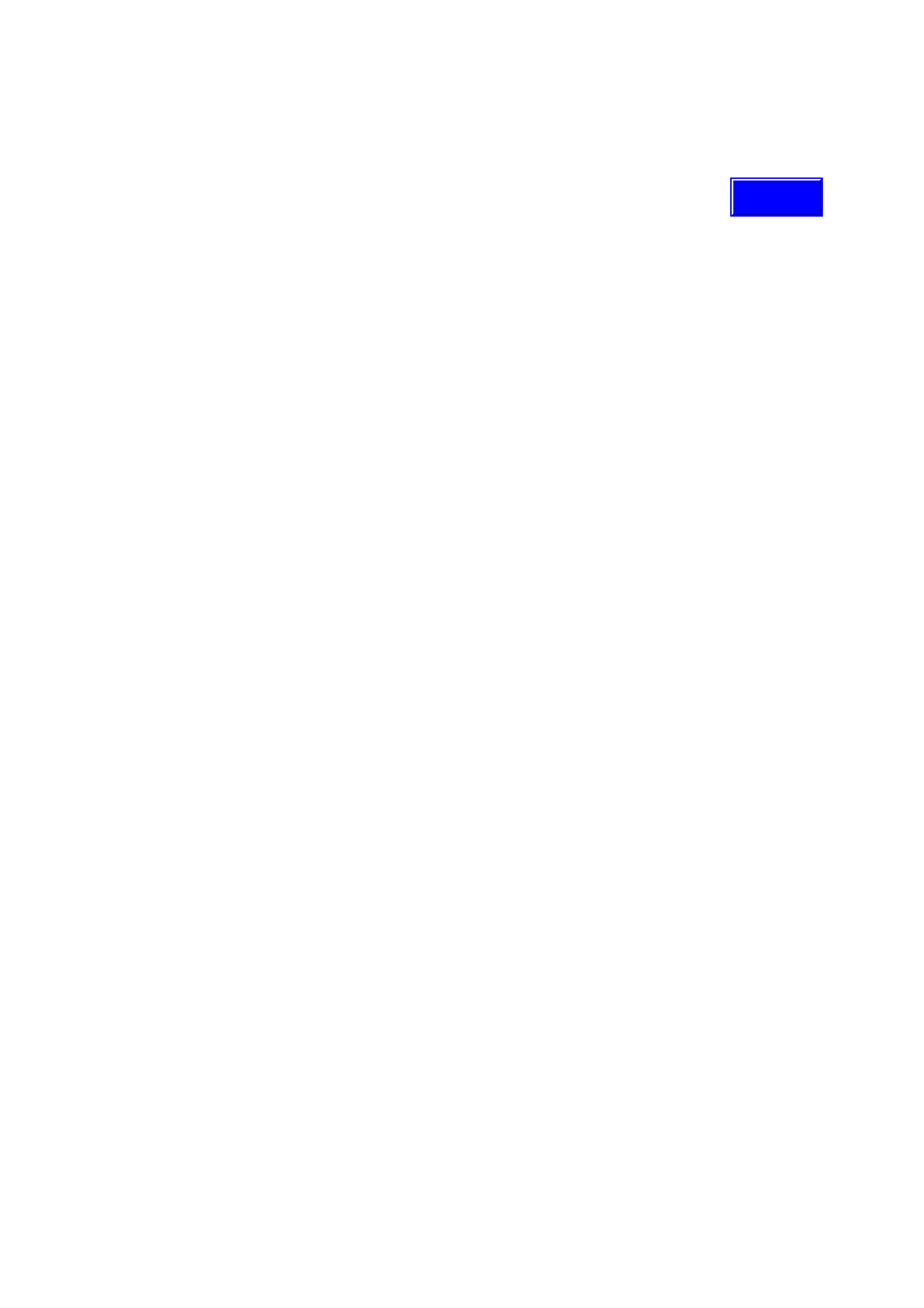
4. SPECIFICATIONS
General
Radiator Cap Pressure Rating ................................ 96.5 to 124 kPa
Cooling System Capacity........................................ 14.3 Litres
Coolant Corrosion Inhibitor...................................... DEX-COOL® to GM Specification 6277M, approx. 7.0
litres required when changing coolant.
Thermostat
Type ........................................................................ Power element (wax pellet)
Start to open at........................................................ 86°C
Fully open at............................................................ 100°C
Coolant Pump
Type ........................................................................ Centrifugal
Drive........................................................................ Multi-ribbed, Serpentine V-belt
Bearing Type........................................................... Double-row ball bearing
Radiator
Core type................................................................. Aluminium crossflow core
Overall Width........................................................... 826 mm
Overall Height.......................................................... 495 mm
Core Width.............................................................. 674 mm
Core Height............................................................. 427 mm
Core Thickness....................................................... 35 mm
Plastic tanks............................................................ Nylon 6,6 (30% glass filled)
Radiator Hoses
Lower – Number and type....................................... Two, Moulded
Upper – Number and type....................................... One, Moulded
Engine Cooling Fan – LHS
Fan – Design.............................................................. Asy mmetrically spaced, curved blades with outer ring
Material.................................................................... Nylon 6,6 (25% glass filled), with zinc coated metal
hub insert
Number of Blades ................................................... 5
Diameter.................................................................. 293 mm
Fan Motor – Type ...................................................... Twin speed, 4 brush with 4 permanent magnets
Housing................................................................... Semi-sealed, zinc coated steel with drain hole
Direction of Rotation................................................ Counter-clockwise (as viewed from motor side)
Power...................................................................... 180 Watts (nominal)
Rotational Speed wi th 12 volts applied, Radiator
and Condenser Installed:
Stage 1............................................................... 2,050 ± 150 rpm
Stage 2............................................................... 2,300 ± 150 rpm
Engine Cooling Fan – RHS
Fan – Design.............................................................. Asy mmetrically spaced, curved blades with outer ring
Material.................................................................... Nylon 6,6 (25% glass filled), with zinc coated metal
hub insert
Number of Blades ................................................... 5
Diameter.................................................................. 342 mm
Fan Motor – Type ...................................................... Twin speed, 4 brush with 4 permanent magnets
Housing................................................................... Semi-sealed, zinc coated steel with drain hole
Direction of Rotation................................................ Counter-clockwise (as viewed from motor side)
Power...................................................................... 220 Watts (nominal)
Rotational Speed wi th 12 volts applied, Radiator
and Condenser Installed:
Stage 1............................................................... 2,350 ± 150 rpm
Stage 2............................................................... 2,750 ± 150 rpm