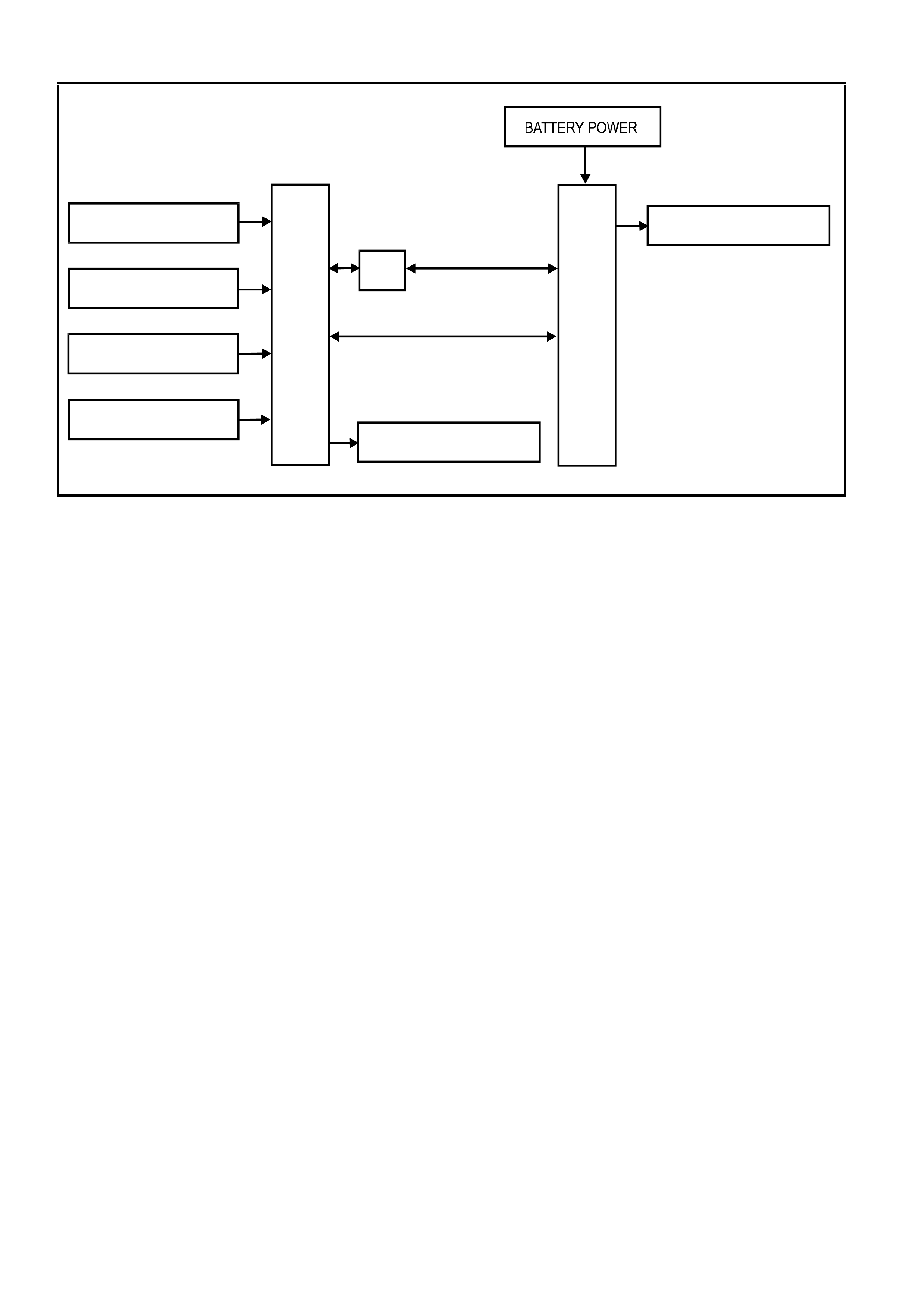
ENGINE COOLI NG FAN APPLICATION
T22A003
PCM
HIGH SPEED COOLING
FAN RELAY
PIM BCM
LOW SPEED COOLING
FAN RE LAY
IGNITION SWITCH ON
VEHICLE SPEED
SENSOR
ENGINE COOLANT
TEMP. SENSOR
AIR CONDITIONING
REQUEST
V6 & V6 S/C ENGINE
GEN III V8 ENGINE
Figure 2A-4 System Overview
VT Series II Models with V6 engines have two single speed electric engine cooling fans; a low speed fan and a high
speed fan (only the low speed fan operates for low speed operation, however, both the high and low fans operate
for high speed). All other VT Series Models, regardless of the engine configuration (including GEN III V8), are
equipped with two, two speed electric cooling fans.
The engine cooling fan assemblies provide the primary means of moving air through the engine radiator. These
fans are placed between the radiator and the engine and have their own shroud. These fans configurations are
used on all vehicles even if not equipped with air conditioning. There is no fan in front of the A/C condenser.
The electric engine cooling fans are used to cool engine coolant flowing through the radiator, and if fitted, refrigerant
flowing through the A/C condenser.
On vehicles with V6 engines, the engine cooling fan motors have two terminals; one positive and one negative. The
positive terminals are permanently connected to battery voltage. When the negative terminal is connected to
earthed through the low speed cooling fan relay, the low speed cooling fan will operate. When the negative terminal
is connected to earth via the high speed cooling fan relay, both cooling fans will operate.
On vehicles with either V6 supercharged or GEN III V8 engines, the engine cooling fan motors have four terminals,
two negative and two positive terminals. The two positive terminals are permanently connected to battery voltage.
When one of the negative terminals is earthed, both cooling fan motors will operate at low speed. When both
negative terminals are earthed, both cooling fans will operate at high speed.
Regardless of the engine configuration, the low speed cooling fan operation is enabled when the low speed engine
cooling fan micro relay (located in the engine compartment relay housing, labelled Lo Fan) is energised by the Body
Control Module (BCM) via a request from the Powertrain Control Module (PCM). The PCM will request low speed
fan enable and disable via serial data communication to the BCM on circuit 1221 (Red/Black wire). After the PCM
requests a change in the state of the low speed relay (i.e. OFF to ON or ON to OFF), the BCM will send a serial
data response message back to the PCM confirming it received the message.
NOTE: On vehicles with GEN III V8 engines, serial data communication between the PCM and BCM is via the
Powertrain Interface Module (PIM).
The PCM determines when to enable the low speed fan relay based on inputs from the A/C request signal, Cooling
Temperature Sensor (CTS) and the Vehicle Speed Sensor (VSS).