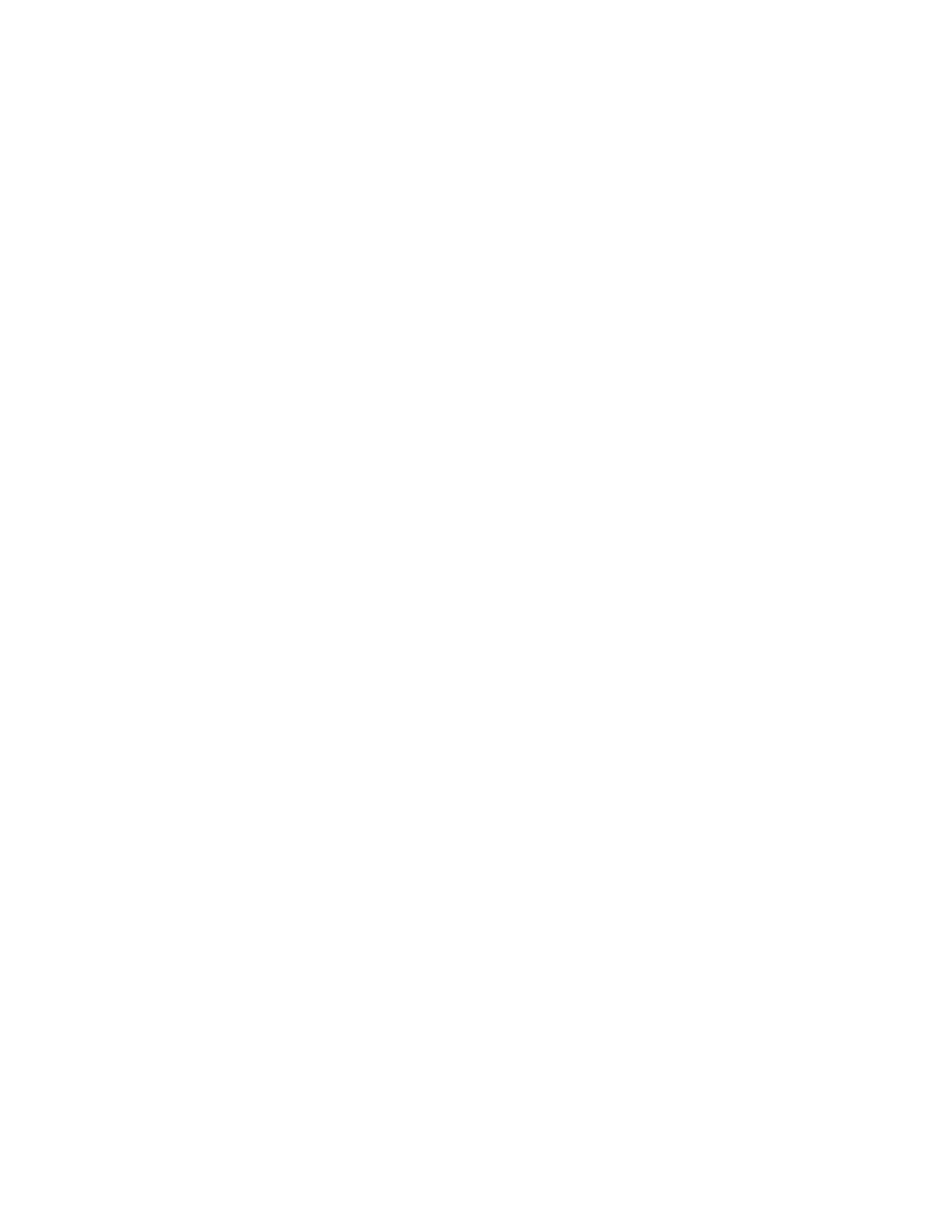
HOLDEN SERVICE TECHLINE ________________________________________________________________ APRIL 1999
The following information is an excerpt from VT
Service Manual, Volume 14A, to be released
shortly.
1. GENERAL INFORMATION
The engine cooling system on VT Series II Models with V6
engine carries over from VT Series Models, noting the
following:
As a running change, approximately March 1999, two
single speed electric engine cooling fans were introduced
to vehicles with V6 engine; a low speed fan and a high
speed fan (as compared to; two, two speed electric cooling
fans).
As information about these new engine cooling fans has
not been published before, this Section has been compiled
to cover their introduction.
For information, including General Information, Service
Operations, Specifications and Torque Wrench
Specifications, that is not covered in this Section, refer to
Section 6B1-1 ENGINE COOLING - V6 ENGINE in Volume
2 of this Service Manual.
NOTE: The cooling system for vehicles with V6
supercharged engines does not change for VT Series II
Models.
1.1 COOLING FAN OPERATION
On VT Series II Models with V6 engines, the engine
cooling fan motors have two terminals; one positive and
one negative. The positive terminals are permanently
connected to battery voltage. When the negative terminal
is connected to earth through the low speed cooling fan
relay, the low speed cooling fan will operate. When the
negative terminal is connected to earth via the high speed
cooling fan relay, both cooling fans will operate.
The low speed cooling fan operation is enabled when the
low speed engine cooling fan micro relay (located in the
engine compartment relay housing, labelled Lo Fan) is
energised by the Body Control Module (BCM) via a request
from the Powertrain Control Module (PCM). The PCM will
request low speed fan enable and disable via serial data
communication to the BCM on circuit 1221 (Red/Black
wire). After the PCM requests a change in the state of the
low speed relay (i.e. OFF to ON or ON to OFF), the BCM
will send a serial data response message back to the PCM
confirming it received the message.
The PCM determines when to enable the low speed fan
relay based on inputs from the A/C request signal, Engine
Coolant Temperature (ECT) sensor and the Vehicle Speed
Sensor (VSS).
LOW SPEED FAN OPERATION
The low speed cooling fan relay will be turned ON when:
•Air conditioning request indicated (YES) and the
vehicle speed is less than 30 km/h or
•Air conditioning pressure is greater than 1500 kPa or
•Coolant temperature is greater than 104°C or
•An engine coolant temperature sensor failure is
detected by the PCM, refer to Section 6C1
POWERTRAIN MANAGEMENT - V6 ENGINE for
additional information.
•When the ignition switch is turned from ON to OFF
and the engine coolant temperature is above 117°C.
The BCM will continue to energise the low speed
engine cooling fan micro relay for approximately four
minutes.
The PCM will request the BCM to switch off the low speed
cooling fan relay when the following conditions have been
met:
•Air conditioning request not indicated (NO) and the
coolant temperature is less than 99°C or
•Air conditioning request indicated (YES) with pressure
less than 1170 kPa, vehicle speed greater than 50
km/h and coolant temperature less than 99°C.
HIGH SPEED OPERATION
The PCM determines when to enable the high speed fan
relay based on inputs from the ECT sensor. The high
speed cooling fan relay will be turned ON if the low speed
cooling fan relay has been energised for one second and
the following conditions have been met:
•If there is a BCM message response fault, setting a
DTC 92 or
•An engine coolant temperature sensor failure is
detected by the PCM, refer to Section 6C1
POWERTRAIN MANAGEMENT - V6 ENGINE for
additional information or
•Engine coolant temperature is above 107°C or
•Air conditioning pressure is greater than 2000 kPa.
NOTE: If the low speed cooling fan is off when the criteria
for turning the high speed cooling fan on are first met, the
high speed cooling fan will turn on 5 seconds after the low
speed cooling fan is switched on.
If both the high and low speed cooling fans are enabled,
the PCM will turn the high speed cooling fan off when:
•The engine coolant temperature is less than 103°C
and
•Air conditioning request is not indicated (No) or
•Air conditioning request is indicated (Yes) and the
pressure is less than 1500 kPa.
2. SERVICE OPERATIONS
Service Operations for the cooling system on vehicles with
V6 engine carry over from those detailed in Section 6B1-1
ENGINE COOLING - V6 ENGINE in Volume 2 of this
Service Manual, noting the following.
To accommodate the new engine cooling fans, a minor
revision to the lower baffle air chute was made, however,
this revision does not effect the way the air chute attaches
to the front of the vehicle.
If reinstalling a cooling fan, cooling fan motor or shroud
assembly to a VT Series II vehicle with a V6 engine, refer to
4. TORQUE WRENCH SPECIFICATIONS in this Section
for the correct torque wrench specifications.