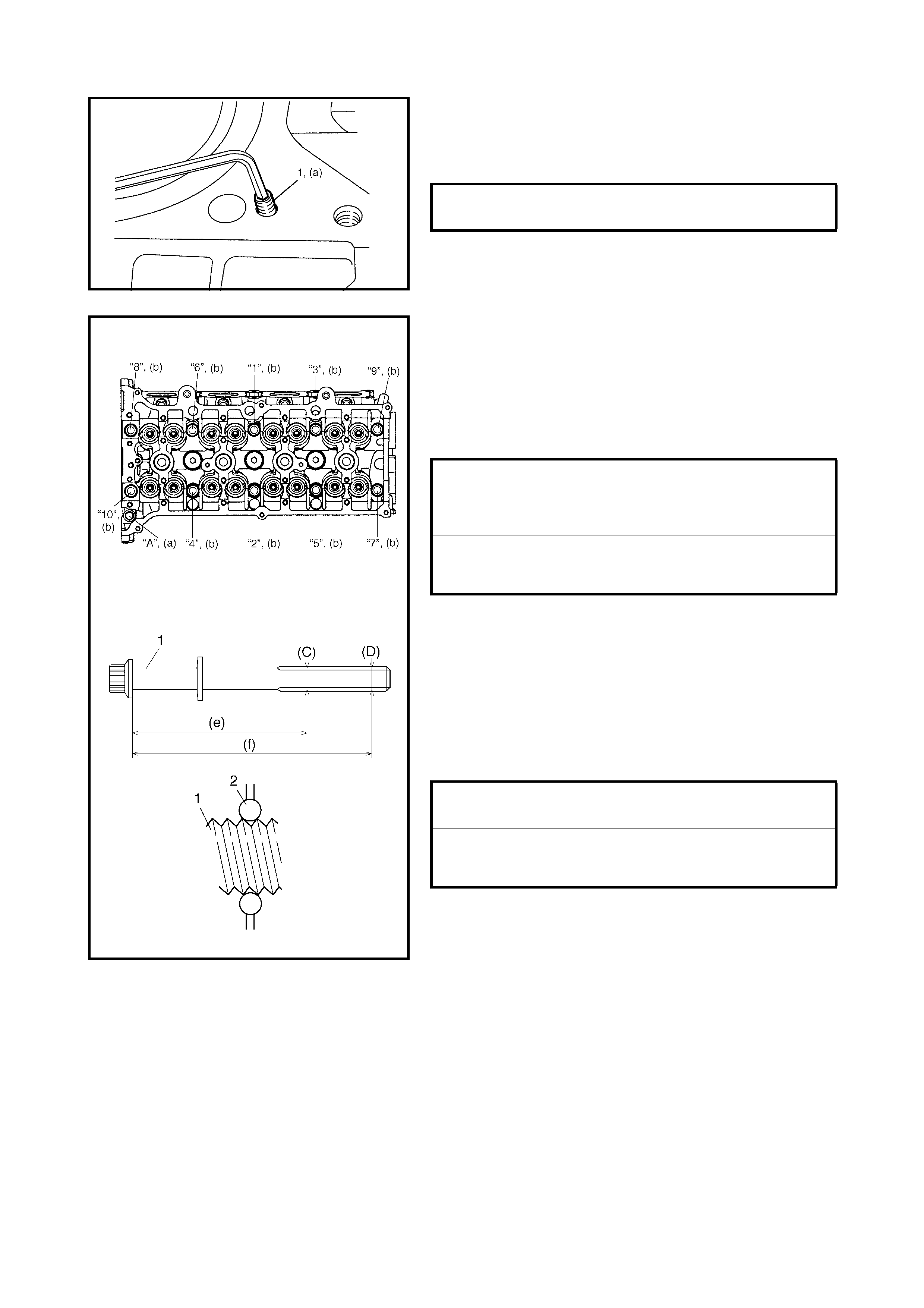
4. Make sure that the oil jet (venturi plug) (1) is installed
and that it is not clogged.
When installing the oil jet, be sure to tighten to
specified torque.
5. Install the cylinder head onto the cylinder block.
NOTE: If possible u se new cylinder head bolts. If they are
to be reused, check each bolt for thread deformation.
Measure the thread diameter of the cylinder head bolt (1) at
(C) and (D ) poin ts indicated i n the figure using a m icrome-
ter (2), an d calc ulate t he difference i n diame ters, (C) – ( D).
If it exceeds the limit, replace with new ones.
Apply engine oil to the cylinder head bolts and tighten them
gradually as follows.
a. Tighten the cylinder head bolts (“1” – “10”) to 20 Nm
following the numerical or der as shown, us ing a 12
corner socket wrench.
b. Repeat Step a, but tighten bolts to 40 Nm.
c. Turn all bolts 60° following the previous sequence.
d. Repeat Step c.
e. Tighten bolt “A” to specified torque.
6. Install the exhaust manifold stiffener, refer to 3.6
EXHAUST MANIFOLD INST ALLATION in this Section.
7. Install the camshafts, refer to 4.5 CAMSHAFT,
TAPPET AND SH IM INSTALL AT IO N in this Section.
8. Install the timing chain, refer to 4.4 TIMING CHAIN
AND CHAIN TENSIONER INSTALLATION in this
Section.
9. Install the timing chain cover, refer to 4.2 TIMING
CHAIN COVER in this Section.
10. Install the cylinder head cover, refer to 3.4 CYLINDER
HEAD COVER INSTALLATION in this Section.
11. Install the oil pan, refer to 3.7 OIL PAN AND OIL PUMP
STRAINER INSTALLATION in this Section.
12. Install the intake manifold stiffener and connect all
hoses, refer to 3.5 THROTTLE BODY AND INTAKE
MANIFOLD INSTALLATION in this Section.
13. Refer to 4.2, TIMING CHAIN COVER INSTALLATION
in this Section and perform Steps 3 to 7.
VENTURI PLUG (a)
TORQUE SPECIFICATION 5 Nm
CYLINDER HEAD BOLT DIAMETER
MEASUREMENTS POINTS (e)
(f) 83.5 mm
115 mm
CYLINDER HEAD BOLT DIAMETER
DIFFERENCE (DEFORMATION) LIMIT
(C) – (D) 0.1 mm
CYLINDER HEAD BOLT - M8 (a)
TORQUE SPECIFICATION 22 Nm
CYLINDER HEAD BOLTS - M10 (b)
TORQUE SPECIFICATION
20 Nm THEN
40 Nm THEN
TURN 60° TWICE