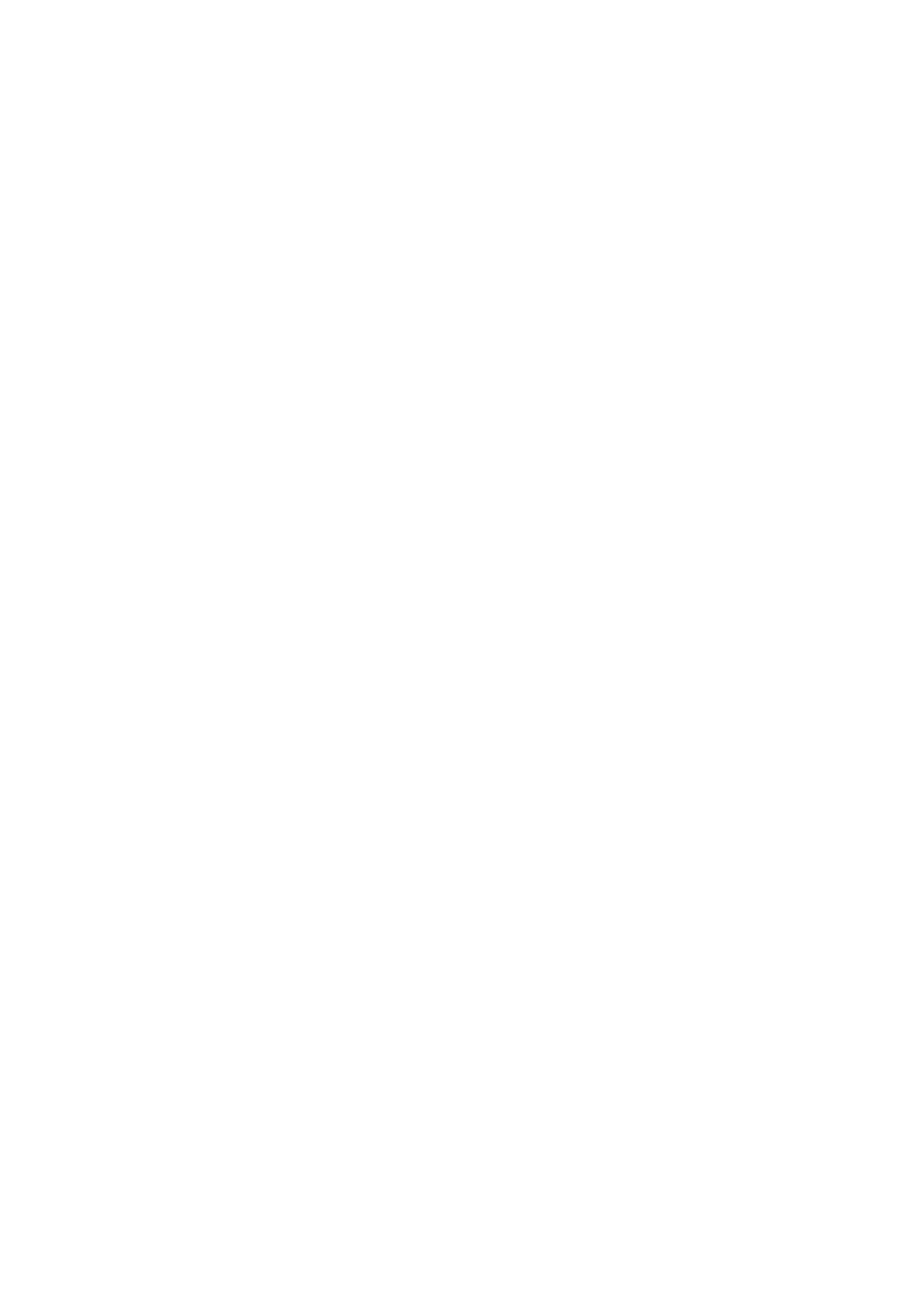
NORMAL OPERATION
Refer to Fig. 6D2-3-34
Brown or greyish-tan deposits and slight electrode wear indicate correct spark plug heat range and mixed periods of
high and low speed driving.
CARBON FOULED (SOOTED)
Refer to Fig. 6D2-3-34
Dry, fluffy black carbon (soot) deposits due to poor ignition output, weak coil or faulty spark plug leads.
Excessive idling, slow speeds under light load also can keep spark plug temperatures so low that normal
combustion deposits are not burned off.
OIL FOULED
Refer to Fig. 6D2-3-34
Wet, oily deposits with minor electrode wear may be caused by oil leaking past worn piston rings. 'Break in' of a new
or recently overhauled engine before rings are fully seated may also result in this condition.
DEPOSIT FOULING "A"
Refer to Fig. 6D2-3-34
Red brown, yellow and white coloured coatings on the insulator tip. These coatings are by-products of combustion
and come from the fuel and lubricating oil, both of which today generally contain additives. Most powdery deposits
have no adverse effect on spark plug operation; however, they may cause intermittent missing under severe
operating conditions, especially at high speeds and heavy load.
DEPOSIT FOULING "B"
Refer to Fig. 6D2-3-34
Deposits are similar to those identified as DEPOSIT FOULING "A". These deposits are by-products of combustion
and come from the fuel and lubricating oil. Excessive valve stem clearances and/or defective intake valve seals will
allow excessive oil to enter the combustion chamber. The deposits will accumulate on the portion of the spark plug
projecting into the chamber and will be heaviest on the side facing the intake valve. Defective seals should be
suspected when the condition is found in only one or two cylinders
DEPOSIT FOULING "C"
Refer to Fig. 6D2-3-34
Most powdery deposits identified in DEPOSIT FOULING "A", have no adverse effect on the operation of the spark
plug as long as they remain in the powdery state. However, under certain conditions of operation, these deposits
melt and form a shiny glaze coating on the insulator which, when hot, acts as a good electrical conductor. This
allows the current to follow the deposits instead of jumping the gap, thus shorting out the spark plug.
DETONATION
Refer to Fig. 6D2-3-34
Commonly referred to as engine knock or 'ping', detonation causes severe shock inside the combustion chamber to
the adjacent parts which include spark plugs.
PRE-IGNITION
Refer to Fig. 6D2-3-34
Causes burned or blistered insulator tip and badly eroded electrodes. Excessive overheating is indicated. Cooling
system blockage or sticking valves are common causes of pre-ignition. Spark plugs which are the wrong (too hot)
heat range, or not properly installed are also a possible cause. Sustained high speed, heavy load service can
produce high temperatures which will cause pre-ignition.
HEAT SHOCK FAILURE
Refer to Fig. 6D2-3-34
A common cause of broken and cracked insulator tips. Rapid increase in tip temperature under severe operating
conditions causes the heat shock and a fracture results. Another common cause of chipped or broken insulator tips
is carelessness in re-gapping, by either bending the centre electrode to adjust the gap, or allowing the gapping tool
to exert force against the tip of the centre electrode or insulator when bending the outer electrode to adjust the gap.
INSUFFICIENT INSTALLATION TORQUE
Refer to Fig. 6D2-3-34
Poor contact between the spark plug and the engine seat. The lack of proper heat transfer, resulting from poor seat
contact, causes overheating of the spark plug and, in many cases, severe damage as shown. Dirty threads in the
cylinder head can also result in the plug seizing before it is seated.
THREAD SEIZURE
Refer to Fig. 6D2-3-34
Recommended installation torque may be obtained without taper seat engagement in cylinder head. Operation of an
engine with this type of installation may result in spark plug overheating, causing possible damage to the spark plug
or engine. Always ensure cylinder head and spark plug threads are free of deposits, burrs and scale.