E. Armature does not rotate. High current. E. Earthed field winding or open-circuited
solenoid. Armature physically prevented
from rotating.
F. Excessive brush movement causing
arcing at commutator. F. Low brush spring tension, worn or out-
of-round commutator, 'thrown' or high
segment on commutator, or insulation
protruding between segments.
G. Excessive arcing at commutator. G. Defective armature windings, sticking
brushes or dirty commutator.
H. Armature rotates but pinion does not
mesh with ring gear. H. Pinion bearing fouled, burred, damaged
ring gear or broken pinion teeth.