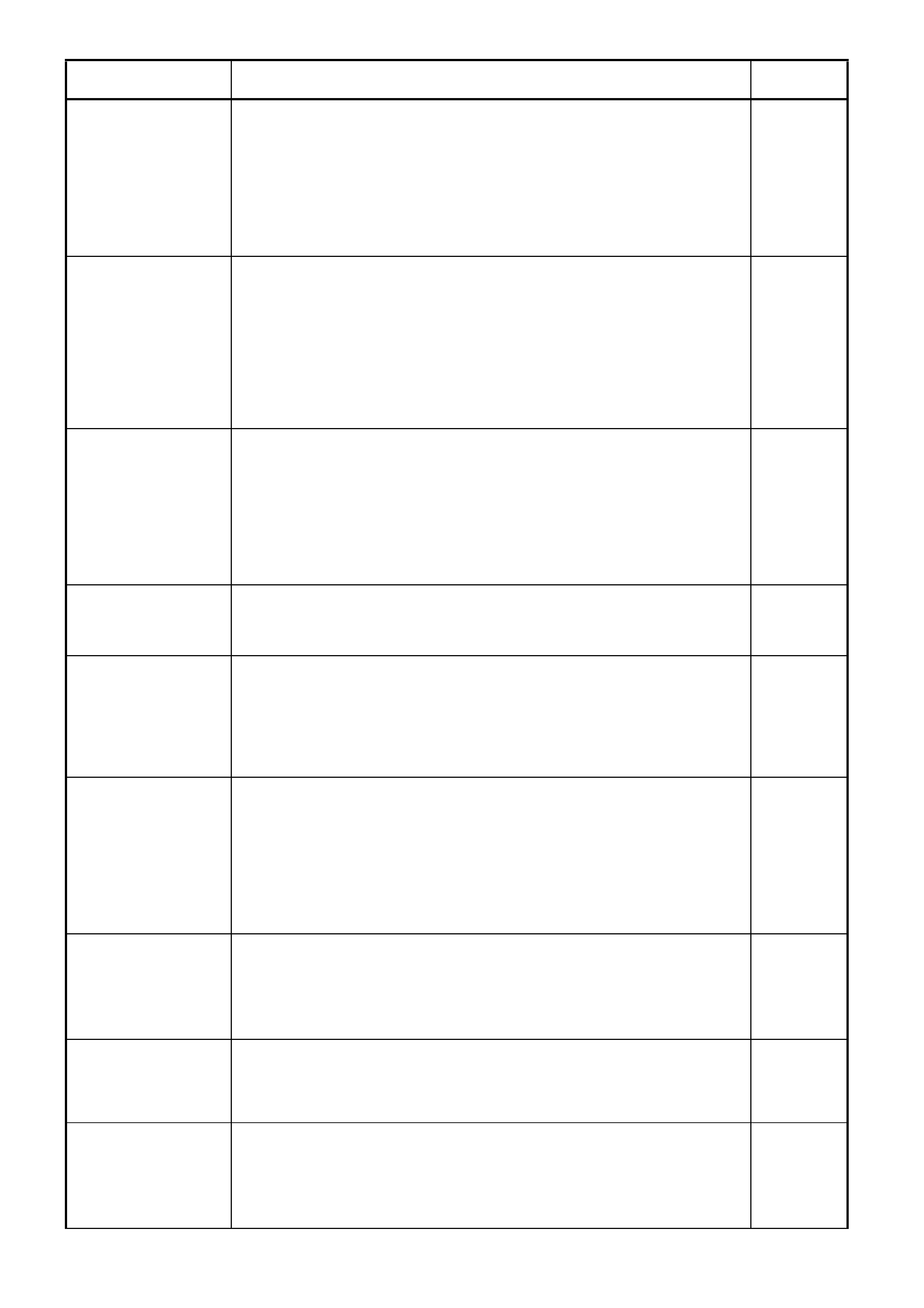
SCREEN DISPLAY DESCRIPTION TERMINAL
AFFECTED
FRONT WASHER
PUMP SWITCH Displays front washer pump switch input to BCM.
W ith ignition on and the washer pump switch activated, screen display changes
from OFF to ON.
If circuit 94, between the BCM and the wiper/washer switch is open circuited, the
wipe after wash function will not operate.
If screen display does not change, check circuit 94 between BCM terminal D18
and wiper/washer switch (including wiper/washer switch contacts), refer to
Section 12C INSTRUMENTS, W IPER/W ASHER AND HORN in the VT Series I
Service Information.
D18
WIPER PARK SWITCH Displays input to BCM.
With wipers in the park position, screen displays ON. With wipers operating,
display will change to OFF and momentarily go to ON as wipers operate through
the park region.
If circuit 196, between the BCM and the wiper motor is open circuited, the screen
will display ON all the time and wipers will not park when turned off.
If screen display remains ON with wipers operating, check for open circuit
between BCM terminal B9 and wiper motor, carry out checks of wiper motor,
refer to Section 12C INSTRUMENTS, WIPER/WASHER AND HORN in the VT
Series I Service Information.
B9
FRONT WIPER
INTERMITTENT
SWITCH
Displays wiper/washer switch intermittent switch contacts input to BCM.
W ith ignition on and wiper/washer switch set to the intermittent position, screen
display changes to ON.
If circuit 97, between the BCM and the wiper/washer switch is open circuited,
there will be no intermittent wiper function.
If screen display does not change, check circuit 97 between BCM terminal D10
and wiper/washer switch (including wiper/washer switch contacts), refer to
Section 12C INSTRUMENTS, W IPER/WASHER AND HORN in the VT Series I
Service Information.
D10
INTERMITTENT
WIPER DRIVE W ith wipers operating in the intermittent mode, screen displays ON. W ith wipers
in the parked position, and in 1st or 2nd speed, screen displays off.
If screen displays are not as described, refer to 4.11 WIPER CONTROL
SYSTEM in this Section.
-
FRONT WIPER
DWELL TIME Displays wiper/washer switch dwell time input to the BCM.
The wiper dwell on vehicles with a low series BCM is a fixed dwell period of
approximately 8.0 seconds and is non-adjustable.
If wipers do not operate intermittently when selected, check for open in circuit 97
between BCM terminal D10 and wiper/washer switch (including wiper/washer
dwell control adjustment contacts, refer to Section 12C INSTRUMENTS,
WIPER/WASHER AND HORN in the VT Series I Service Information.
D10
REAR WASH PUMP
SWITCH Displays rear washer pump switch input to BCM.
W ith ignition on and the washer pump switch activated, screen display changes
from OFF to ON.
If circuit 494, between the BCM and the wiper/washer switch is open circuited,
the wipe after wash function will not operate.
If screen display does not change, check circuit 494 between BCM terminal D19
and wiper/washer switch (including wiper/washer switch contacts), refer to
Section 12C INSTRUMENTS, W IPER/WASHER AND HORN in the VT Series I
Service Information.
D19
REAR WIPER SWITCH Displays rear wiper switch input to BCM.
W ith ignition on and the rear wiper switch in the on position, screen will change
from OFF to ON (this applies to wagon only, on sedan models, the screen will
always display OFF).
If screen displays are not as described, refer to 4.11 WIPER CONTROL
SYSTEM in this Section.
D7
HEATED REAR
WINDOW DRIVE With ignition on, screen display changes from OFF to ON as the heated rear
window is turned on, and then to off as switch is turned off. Also, if turned on, it
will remain on for fifteen minutes, provided the switch is not reactivated and the
screen will then display OFF. This check confirms that the BCM internal circuitry
is operating.
-
HEATED REAR
WINDOW SWITCH Displays heated rear window switch input to BCM.
Display will change from OFF to ON as switch is depressed and held on.
Release switch and display will change to OFF.
If screen does not change, check wiring between BCM terminal D20 and heated
rear window switch and heated rear window switch contacts, refer to 4.9
HEATED REAR WINDOW in this Section.
D20