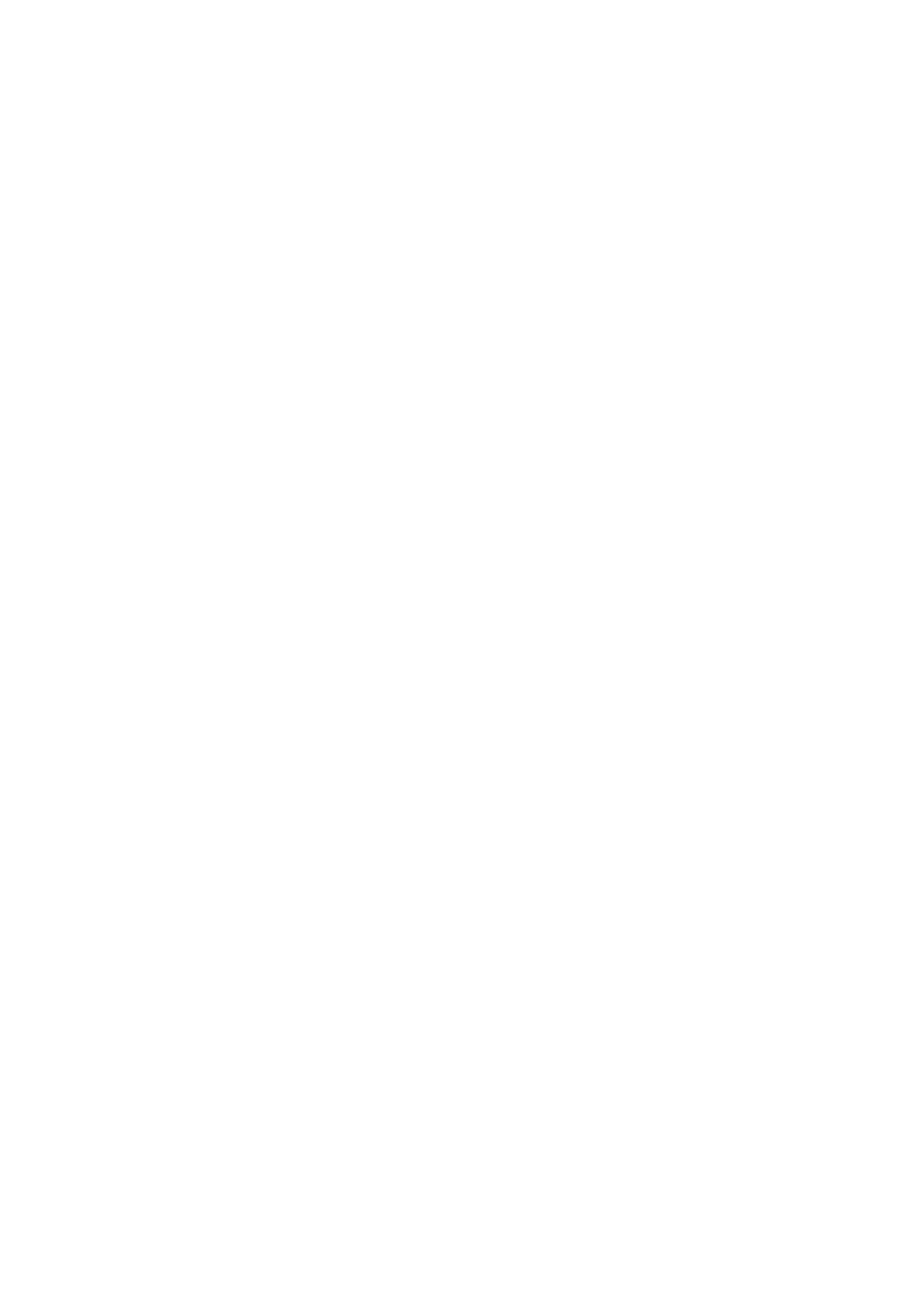
1.2 POWER FLOWS
The maindrive gear, fifth, third, second, first speed and reverse gears are in constant mesh with the cluster gear.
Therefore, when the engine is running with the clutch engaged, torque is imparted to the maindrive gear and
through the cluster gear to the fifth, third, second, first speed and reverse gears at all times.
Refer to Figure 7B1-6 for illustrations relating to the following descriptions:
NEUTRAL
In neutral, with the clutch engaged, the maindrive gear turns the cluster gear. The cluster gear turns the constant
mesh gears because no synchroniser assemblies are engaged. As all constant mesh gears are supported on roller
bearings, they will also rotate with the cluster gear.
FIRST GEAR
In first gear, the first/second speed synchroniser sleeve is moved rearward to engage the first speed gear, which is
being turned by the cluster gear. Because the first/second speed synchroniser hub is splined to the mainshaft,
torque is imparted to the mainshaft from the first speed gear through the sy nchroniser sleeve and hub.
SECOND GEAR
In second gear, the first/second speed synchroniser sleeve is moved forward to engage the second speed gear,
which is being turned by the cluster gear. Because the first/second speed synchroniser hub is splined to the
mainshaft, torque is imparted to the mainshaft from the second speed gear through the synchroniser sleeve and
hub.
THIRD GEAR
In third gear, the first/second speed synchroniser sleeve assumes a neutral position. The third/fourth speed
synchroniser sleeve is moved rearward to engage the third speed gear, which is being turned by the cluster gear.
The engagement of the sleeve with the third speed gear, imparts torque to the mainshaft because the third/fourth
speed synchroniser hub is splined to the mainshaft.
FOURTH GEAR
In fourth gear, the third/fourth speed synchroniser sleeve is moved forward to engage the maindrive gear. This
engagement of the maindrive gear with the third/fourth synchroniser sleeve and hub assembly, imparts torque
directly to the mainshaft. While the cluster gear is still rotating, it does not impart torque to any component but
continues to lubricate the internal transmission components by the ‘splash’ method.
FIFTH GEAR
In fifth or overdrive gear, the first/second and third/fourth speed synchroniser sleeves assume neutral positions. The
fifth speed/reverse synchroniser sleeve is moved rearward to engage the fifth speed constant mesh gear, supported
on the mainshaft by a caged needle roller bearing. This engagement of the sleeve with the fifth speed constant
mesh gear, imparts torque from the cluster gear to the mainshaft, via the splined synchromesh hub.
REVERSE GEAR
In reverse gear, the fifth speed/reverse synchroniser sleeve is moved forward to engage the mainshaft reverse gear
and the cluster reverse gear, via the reverse idler gear. This imparts torque from the cluster reverse gear through
the idler gear (reversing direction of rotation) to the mainshaft reverse gear. Because the fifth speed/reverse
synchromesh hub is splined to the mainshaft, this causes the mainshaft to rotate in the opposite direction to the
maindrive gear.