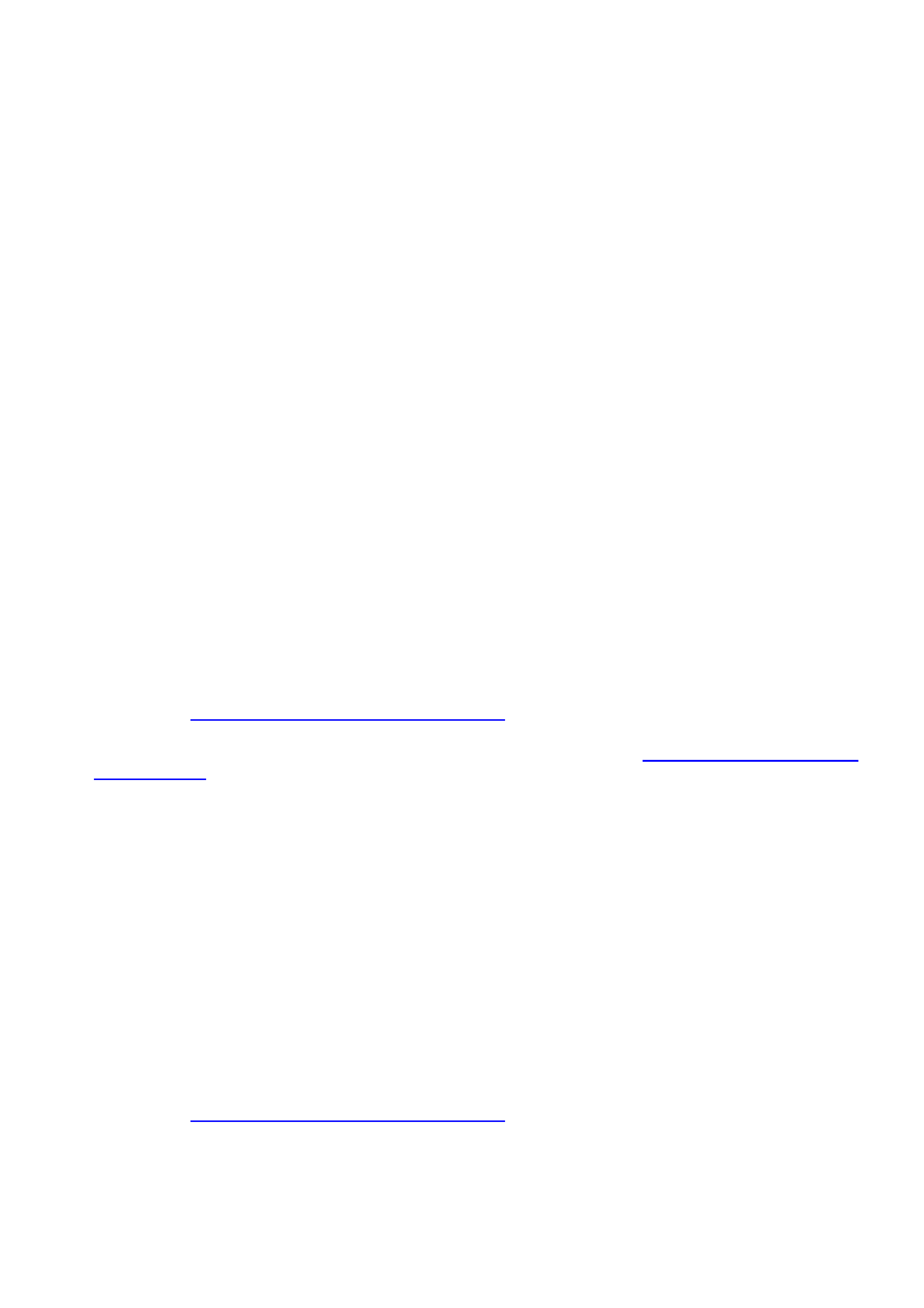
ENGINE COOLI NG FAN APPLICA TION
WH Series Models with standard V6 engines have two electric engine cooling fans. One fan operates at 'Low
Speed’; both operate at 'High Speed'. WH Models with GEN III V8 engine and V6 Supercharged are equipped with
two, two speed electric cooling fans.
The engine cooling fan assemblies provide the primary means of moving air through the engine radiator. These
fans are placed between the radiator and the engine and have their own shroud. There is no fan in front of the A/C
condenser.
The electric engine cooling fans are used to cool engine coolant flowing through the radiator.
On vehicles with V6 engines, the engine cooling fan motors have two terminals; one positive and one negative. The
positive terminals are permanently connected to battery voltage. When the negative terminal is pulled to earthed
through the low speed cooling fan relay, the low speed cooling fan will operate. When the negative terminal is pulled
to earth via the high speed cooling fan relay, both cooling fans will operate.
On vehicles with either V6 supercharged or GEN III V8 engines, the engine cooling fan motors have four terminals,
two negative and two positive terminals. The two positive terminals are permanently connected to battery voltage.
When one of the negative terminals is earthed, both cooling fan motors will operate at low speed. When both
negative terminals are earthed, both cooling fans will operate at high speed.
Regardless of the engine configuration, the low speed cooling fan operation is enabled when the low speed engine
cooling fan micro relay (located in the engine compartment relay housing, labelled Lo Fan) is energised by the Body
Control Module (BCM) via a request from the Powertrain Control Module (PCM). The PCM will request low speed
fan enable and disable via serial data communication to the BCM on circuit 1221 (Red/Black wire). After the PCM
requests a change in the state of the low speed relay (i.e. OFF to ON or ON to OFF), the BCM will send a serial
data response message back to the PCM confirming it received the message.
NOTE: On vehicles with GEN III V8 engines, serial data communication between the PCM and BCM is via the
Powertrain Interface Module (PIM).
The PCM determines when to enable the low speed fan relay based on inputs from the A/C request signal, Cooling
Temperature Sensor (CTS) and the Vehicle Speed Sensor (VSS).
Low speed fan operation
The low speed cooling fan relay will be turned ON when:
•Air conditioning request indicated (YES) and the vehicle speed is less than 30 km/h or
•Air conditioning pressure is greater than 1500 kPa or
•Coolant temperature is greater than 104°C (V6 and V6 supercharged) / 98°C (GEN III V8) or
•Vehicles with V6 and V6 supercharged engines; an engine coolant temperature sensor failure is detected by the
PCM, refer to Section 6C1 POWERTRAIN MANAGEMENT - V6 ENGINE for additional information.
Vehicles with GEN III V8 engines; when a coolant temperature sensor failure in conjunction with an Intake Air
Temperature (IAT) sensor failure is detected by the PCM, refer to Section 6C3 POWERTRAIN
MANAGEMENT - GEN III V8 ENGINE for additional information.
•When the ignition switch is turned from O N to O FF and the engine coolant temper ature is above 117°C (V6 and
V6 supercharged) / 113°C (GEN III V8) the BCM will continue to energise the low speed engine cooling fan
micro relay for four minutes
The PCM will request the BCM to switch off the low speed cooling fan relay when the following conditions have
been met:
•Air conditioning request not indicated (NO) and the coolant temperature is less than 99°C (V6 and V6
supercharged) / 95°C (GEN III V8) or
•Air conditioning reques t indicated (YES) with pressure les s than 1170 kPa, vehic le speed gr eater than 50 km /h
and coolant temperature less than 99°C (V6 and V6 supercharged engines) / 98°C (GEN III V8).
•NOTE: The low speed cooling fan has a minimum run on time of 30 seconds (GEN III V8 ONLY).
High speed fan operation
The high speed cooling fan relay will be turned ON if the low speed cooling fan relay has been energised for one
second and the following conditions have been met:
•Vehicles with V6 or V6 supercharged engines; if there is a BCM message response fault, setting a DTC 92 or
•Vehicles with V6 and V6 supercharged engines; an engine coolant temperature sensor failure is detected by the
PCM, refer to Section 6C1 POWERTRAIN MANAGEMENT - V6 ENGINE for additional information or
•Engine coolant temperature is above 107°C (V6), 111°C (V6 supercharged engines) 108°C (GEN III V8) or
•Air conditioning pressure is greater than 2000 kPa. (V6) 2600 kPa (V6 supercharged) 2400 kPa (GEN III V8).
NOTE: If the low speed cooling fan is off when the criteria for turning the high speed cooling fan on are first met, the
high speed cooling fan will turn on five seconds (V6 and V6 supercharged) one second (GEN III V8) after the low
speed cooling fan is switched on.
If both the high and low speed cooling fans are enabled, the PCM will turn the high speed cooling fan off when: