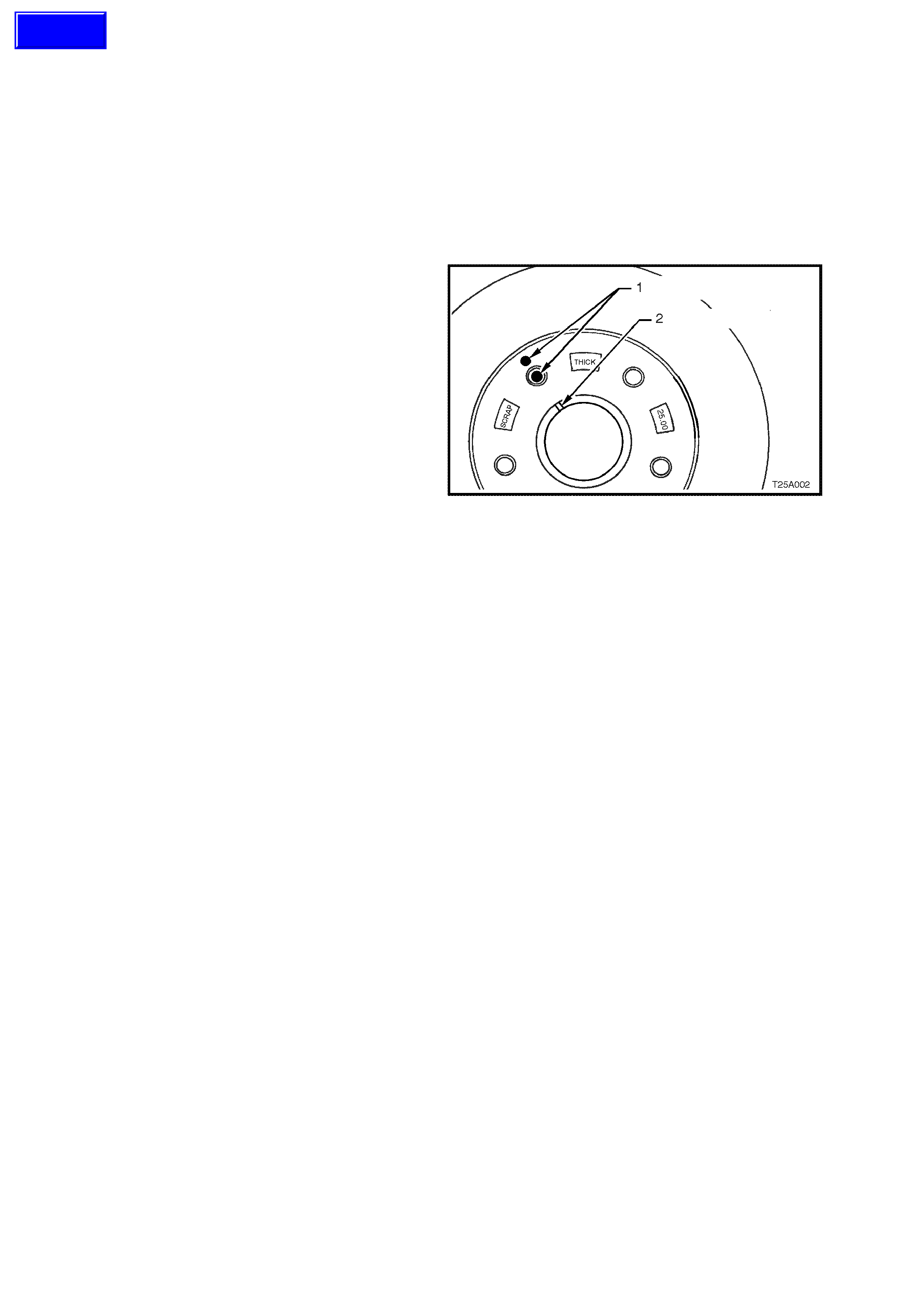
2.1 FRONT BRAKE DISC
CAUTION: Whenever any component that
forms part of the ABS (if fitted) is disturbed
during Service Operations, it is vital that the
complete ABS system be checked, using the
procedure as detailed in DIAGNOSIS, ABS
FUNCTION CHECK, in Section 12L ABS &
ABS/ETC (V6 engine) or Section 12L ABS &
ABS/ETC (GEN III V8 engine) of this Service
Information.
REMOVE
IMPORTANT: T he brake dis c to hub relationship is
carefully matched during production (indexed), to
minimise the effect of a tolerance stack-up, that
could result in disc runout and subsequent brake
shudder.
Therefore, prior to removal of the front brake disc/s,
check to see whether a paint daub mark (1) is still
visible on the brake disc hub surface, adjacent to
one of the wheel studs and in alignment with the
two marks (2) on the end of the hub, as shown.
If the paint marks are no longer visible, then
carefully mark the relationship of the brake disc to
the hub for installation. If this precaution is not
taken, then a disc runout condition could be
induced that will cause brake shudder.
NOTE: If the br ake disc is being removed to rec tify
brake shudder, if the brake disc is to be machined
or replaced, or if brake disc to hub m atching is not
evident, the brake disc to the hub must be indexed.
Figure 5A-2
1. Remove brake calliper assembly, refer to 3.3
BRAKE CALLIPER (FRONT AND REAR), in
Section 5A STANDARD BRAKES of the VT
Series I Service Information.
NOTE: It is not necessary to disconnect the brake
hose from calliper. Support the calliper with a wire
hook to avoid strain on the brake hose.
2. If necessary, jar the brake disc loose by
carefully tapping the disc in the centre
between the wheel studs, with a soft faced
hamm er, tak ing care not to dam age the wheel
stud threads.
INSPECT
If the brak e disc surface is rusted or lightly scored,
resurface disc. Scores less than 0.4 mm deep will
not affect brake performance.
If scoring is deep or if brake disc parameters are
out of specification, the disc must be machined.
NOTE 1: Machine or resurface BOTH sides of
disc. Do not machine or resurface one side only.