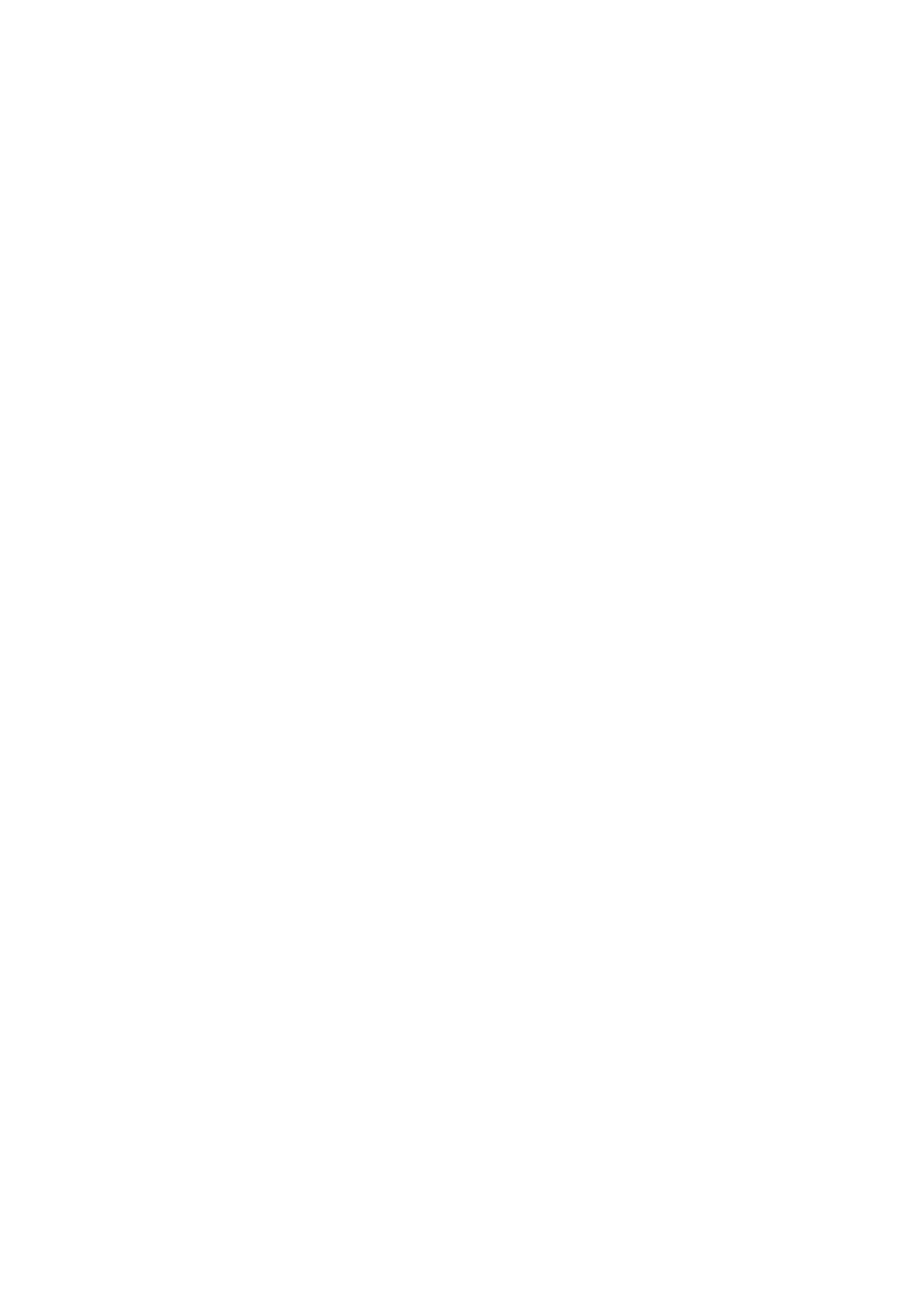
Engine Rear Cover Bolts................................................................................... 25
Engine Rocker Cover Bolts............................................................................... 12
Engine Service Lift Bracket M10 Bolts.............................................................. 50
Engine Service Lift Bracket M8 Bolt.................................................................. 25
Engine Valley Cover Bolts................................................................................. 25
" Ex haus t Man ifold Bo lts...........................Stage 1.............................................. 15
...............................................................Stage 2.............................................. 25
Exhaust Manifold Heat Shi eld Bo lt.................................................................... 9
! Flywheel/Flexplate Bolts (in Sequence) Stage 1.............................................. 20
Stage 2.............................................. 50
Stage 3.............................................. 100
" Fuel Rail Bolts................................................................................................... 10
" Ignition Coil-to-Bracket Bolts............................................................................. 12
" Ignition Coil Bracket-to-Valve Rocker Arm Cover Bolts.................................... 12
" Intake Manifold Bolts (in Sequence) ......Stage 1 ............................................. 5
Stage 2.............................................. 10
Knock Sensors.................................................................................................. 20
Oil Filter............................................................................................................. 30
Oil Filter Adaptor ............................................................................................... 55
Oil Level Indicator Tube Bolt............................................................................. 25
Oil Pan Blanking Sc re w Plug ............................................................................ 25
Oil Pan Baffle Bolts ........................................................................................... 12
Oil Pan Closeout Cover Bolt (Either Sid e) ........................................................ 10
Oil Pan Drain Plug............................................................................................. 25
" O il Pan Gal ler y Screw Plug............................................................................... 25
Oil Pan M8 Bolts (Oil Pan to Engine Block and to Front Cover)....................... 25
Oil Pan M6 Bolts (Oil Pan-to-Rear Cover)........................................................ 12
Oil Pan Transfer Cover Nut............................................................................... 12
Oil Pan Under-Tra y Bolt.................................................................................... 30
" Oil Pressure Sensor.......................................................................................... 20
Oil Pump-to-Eng ine Bloc k Bolts........................................................................ 25
Oil Pump Cover Bolts........................................................................................ 12
Oil Pump Relief Valve Plug............................................................................... 12
Oil Pump Pick-Up Tube to Oil Pump Screw...................................................... 12
Oil Transfer Cover Nuts .................................................................................... 12
" Oil Transfer Tube Bolts..................................................................................... 12
" Oil Transfer Tube Nuts...................................................................................... 12
" Oxygen Sensor ................................................................................................. 41
Positive Crankcase Ventilation (PCV) System Strap Nut................................. 12
Spark Plugs (New Cylinder Head - ‘Coining’)).................................................. 20
Spark Plugs....................................................................................................... 15
Starter Motor Bolt.............................................................................................. 48
Throttle Body Bolts............................................................................................ 12
Torque Converter Housing to Engine Block Bolts (Automatic Transmission) .. 50
" Torque Converter to Flexplate Attaching Bolts (Automatic Transmission)....... 65
Transmission Crossmember to Side Frame Bolts ............................................ 25
Transmission Support to Crossmember Nuts................................................... 60
Transmission Support to Transmission Extension Housing Bolts .................... 25
Valve Lifter Guide Bolts..................................................................................... 12
! Valve Rocker Arm Bolts.................................................................................... 30
Vapour Vent Pipe Bolts and Studs.................................................................... 12