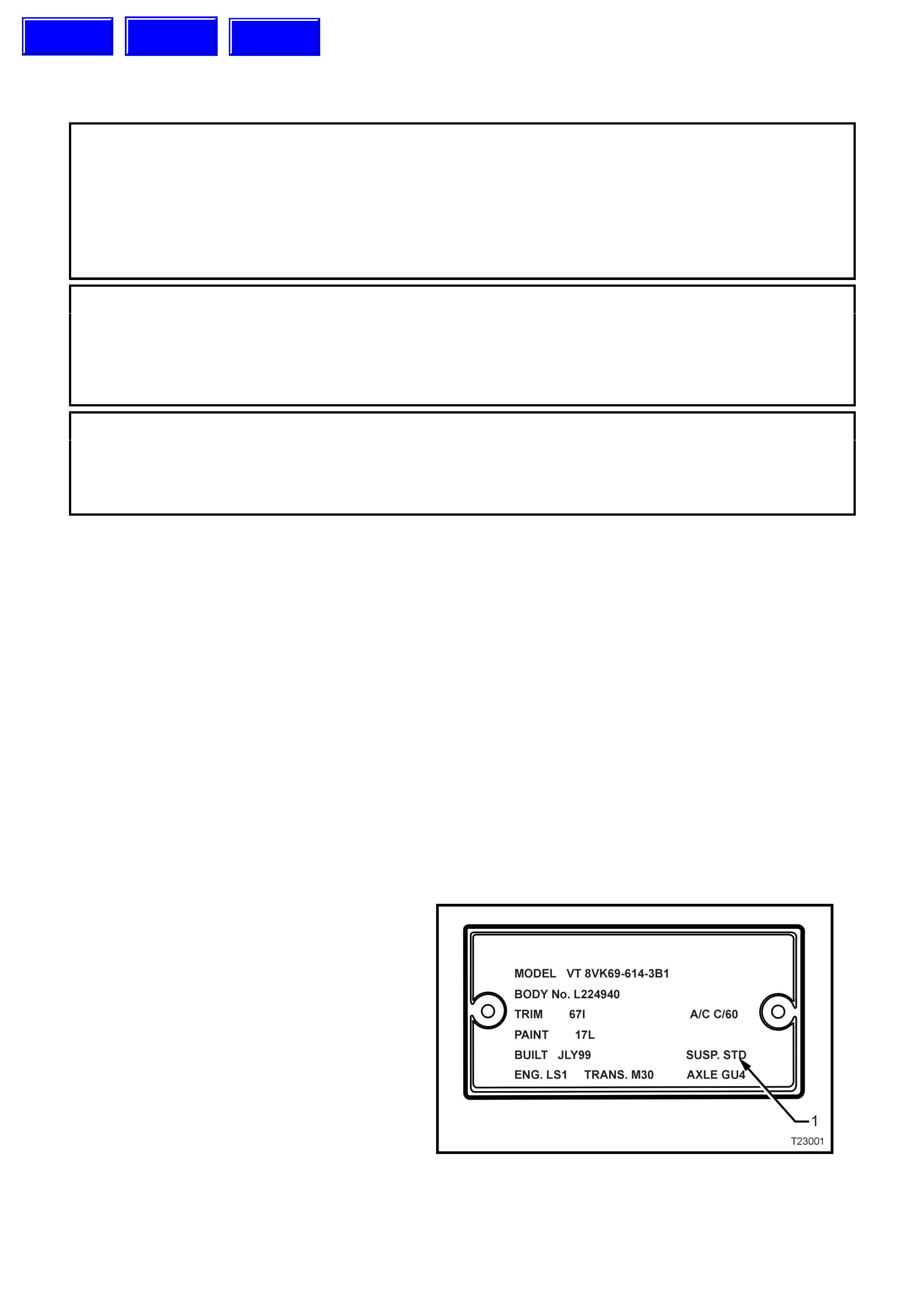
SECTION 3 - FRONT SUSPENSION
CAUTION:
This vehicle will be equipped with a Supplemental Restraint System (SRS). A SRS will consist of either
seat belt pre-tensioners and a driver's air bag, seat belt pre-tensioners and a driver's and front
passenger's air b ags or seat belt pre- tensioners, driv er’s and front passenger’s air bag and left and right
hand side air bags. Refer to SAFETY PRECAUTIONS, Section 12M, Supplemental Restraint System of
this Service Information CD before performing any service operation on, or around any SRS
components, the steering mechanism or wiring. Failure to follow the SAFETY PRECAUTIONS could
result in SRS deployment, resulting in possible personal injury or unnecessary SRS system repairs.
CAUTION:
This vehicle may be equipped with LPG (Liquefied Petroleum Gas). In the interests of safety, the LPG
fuel system should be isolated by turning ‘OFF’ the manual service valve and then draining the LPG
service lin es, b efo re any serv ice work is carried o ut on th e v ehi cle. Refer t o t he L PG leaf let in clud ed with
the Owner's Handbook for details or the appropriate Section of this Service Information CD for more
specific servicing information.
CAUTION:
Whenever any component that forms part of the ABS or ABS/ETC (if fitted), is disturbed during Service
Operations, it is vital that the complete ABS or ABS/ETC system is checked, using the procedure as
detailed in 4. DIAGNOSIS, ABS or ABS/ETC FUNCTION CHECK, in Section 12L ABS & ABS/ETC (V6
Engine) or (GEN III V8 Engine) of this Service Information CD.
1. GENERAL DESCRIPTI ON
Changes to the front suspension for VT Series II
vehicles are minor and are as follows:
a. Re-introduction of V5W Country Pack
suspension to VT series Sedan and Station
Wagon vehicles.
b. Revisions to some wheel alignment angles
and changes to suspension specifications to
reflect the introduction of the GEN III V8
engine and optimise vehicle ride
characteristics.
c. Apart f rom the notes contained in this Section,
all service operations remain unchanged from
those published Section 3 FRONT
SUSPENSION of the VT Series I Information.
For identification information and specification
details for the different suspension components
available for VT Series II vehicles, refer to
4. SPECIFICATIONS in this Section.
To identify the suspension fitted to an individual
vehicle, refer to “SUSP” (1) on the Body, Option
and Identification Plate.
For the location of this plate, refer to Section 0A
GENERAL INFORMATION, of this Service
Information CD.
Figure 3-1