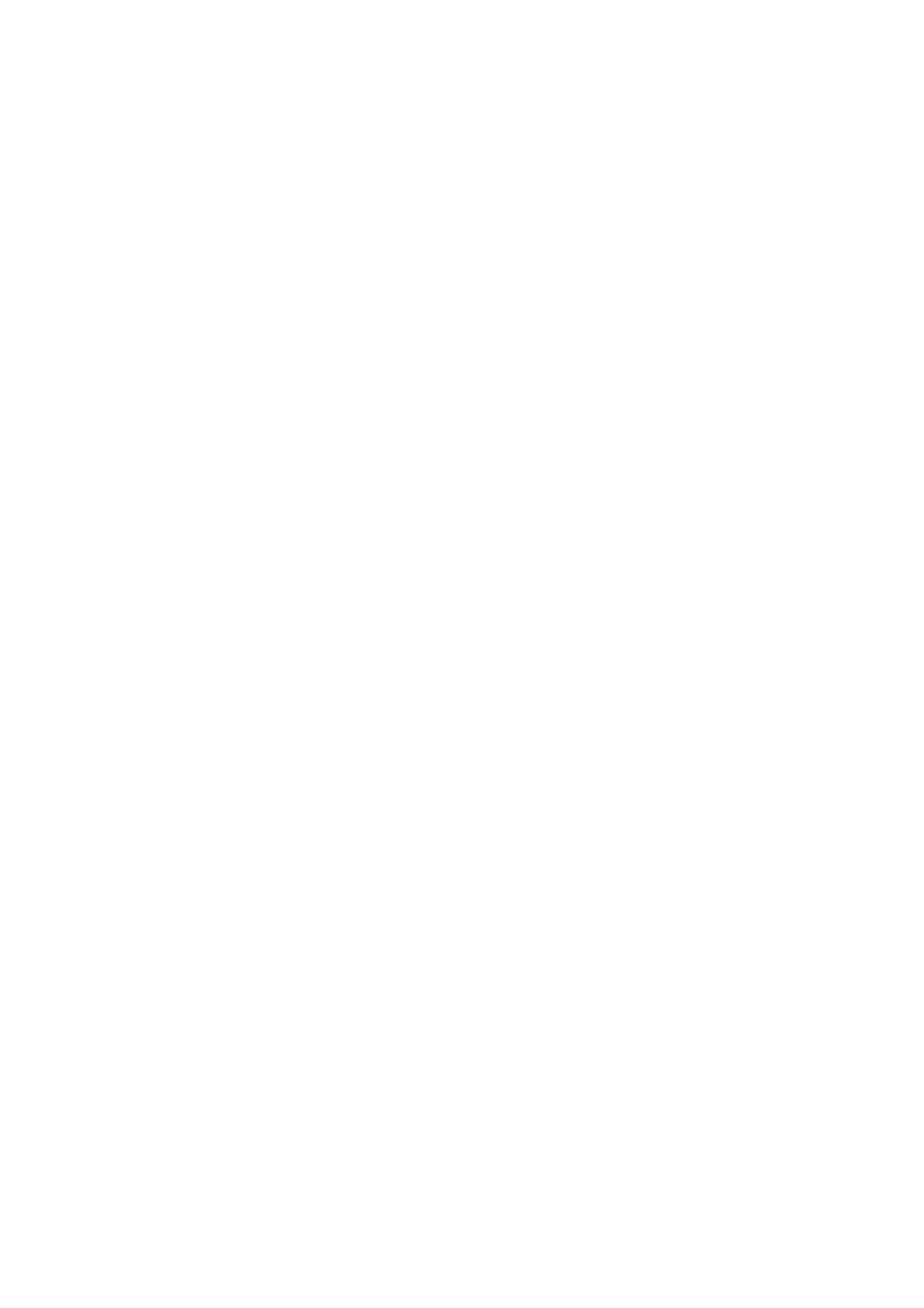
Outputs
To control the anti-lock braking system and traction control system, the ABS/ETC control m odule sends command
signals to the following components.
• Valve relay/solenoid valves - internal control.
• Pump relay/pump motor - internal control.
• Serial data (input and output) - ABS/ETC control module terminal No. 11.
• Self diagnostic 'Flash Code Actuation' - ABS/ETC control module terminal No. 12.
• Requested throttle position - ABS/ETC control module terminal No. 13.
• ETC warning lamp (TRAC OFF, LOW TRAC) - ABS/ETC control module terminal 20.
• ABS warning lamp - ABS/ETC control module terminal No. 21.
• Requested spark retard – ABS/ETC control module terminal No. 28.
With the ignition switch in the on position, batter y voltage is applied to the ABS/ETC control m odule ter m inal No. 15
via fuse F27. Battery voltage is also applied to the pum p motor relay and valve relay via fusible link FR. Neither of
the relays operate until they receive an earth from the ABS/ETC control module.
Also, battery voltage is supplied to the ABS and ETC warning lamps via fuse F13. The LOW TRAC and ABS
warning lamp s will not illum inate until they are earthed by ABS/ETC control m odule. If the ABS/ET C c ontrol module
wiring harness connector YE98, is not connected to the control module, terminals 19, 20 and 21 are shorted
together by a shorting bar, and the LOW TRAC and ABS warning lamps will be illuminated. The TRAC OFF warning
lamp is defaulted to the on position and is turned off via a serial data message from the ABS/ETC control module
when the ignition is turned on (provided the system is OK).
Wheel speed sensors are located at each front wheel and at each final drive inner axle flange. When the vehicle
starts m oving, all of the speed sensors create signals that are input to the ABS/ET C control module at terminals 1
and 2, 4 and 5, 6 and 7, 8 and 9. These signals are AC electrical pulses that are proportional (in frequency and
amplitude) to wheel rotational speed.
Once the vehicle has been started and dr iven over approx imately 6 km /h, the c ontro l module perf or ms an ABS/ETC
self test. The control module test cycles each solenoid valve and the return pump in the hydraulic modulator to
check component operation. The control module checks its own logic section and circuitry. If errors are detected
during this test, the control module earths terminal 20, illuminates the ABS warning lamp and also sends a
message, via the serial data circuit, commanding the TRAC OFF warning lamp to be illum inated. The ABS and/or
ETC warning lamp/s are illuminated to warn the driver of a problem with the system/s. The ABS/ETC control module
remains deactivated until the next ignition switch OFF to ON cycle when the process is repeated and the ABS
and/or TRAC OFF warning lamp/s will be illuminated.
The ABS self test occurs once each ignition cy cle as follows:
1. After receiving an ignition ON input, the control module earths and activates the valve relay.
2. As soon as the ABS/ETC control module receives a signal from any of the wheel speed sensors, it checks
wheel speed sensor output. If any of the wheel speed sensor signals are not detected, or are incorrect, the
ABS/ETC system will be disabled and the warning lamps will be illuminated.
3. When the vehicle reaches approximately 6 km/h, the control module tests the solenoid valves and the return
pump in the modulator. If the control lamp switch receives a brake lamp switch input before the vehicle has
reach 6 km/h, the self test will not occur until the vehicle reaches a road speed of approximately18 km/h.
4. If the pum p or s olenoid valves f ail to operate, the ABS/ET C s ystem will be dis abled and the warning lam ps will
be illuminated.
Once the vehicle is moving, the control module continuously monitors itself and the following components:
1. Solenoid valves.
2. Wheel speed sensors.
3. Wiring harness and relays.
4. Battery voltage.
If battery voltage drops below approximately 9 volts, the ABS/ETC will be disabled and the ABS and TRAC OFF
warning lamps will be illuminated, while the voltage remains below 9 volts.
During braking applications, if one or more wheels start to decelerate too quickly, the ABS is engaged and the
modulation process begins. Wheel speed information sent to the ABS/ETC control module is processed and the
module deter mines pr oper solenoid valve oper ation in the modulator. The modulator c ontains ten s olenoid valves ; a
priming and switching relay, plus one inlet and one outlet valve for each wheel.
When wheel spin is detected and traction control mode begins, the ABS/ETC control module also engages ABS
through the modulation process. Additionally, the ABS/ETC control module simultaneously changes the engine
output conditions by reducing the amount of spark advance and reducing the throttle opening.