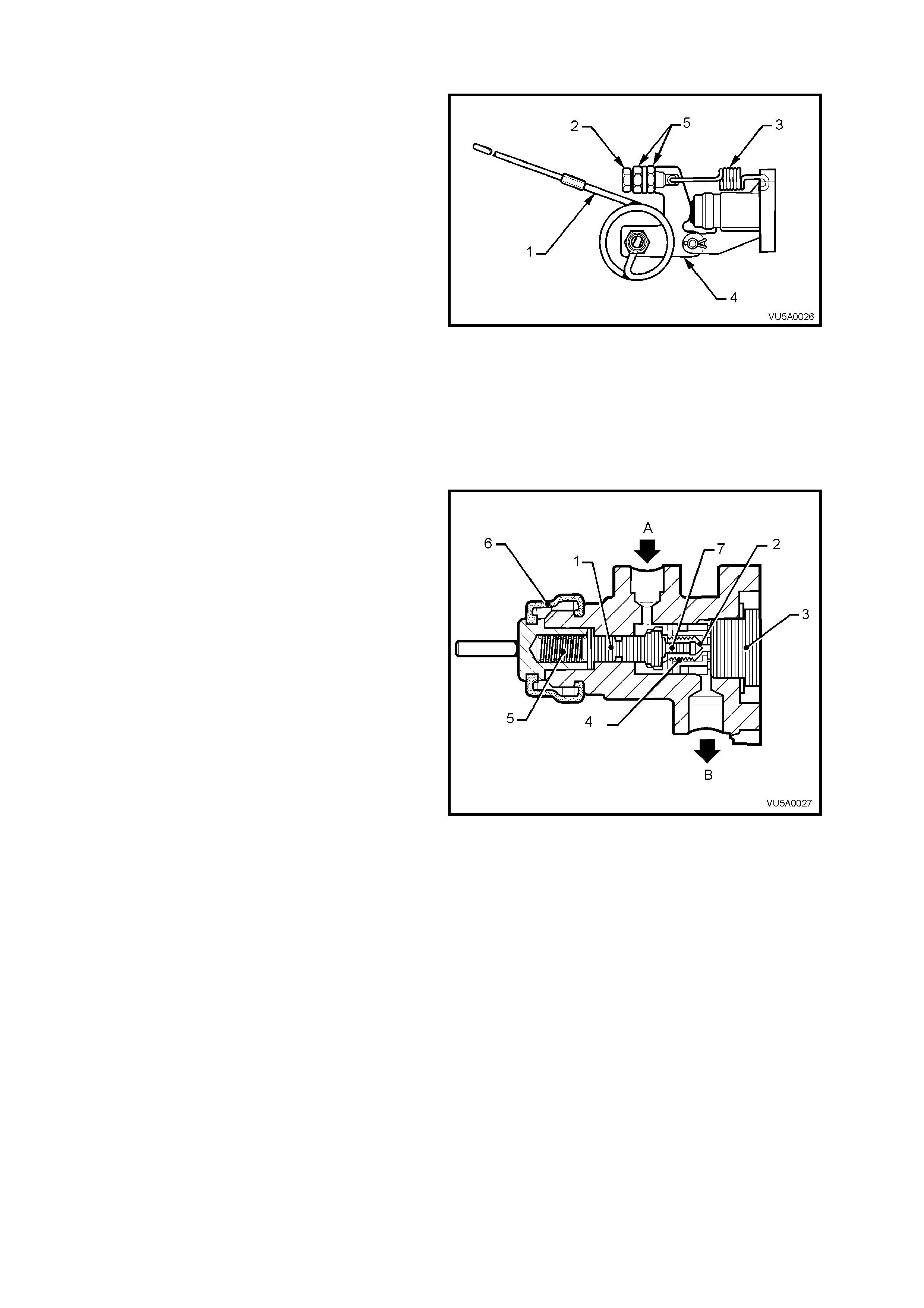
1.2 LOAD SENSING PROPORTIONING VALVE - PRINCIPLES OF OPERATION
CONSTRUCTION
The loa d sens ing propor tio ning va lve is att ached to
the right hand frame, above the final drive
assembly. The valve torsion spring lever is
attached to the right hand trailing arm rod with a
bracket, cable and hook.
The load sensing proportioning valve senses load
by monitoring the rear suspension ride height, to
regulate the pressure applied to the rear brake
calipers. Maximum line pressure is supplied to the
rear brakes when the vehicle is fully laden, while
lightly loaded conditions provide minimum line
pressure; i.e. line pressure varies in relation to the
weight of the load.
Legend
1. Sensing torsion spring
2. Adjusting screw
3. Static spring
4. Torsion spring lever
5. Adjusting screw lock nuts
Figure 5A-9
OPERATION
The static spring exerts a force on the end of the
spool by means of a lever, while a torsion type
sensing spring attached to the right-hand trailing
arm rod modifies this applied force, depending on
the axle load.
When the vehicle is unladen or lightly loaded, the
torsion spring has the maximum effect and,
together with the static spring force, the total apply
force on the plunger and piston is lowest. This
apply force is able to position the load sensing
piston to restrict the flow of fluid through the outlet
port to the rear brakes.
However, when the vehicle is loaded, the spool is
positioned so that fluid can flow unrestricted
through the inlet port, through the spool sub-
assem bly, around th e poppet valve and out via th e
spool sub assembly sealing seat and outlet port to
the rear wheel calipers.
When the brake pedal is released, inlet pressure
drops, allowing the higher pressure on the rear
wheel side of the sensing valve to force upon the
poppet valve, such that the brake fluid can flow
almost unrestricted, back to the master cylinder.
Eventually, the spool is forced into its released
position by the external spring set up, to fully open
the passage between the front and rear circuit.
NOTE: The static spring tension is pre-set and
should not be adjusted.
Figure 5A-10
Legend
1. Load sensing valve spool
2. Load sensing valve spool sealing seat
3. Load sensing valve end plug
4. Secondary spring
5. Primary spring
6. Load sensing valve boot
7. Load sensing valve poppet and valve
A. Brake fluid inlet
B. Brake fluid outlet