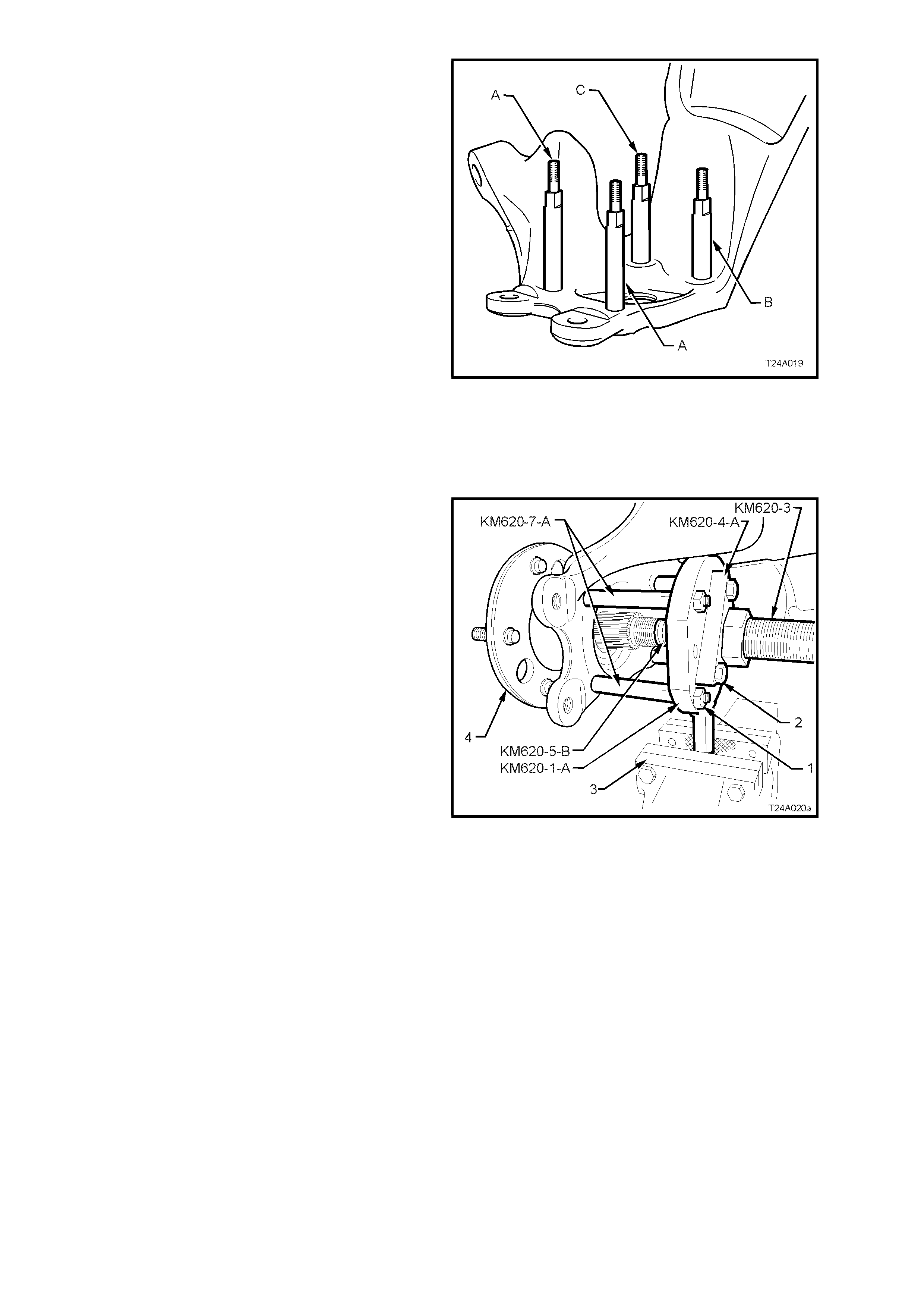
10. Preparatory to removing the trunnion assembly
and rear wheel bearing from the trailing arm,
use a commercially available M10 x 1.25
bottoming tap and clean the four backing plate
to trailing arm bolt threads, using a suitable
lubricant and working from the trunnion
assembly side.
NOTE: This step is necessary to clear any dried
mud, dirt etc, from the exposed portion of the
threads on the inboard side of the trailing arm.
Also, the deepest thread (position ‘C’) may not be
completely formed through to the inboard side.
11. Install two supports KM620-7-A in positions ‘A’
and two KM620-7-AUS to ‘B’ and ‘C’ in the
trailing arm, as indicated.
As a guide, the two longest supports (KM620-
7-A) are to be installed at the brake caliper
mounting side (position ‘A’). The longer of
KM620-7-AUS supports is installed at position
‘B’ and the shorter is installed at position ‘C’.
12. After installing all four supports in the correct
positions, tighten with a set spanner.
Figure 4A-21
13. Install flange holding tool KM620-1-A over the
four supports, KM620-7-A (2 places) and
KM620-7-AUS (2 places), install four suitable
nuts (1) and tighten to secure.
14. Pre-assemble lubricated forcing screw KM620-
3 to adaptor KM620-4-A. Apply grease to ball
end of plunger KM620-5-B, then install that,
into the end of forcing screw KM620-3.
15. Install this sub-assembly through the central
opening of holding tool KM620-1-A. Secure the
adaptor KM620-4-A to the flange holding tool
KM620-1-A, using three suitable bolts (2).
NOTE: Adjust the position of the forcing screw
KM620-3 into the adaptor KM620-4-A, to allow full
contact of the adaptor to the flange holding tool
KM620-1-A.
16. Tighten the three bolts securing adaptor
KM620-4-A to the flange holding Tool KM620-
1-A.
17. Mount assembly in vice (3) by the handle of
flange holding tool KM620-1-A as shown, then
turn the forcing screw KM620-3 and press the
trunnion assembly (4) from rear wheel bearing.
18. When trunnion has been removed, unscrew
the forc ing screw, as this sam e arrangem ent is
used to press the rear wheel bearing from the
trailing arm.
NOTE: The inner rear wheel bearing cone will
separate from the bearing assembly and be
retained on the trunnion assembly.
19. Remove the brake backing plate and park
brak e assem bly from the trailing ar m and set to
one side.
Figure 4A-22