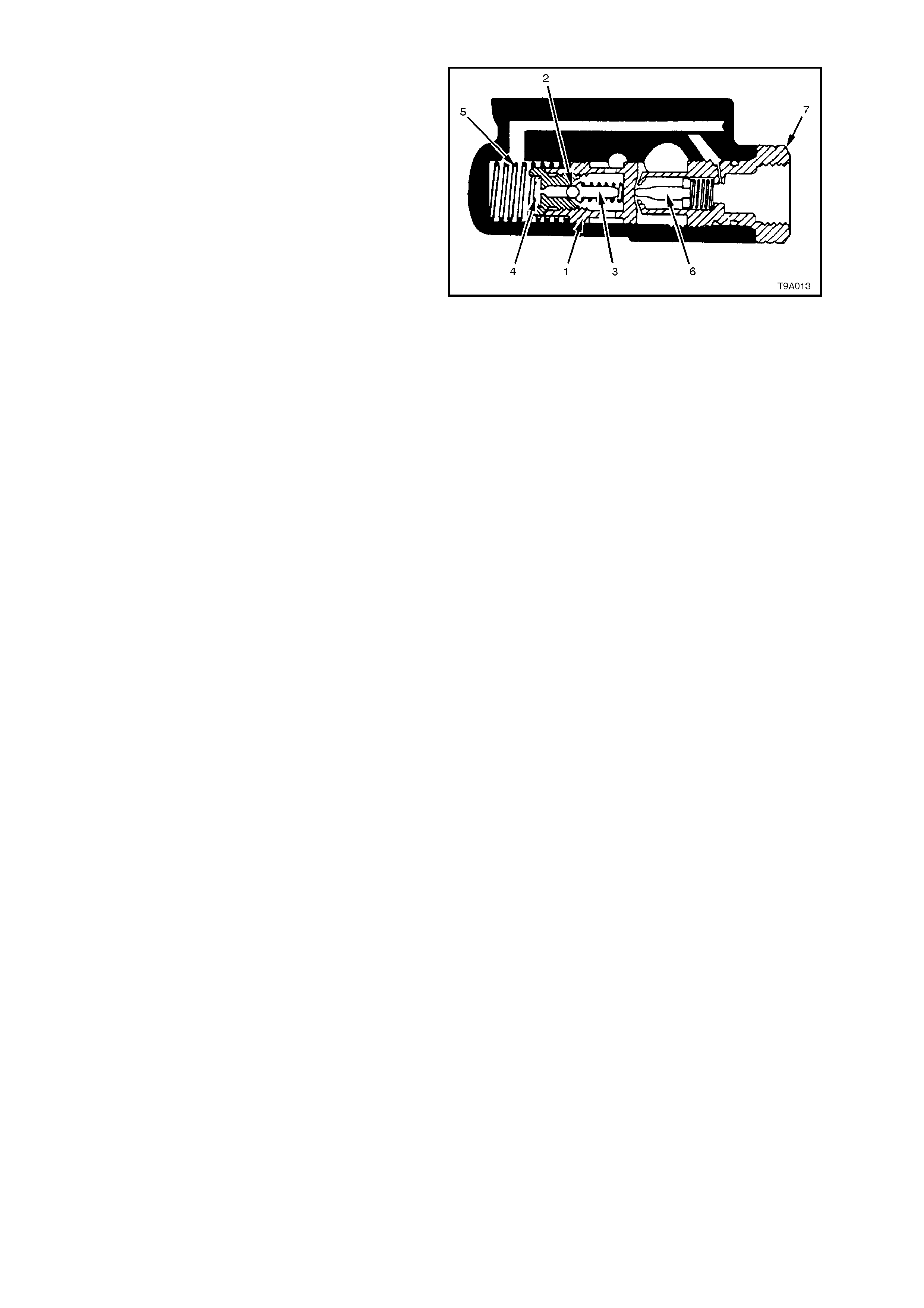
CONTROL VALVE ASSEMBLY
The purpose of the control valve assem bly fitted to
droop flow design pum ps, is to vary power steering
system pressure and fluid flow to the steering gear
as required, under various operating conditions.
The control valve assembly consists of the control
valve plunger (1), an internal pressure relief ball
check (2), ball check guide and ball check guide
spring (3) . A scr een (4) in the end of the plunger, is
designed to keep dirt and foreign material out of the
ball check area.
Movem ent of the c ontrol valve as s embly under fluid
pressure and spring (5) force, acts upon a fluid
control needle and spring (6), in the pump outlet
fitting (7). The needle is tapered and movement
within the outlet fitting orifice hole, changes the
amount of fluid flow to the steering gear.
Figure 9A-12
FILLING THE PUMP
When the pump and power steering gear are
completely empty of fluid, adding fluid to the
reservoir will fill the pump housing assembly.
Suction and gravity draw fluid into the intake
section of the pump, causing it to flow through a
drilled passage in the housing, leading to the large
cavity around the rotor ring. The fluid fills this area
and also the two intake openings on the pressure
and thrust plates, f illing the space between the ring
and rotor assembly. Any air that might enter the
system is automatically removed by the circulating
fluid, from the pump, through the fluid circuit to the
steering gear and then to the reservoir, where it
vents to atmosphere, via the reservoir cap.
PRINCIPLES OF OPERATION
The m ode of oper ation of the power steering pum p
is based upon the demand of the power steering
gear.
The various major modes of operation are:
1. Slow cornering.
2. Moderate to high speed straight ahead driving.
3. Cornering against the wheel stop.
The pump is designed to recognise these
conditions and compensate for them internally .
As the pump drive shaft turns the rotor, the vane
tips follow the inner cam surface of the pump ring,
moving outward and inward twice during each
revolution. This results in a complete pumping
cycle every 180° of rotation. Fluid is moved in the
spaces between the vanes. As the vane tips move
outward, fluid enters the inter -vane spaces through
four suction ports in the pressure and thrust plates .
As the vane tips m ove inwards, the pres sure of the
fluid is raised and the fluid is discharged from the
pump ring. High pressure discharges into a cavity,
behind the pressure plate. A portion of this fluid is
circulated through the central port system in the
pressure plate, forcing the vanes to follow the cam
surface of the ring.
Fluid is discharged from the high pressure cavity,
through the outlet fitting to the steering gear. As the
fluid passes through the outlet fitting, the fluid
pressure drops. This reduced pressure is
transmitted to the spring end of the control valve.