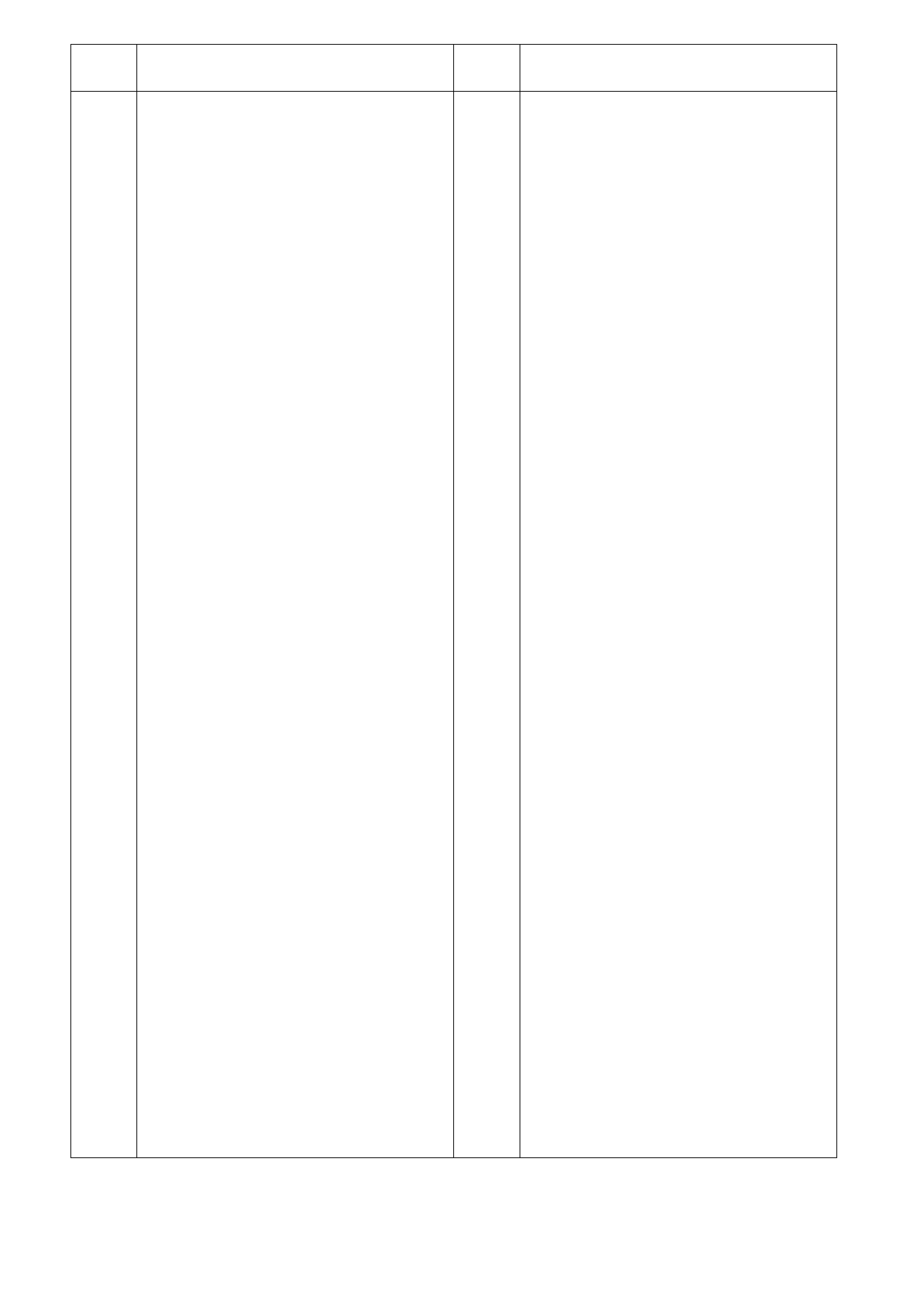
REF
No. PART NAME REF
No. PART NAME
7
600.
601.
602.
603.
605.
606.
607.
608.
609.
610.
611.
612A.
612B.
613.
614.
615.
616.
617.
618.
619.
620.
621.
622.
623.
625.
626.
627.
628.
630.
632.
633.
634.
635.
636.
637.
638.
639.
641.
642.
643.
644.
645a.
645b.
646.
648.
649a.
649b.
Bush, case
Spring assembly, 3-4 clutch boost - 5 places
Washer, thrust
Band assembly
Bush, reverse input clutch (front)
Housing & drum assembly, reverse input clutch
Bush, reverse input clutch (rear)
Piston assembly, reverse input clutch
Seals, reverse input clutch, inner and outer
Spring assembly, reverse input clutch
Ring, reverse input clutch, spring retainer
Plate, reverse input clutch, Belleville
Plate, reverse input clutch, turbulator, steel
Plate, reverse input clutch, composition
Plate, reverse input clutch, selective
Ring, reverse input clutch, retaining
Bearing assembly, stator shaft
Washer, thrust selective
Retainer and check ball assembly,
Seal, O-ring, turbine shaft
Ring, oil seal (solid)
Retainer and check ball assembly
Housing and shaft assembly, input
Seal, O-ring, input to forward clutch housing
Piston, 3rd and 4th clutch
Ring, 3rd and 4th clutch (apply)
Spring assembly, 3rd and 4th clutch
Retainer and ball assy, forward clutch housing
Housing, forward clutch
Piston, forward clutch
Piston, overrun clutch
Ball, overrun clutch
Spring assembly, overrun clutch
Snap ring, overrun clutch spring retainer
Seal, input housing to output shaft
Bearing assembly, input sun gear
Snap ring, overrun clutch hub retaining
Hub, overrun clutch
Retainer and race assembly, sprag
Forward sprag assembly
Retainer rings, sprag assembly
Race, forward clutch (outer)
Plate assembly, overrun clutch (steel)
Plate assembly, overrun clutch (composition)
Plate, forward clutch (apply)
Plate, forward clutch (waved)
Plate assembly, forward clutch (steel)
Plate assembly, forward clutch (composition)
650.
651.
653.
654a.
654b.
655.
656.
657.
658.
659.
661.
662.
663.
664.
665.
666.
667.
668.
669.
670.
671.
672.
673.
674.
675.
676.
677.
678.
679.
680.
681.
682A.
682B.
682C.
682D.
683.
684.
685.
686.
687.
692.
693.
694.
695.
696.
698.
699.
Plate, forward clutch backing (selective)
Ring, forward clutch backing plate retainer
Plate, 3rd and 4th clutch apply (stepped)
Plate assy, 3rd and 4th clutch (composition)
Plate assy, 3rd and 4th clutch (steel)
Plate, 3rd and 4th clutch backing (selective)
Ring, 3rd and 4th clutch backing plate retainer
Plug, orifice cup
Gear, input sun
Bush, input sun gear (rear)
Retainer, output shaft to input carrier
Carrier assembly, input
Bearing assembly, thrust
Gear, input internal
Bush, reaction carrier shaft (front)
Shaft, reaction carrier
Bush, reaction carrier shaft (rear)
Retainer ring, reaction shaft/internal gear
Washer, thrust
Shell, reaction sun
Retainer ring, reaction sun gear
Bush, reaction sun
Gear, reaction sun
Washer, thrust
Race, low and reverse roller clutch
Retainer ring, low and reverse support to case
Retainer ring, low and reverse roller assembly
Clutch assembly, low and reverse roller
Support assembly, low and reverse clutch
Spring, low and reverse clutch support retainer
Carrier assembly, reaction
Plate, low and reverse clutch (waved)
Plate, low and reverse clutch (selective)
Plate, low and reverse clutch (composition)
Plate, low and reverse clutch, turbulator (steel)
Bearing assembly, thrust
Gear, internal reaction
Support, internal reaction gear
Retainer ring, reaction gear/support
Shaft, output
Bearing, reaction gear support to case
Retainer ring, low and reverse clutch
Spring assembly, low and reverse clutch
Piston, low and reverse clutch
Seal, low and reverse clutch (outer/centre/inner)
Orifice cup
Rotor, internal transmission speed sensor