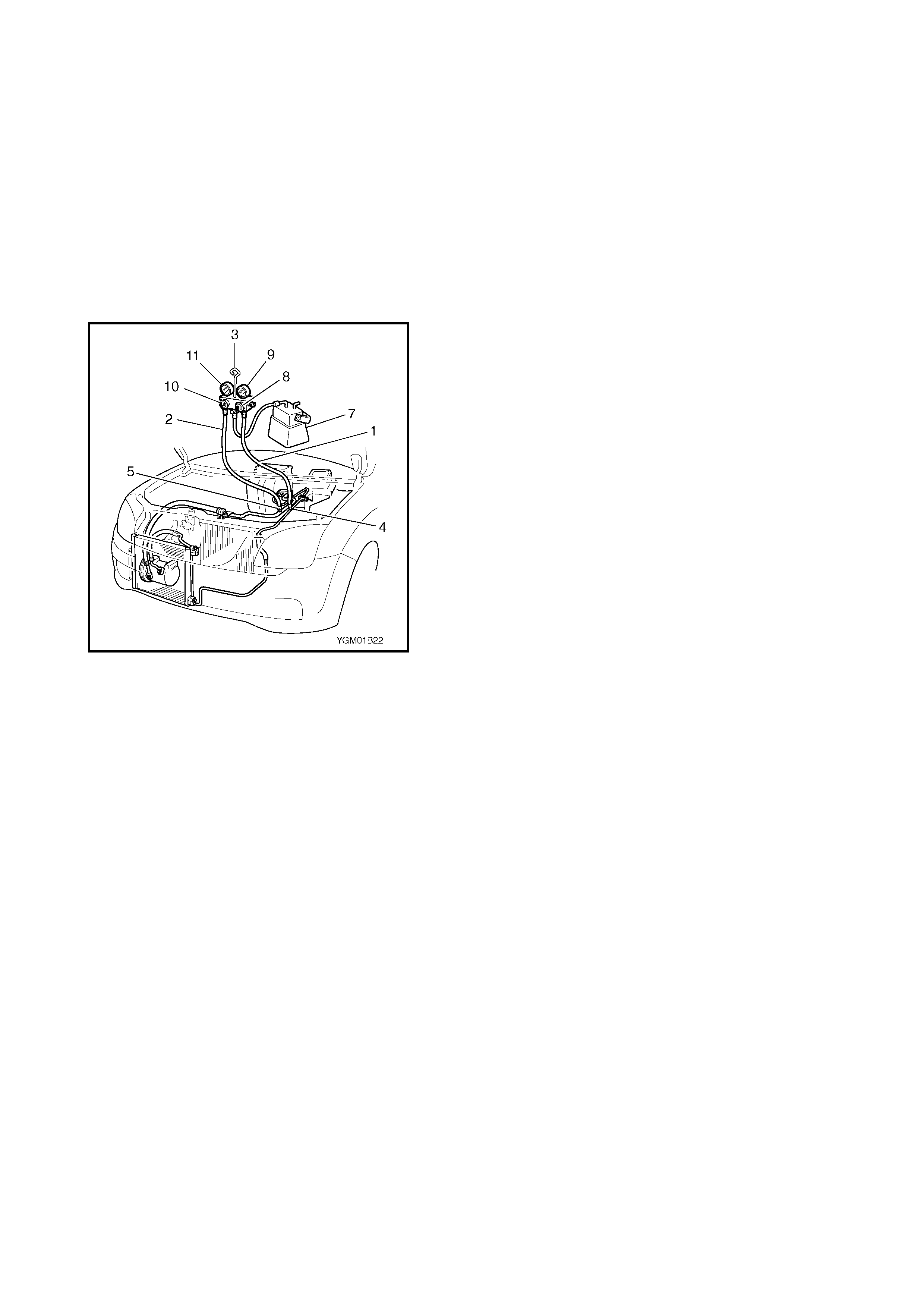
4.4 EVACUATING
EVACUATING PROCEDURE
CAUTION: Do not evacuate before recovering refriger-
ant in syst em.
NOTE: Whenever opened (exposed to atmospheric air),
the air conditioning sy stem must be e vac uated using a vac-
uum pump. A manifold gauge set should be connected to
the A/C system which should be evacuated for approxi-
mately 15 minutes.
1. Connect high pressure (HI) charging hose (1) and low
pressure (LO) c hargi ng hose (2) of the manifold gau ge
set (3) as follows:
High pressure charging hose (1) ® High pressure
charge port (4) on con denser outlet (liquid) tube.
Low pressure charging hose (2) ® Low pressure
charge port (5) on suction tube.
2. Attach centre charging hose (6) of manifold gauge set
(3) to vacuum pump (7).
3. Operate vacuum pump (7), and open the discharge
side valve (HI) (8) of the manifold gauge set (3).
If there is no blockage in the system, there will be an
indication on the high pressure gauge (9).
In this cas e, open the other side valve (LO) (10) of t he
set and evacu ate th e syste m.
4. After appro ximately 10 minutes the low pressure gauge
(11) should show a vacuum lower than –760 mmHg
providing no leakage exists.
NOTE:
•If the system does not show a vacuum below –760
mmHg, close both valves, stop the vacuum pump and
watch the movemen t of the low pressure gauge.
•Increas e in the gauge readi ng sugges ts existence of a
leak. In this case, repair the system before continuing
with the evacuation.
•If the gauge shows a stable reading (suggesting no
leakage), continue evacuation.
5. Evacuation should be carried out for a total of at least
15 minutes.
6. Continue evacuation until low pressure gauge (9)
indicates a vacuum less than –760 mmHg, and then
close both valves (8), (10).
7. Stop vacuum pump (7). Disconnect centre charging
hose (6) from pump inlet. Now, the system is ready for
charging refrigerant.
4.5 CHECKING SYSTEM FOR PRESSURE LEAKS
After completing the evacuation, close the manifold gauge
high pressure valve and low pressure valve and wait 10
minutes. Verify that low pressure gauge reading has not
changed.
CAUTION: If the gauge reading moves closer to “0”,
there is a leak somewhere. Inspect the tubing connec-
tions, make necessary repairs, evacuate the system
once again, ensuri ng there are no leaks.