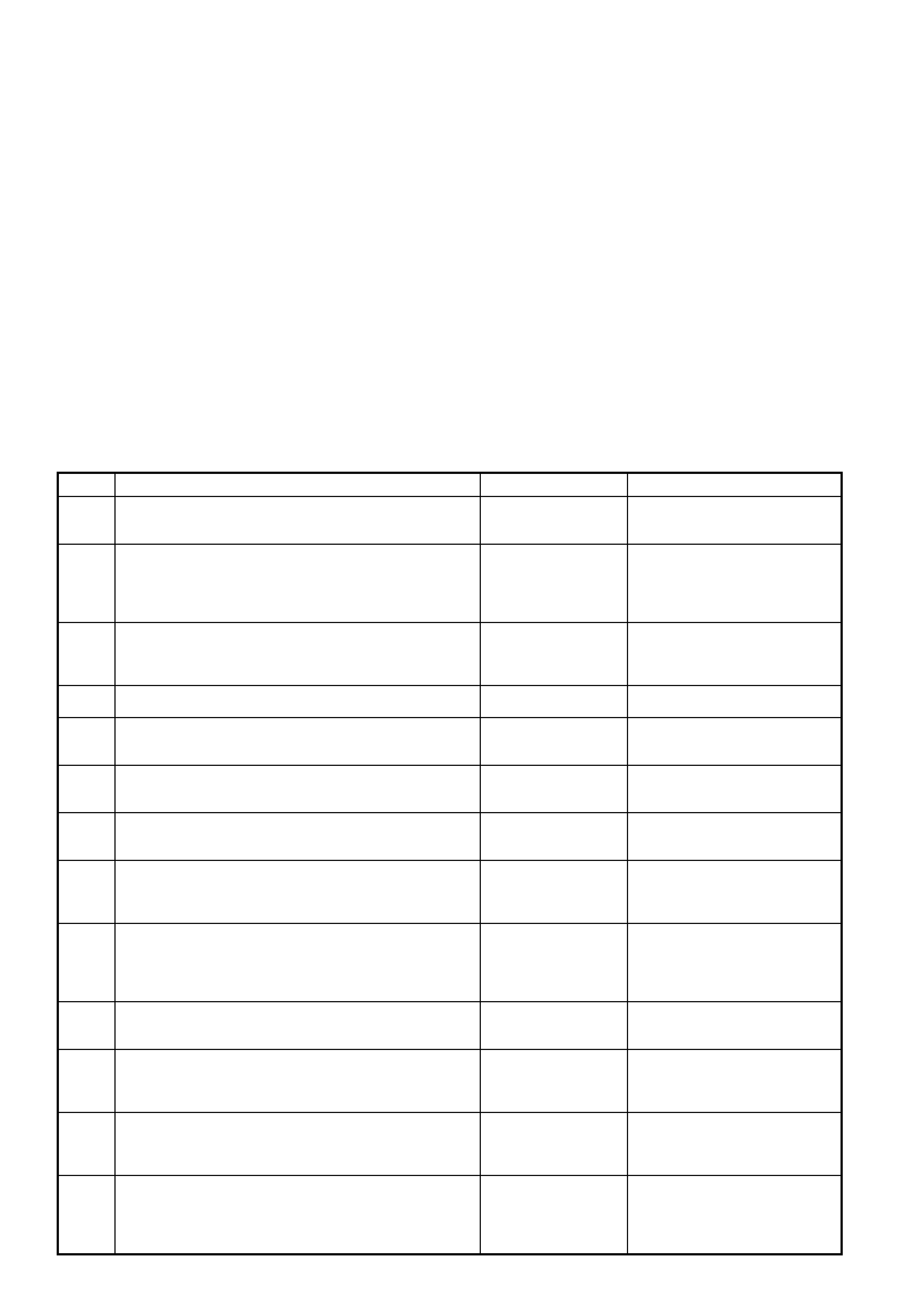
4.9 ENGINE BACKFIRES ON LPG
TEST DESCRIPTION
The numbers below refer to step numbers in the following diagnostic chart.
NOTE: Whenever a engine backfire has occurred the complete intake system including the mixer should be
checked for damage.
1. The LPG VEHICLE PRELIMINARY DIAGNOSIS CHECK must be the first step when diagnosing any LPG
system problem.
2. An ON BOARD DIAGNOSTIC SYSTEM CHECK should be performed to confirm that a problem with the
Powertrain Management system is not causing the engine to backfire when operating on LPG?
3-7 An ignition system that is not operating at it’s full potential can cause an engine to backfire when operating on
LPG. Ignition leads that operate quite well when operating on petrol, can cause problems when operating on
LPG. Therefore, all ignition system components must be at here optimum when operating on LPG.
8. Vacuum leaks or blocked vacuum lines can cause incorrect system operation, causing engine backfire.
9. Incorrect mixer operation can cause incorrect air/fuel ratios. Incorrect air/fuel ratios can cause engine backfire.
10. Incorrect ADP set-up can cause incorrect system operation, causing engine backfire.
11. Incorrect converter operation can cause incorrect air/fuel ratios. Incorrect air/fuel ratios can cause engine
backfire.
12. This test confirm correct Regulator Check Valve (RCV) operation, incorrect RCV operation can cause slow
converter response causing engine backfire.
13. Engine mechanical condition can cause engine operating problems that do not effect the engine when operating
on petrol. The engine must be in optimum operating condition to prevent the engine backfiring when operating
on LPG.
STEP ACTION YES NO
1. 1. Has an LPG VEHICLE PRELIMINARY DIAGNOSIS
CHECK been performed. Go to step 2 Perform an LPG VEHICLE
PRELIMINARY DIAGNOSIS
CHECK.
2. 1. Has an ON BOARD DIAGNOSTIC SYSTEM CHECK
been performed?
Refer ON-BOARD DIAGNOSTIC SYSTEM CHECK,
Section 6C1 in this Service Information.
Go to Step 3. Perform ON-BOARD
DIAGNOSTIC SYSTEM
CHECK. Refer Section 6C1 in
this Service Information.
Recheck for engine backfire.
3. 1. Check spark plug leads for tracking or cracks in
insulation and resistance (refer Section 6D1 in this
Service Information).
2. Are the spark plugs leads OK?
Go to Step 4. Replace spark plug leads.
Recheck for engine backfire.
4. 1. Remove and inspect spark plugs for fouling.
2. Are the spark plugs OK? Go to Step 5. Replace spark plugs. Recheck
for engine backfire.
5. 1. Re-gap spark plugs to minimum specification.
2. Have spark plugs been re-gaped to minimum
specification?
Go to Step 6. Re-gap spark plugs to
minimum specification
Recheck for engine backfire.
6. 1. Check coil resistance (refer Section 6D1 in this
Service Information).
2. Is the ignition coil resistance within specification?
Go to Step 7. Replace faulty ignition coil.
Recheck for engine backfire.
7. 1. Check PCM, DIS and Crank Angle sensor wiring
harness terminal retention.
2. Is terminal retention OK?
Go to Step 8. Resize terminals. Recheck for
engine backfire.
8. 1. Check for vacuum leaks in vacuum or vapour feed
lines between mixer and converter, or a blocked
balance line, FCV or Regulator Check Valve.
2. Are there any leaks or blockages?
Repair vacuum
leaks or blockages.
Recheck for engine
backfire.
Go to Step 9.
9. 1. Test mixer operation (refer 3.4 MIXER in this
Section).
2. Is mixer operating correctly?
Go to Step 10. Overhaul mixer. Refer 2.18
MIXER in the VT Series I
Service Information - LPG
System.
Recheck for engine backfire.
10. 1. Is the LPG Setup correct?
(refer 3.5 LPG SETUP PROCEDURE in this
Section).
Go to Step 11. Carry out LPG Setup
Procedure.
Recheck for engine backfire.
11. 1. Test converter pressures. (Refer 3.1 CONVERTER
in this section).
2. Are converter pressures OK?
Go to Step 12. Overhaul converter.
(Refer 2.15 CONVERTER in
the VT Series I Service
Information - LPG System).
12. 1. Test Regulator Check Valve operation (refer 3.2
REGULATOR CHECK VALVE in this Sec t ion).
2. Is Regulator Check Valve operating correctly?
Go to Step 13. Replace Regulator Check
Valve (refer 3.2 REGULATOR
CHECK VALVE in this Section)
Recheck for engine backfire.
13. 1. Check engine mechanical condition by checking
compression, valve timing, intake and exhaust
valves and manifolds for casting flash.
2. Is the engine mechanical condition OK?
Check for incorrectly
routed harnesses,
ignition leads
or non genuine
accessories.
Repair any faults. Recheck for
engine backfire.