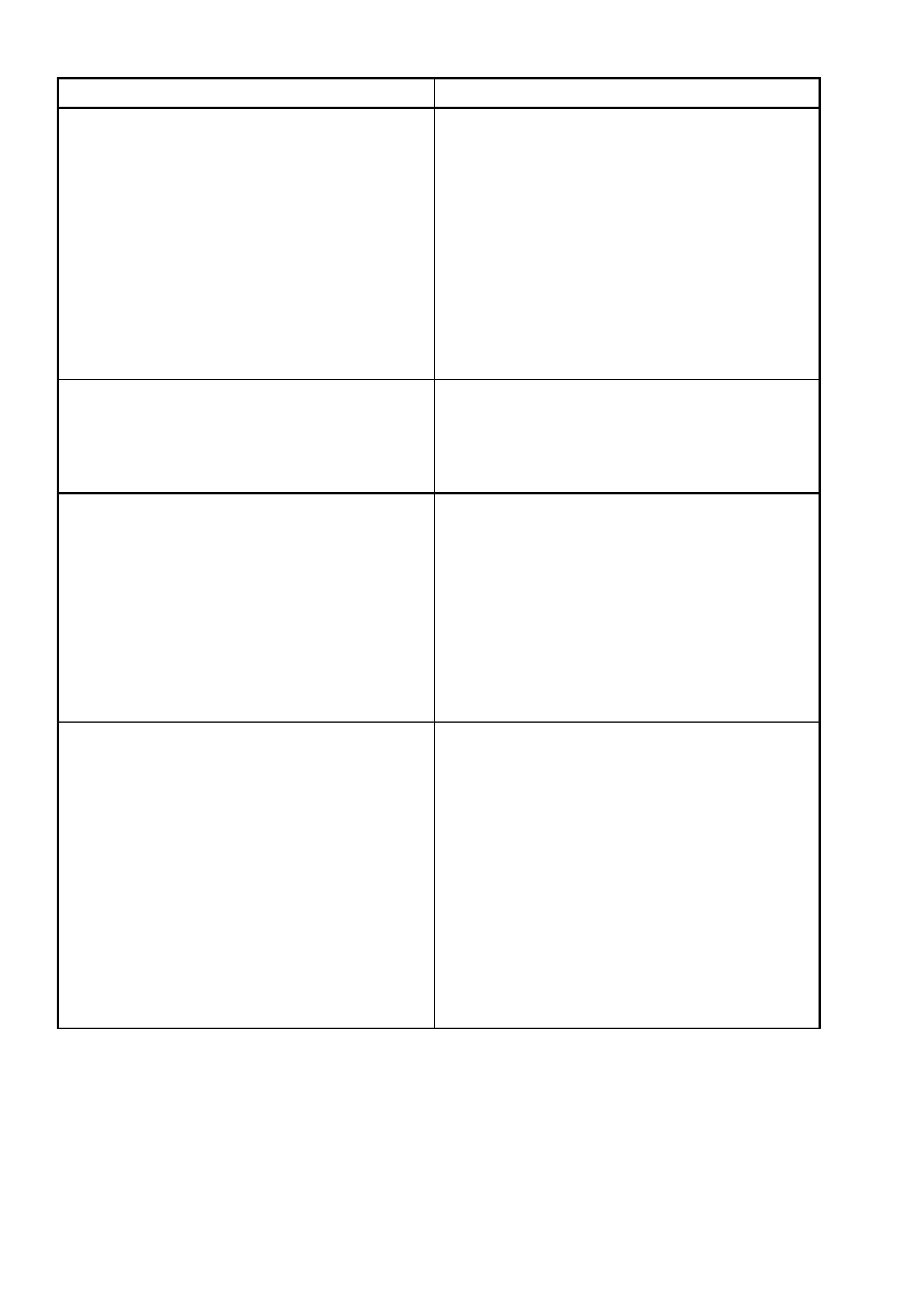
4.1 DIAGNOSIS GUIDE - Cont'd
SYMPTOM AND PROBABLE CAUSE REMEDY
VEHICLE PULLS TO ONE SIDE
1. Low or uneven tyre pressures.
2. Rear wheels not tracki ng with f ront wheels.
3. Front brake pads cont aminated with l ubri cant.
4. Toe-in incorrect.
5. I n correct or uneven c aster or camber.
6. Rear axle assembly s hi fted.
7. S teering knuckle bent.
1. I nflate tyres to specified press ure f or specifi c load
conditi ons. Refer t o tyre placard att ached to the vehicle.
2. Chec k alignment of rear wheels with front wheels and
correct as necessary. Refer t o Secti on 4A , REAR
SUSPE NS ION for detail s of rear wheel alignm ent.
3. Replace brake pads. Correct c ause of lubric ant leakage. Refer
to Section 5A, SERVICE AND PARK BRAKING SYSTEM.
4. A dj ust toe-in to specificati on. Refer to 2. 2 WHEEL
ALIGNMENT CHECKING AND ADJUSTMENT in this Section.
5. Chec k wheel alignment. Adjust as nec essary. Ref er to 2.2
WHEEL ALIGNMENT CHECKING AND ADJUSTMENT in this
Section.
6. Chec k attac hi ng bol ts for looseness and front lower control
arm bus hi ng for wear. Refer to Section 4A, REAR
SUSPENSION.
7. Replace steeri ng knuckle. Refer to 3. 9 S T EERING KNUCK LE
in this Section.
FRONT OR REAR WHEEL TRAMP
1. Wheels and tyres out of balance.
2. Front struts or rear shock absorbers operating
incorrectly, leaking fluid or inoperative.
1. B al ance wheels and tyres. A l so check for ecc entric or
bulged tyres. Repl ace as necessary. Ref er to Sect i on 10
WHEELS AND TYRES.
2. Chec k operation and replace com ponents as nec essary.Ref er
to 3.8 FRONT ST RUT UNI T i n t hi s sect i on or S ection 4A,
REAR SUSPENSION as necessary.
ROAD SHOCKS
1. Incorrect tyre pressures.
2. S teering gear incorrectly adjus ted.
3. Front struts or rear shock absorbers operating
incorrec tly or unevenly, leaking flui d or i noperative.
4. Compress i on or rebound rubbers damaged or missing.
5. Unbalanced wheels.
6. I ncorrect wheel alignment.
1. I nflate tyres to specified press ure f or specifi c load
conditi ons. Refer t o tyre placard att ached to the vehicle.
2. A dj ust st eeri ng gear. Refer to S ection 9, STEERI NG for
details.
3. Chec k operation and replace com ponents as nec essary.
Refer to 3.8 FRONT S T RUT UNI T i n this sec tion or
Sect i on 4A, REAR SUSPENSION as necessary.
4. Replace missing or damaged parts. Refer to 3.8 FRONT
STRUT UNIT i n this Section or Section 4A, REAR
SUSPENSION as necessary.
5. B al ance wheels as detail ed i n Section 10, WHEELS AND
TYRES.
6. Chec k and adjust. Refer to 2. 2 WHEEL ALI GNMENT
CHECKING AND ADJUSTMENT in this Section.
SCUFFED TYRES
1. Toe-in incorrect.
2. Tyres improperly infl ated.
3. Wheels or tyres out-of-true.
4. Front lower control arm soc ket/s worn.
5. Uneven cas ter and cam ber.
6. Lower front lower control arm/s or front lower control arm
rod/s bent.
7. Steering knuckle bent.
1. A dj ust toe-in. Refer to 2.2 WHEEL ALI G NMENT CHE CK ING
AND ADJUSTMENT in this Section.
2. I nflate tyres to specified press ure f or specifi c load
conditi ons. Refer t o the tyre placard at tached to t he vehi cle.
3. Chec k for wheel and tyre wobble. Check that the wheels
and tyres are correctly mounted. Bal ance wheels and
tyres. Ref e r t o S ection 10, WHEELS AND TYRES .
4. Replace worn components. Refer to 3.10 FRONT LOWER
CONTROL ARM in this Sect i on.
5. Chec k wheel alignment. Adjust as nec essary. Ref er to 2.2
WHEEL ALIGNMENT CHECKING AND ADJUSTMENT in this
Section.
6. Chec k alignment of front lower control arm/s and f ront lower
control arm rod/s .
Replace components as necessary. Refer to 3. 10 CONTROL
ARM and 3.14 FRONT LOWER CONTROL A RM ROD in thi s
Section.
7. Replace steeri ng knuckle. Refer to 3. 9 S T EERING KNUCK LE
in this Section.