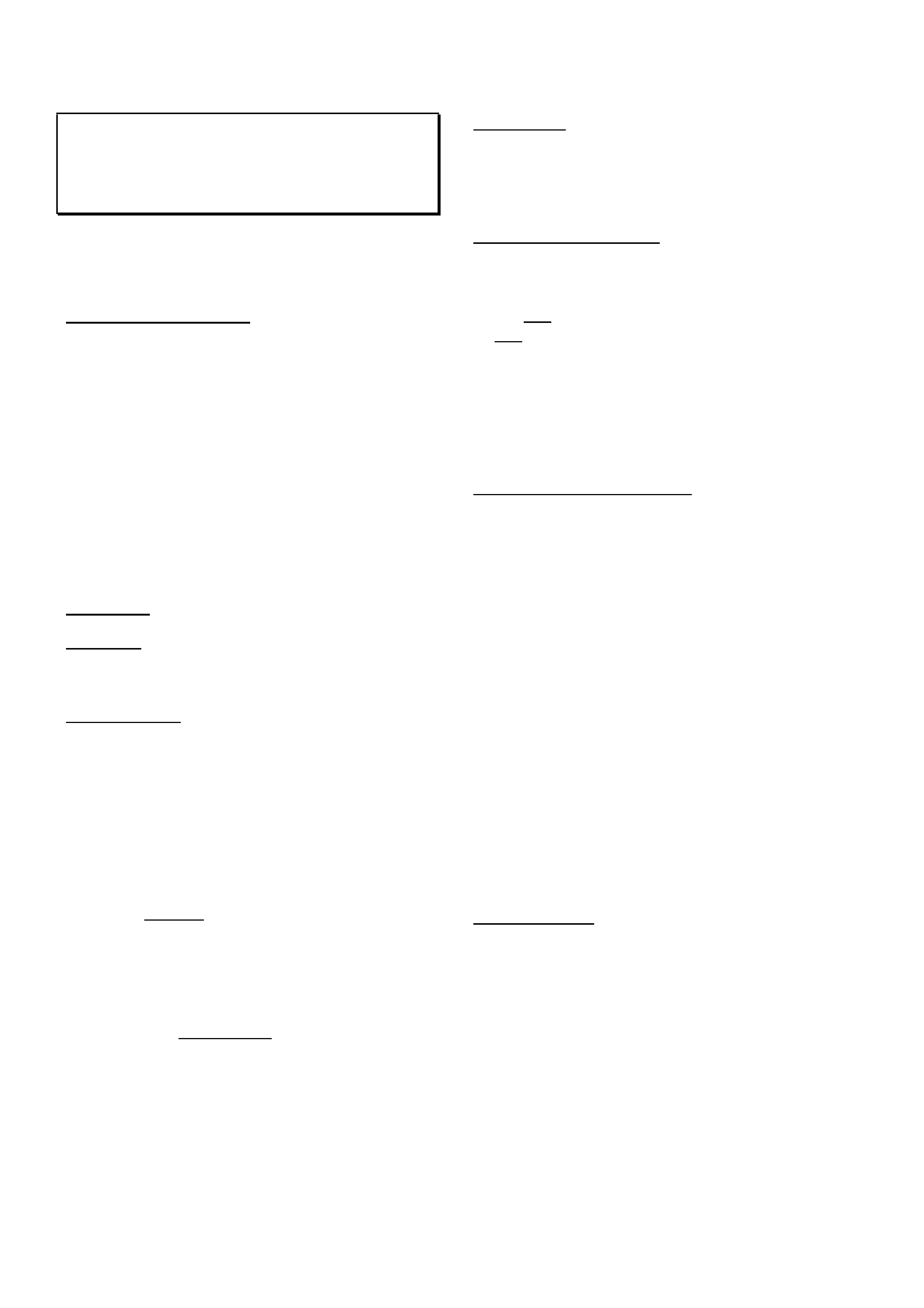
HOLDEN SERVICE TECHLINE ____________________________________________________________ AUGUST 2001
3
BREAKPOINT INFORMATION
ALL
(GROUP OB) TL108-OB01
This Techline provides some insight into
breakpoint numbers, their format and how they
are established.
CURRENT CONDITION
Breakpoints are often provided in Techline
Bulletins for several reasons:
- to identify upgraded or revised vehicle
components;
- to identify whether a specific condition or
complaint (or rework) is, or can be, carried out
on a specific vehicle;
- so that if a certain condition is encountered,
technicians can report the condition via a PIR
IE: if a vehicle is post (after) or pre (before) the
breakpoint – important for gauging whether
further work on a particular condition is
required.
FORMATS
ISOVIN’s:
Where possible, ISOVIN numbers and build
dates are provided.
TAG Numbers:
Tag numbers are quoted – as many Holden
systems (EG: the One Line Warranty claim
system your warranty clerk uses) utilise the Tag
number – and it has always been an easy
vehicle definer within Holden and Holden
dealerships. A complication caused by using
the Tag number is: while locally manufactured
vehicles’ Tag numbers are the last seven digits
of their ISOVIN, imported vehicles’ Tag
numbers are not. Imported vehicles have a
Holden assigned Tag number plate attached at
Port of Entry (POE). This plate provides the
model and Tag number – used for warranty
claiming, and wherever the Tag number is
required. This is required because the
ISOVIN’s are international numbers and each
one is unique – however – the last seven digits
can repeat – within a vehicle model, and each
year of the model! Using these numbers would
create much confusion because of the repeated
seven digit numbers that dealerships would
have on vehicles.
This confusion will eventually be removed (in
the future) when all systems requiring vehicle
identification move to ISOVIN only.
Build Dates:
Sometimes it is only possible to provide a build
date, as revisions to vehicle build or actual
parts introduction are carried out on a specific
date, but an ISOVIN is not recorded.
Engine/Trans. Numbers:
At times, a revision to an engine or a
transmission is carried out and because the
prime revision has taken place in those parts.
Also - any of these engines/trans’ may be fitted
to any vehicle – so the engine or transmission
number is quoted as the breakpoint. In these
cases, the known ISOVIN for the engine
number quoted is also provided – but this is a
“rough guide” or “for reference” ONLY – as
vehicles may be built with “lower” ISOVIN’s and
a post-breakpoint engine number.
Breakpoint Summary Pages:
This section in each Techline carries “TAG”
numbers only, mainly for space reasons.
Where a Tag number is quoted, the vehicle
model it applies to is also provided.
Where these are “L” numbers – locally
manufactured vehicles - in many cases the
number is ‘universal’ for locally built vehicles;
EG: today this would cover VX, VU, WH; where
the component mentioned is used in all the
models, and only “V,W” will be quoted in
‘Model’ area.
Where only ISOVIN numbers are known for
imported vehicles, the last 8 digits are shown
alongside the model – this is not exact, but
allows technicians the best chance to define
whether a vehicle is pre or post breakpoint of a
change. This situation occurs as the
breakpointed vehicle may not be imported to
Australia and thus a Tag number is not
assigned to it.
Export vehicles:
Holden exports vehicles to various overseas
markets and, at times you may see an ISOVIN
number that is unusual – EG: Starts with “6G1.”
but ends in a familiar seven digit “L” tag
number. The Tag numbers (only) of these
ISOVIN’s should be used as breakpoint
numbers, as the vehicles are built on-line with
Australian vehicles.