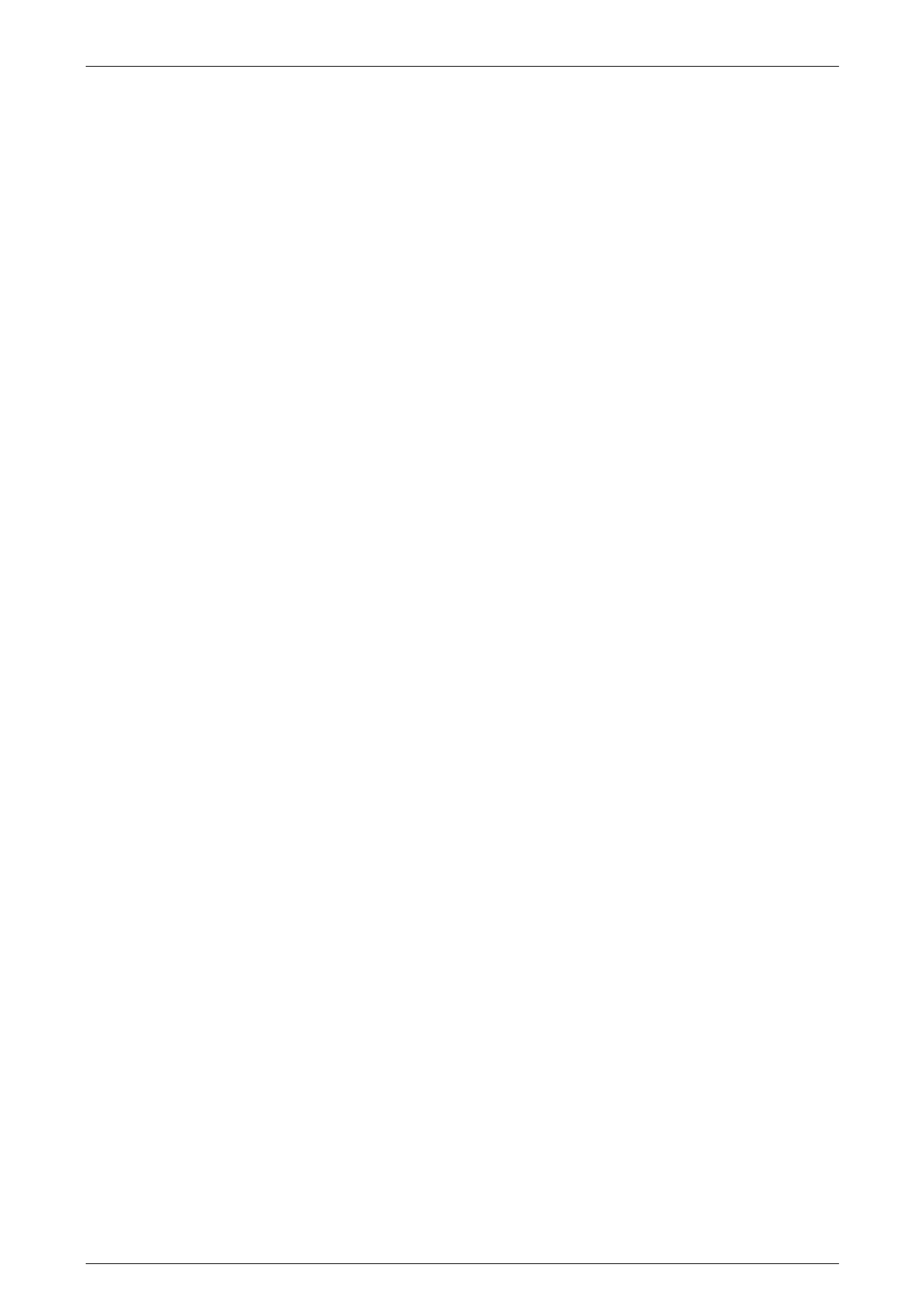
Engine Cooling – V6 Engine Page 6B1–2
3.3 Draining and Filling Cooling System ................................................................................................................. 39
Draining ................................................................................................................................................................ 39
Filling.................................................................................................................................................................... 39
3.4 Cleaning Cooling System.................................................................................................................................... 42
Cooling System Reverse Flush .......................................................................................................................... 42
Radiator............................................................................................................................................................ 42
Engine.............................................................................................................................................................. 43
Heater Hoses and Core.................................................................................................................................... 44
3.5 Drive Belt Tension ............................................................................................................................................... 45
Inspect .................................................................................................................................................................. 46
3.6 Coolant Hoses...................................................................................................................................................... 47
3.7 Pressure Testing.................................................................................................................................................. 49
MY2006 VZ Models............................................................................................................................................... 49
Coolant Filler Cap Pressure Testing................................................................................................................. 49
Cooling System Pressure Testing.................................................................................................................... 51
MY2006 VZ Update Models.................................................................................................................................. 52
Coolant Filler Cap Pressure Testing................................................................................................................. 52
Cooling System Pressure Testing.................................................................................................................... 53
3.8 Thermostat ........................................................................................................................................................... 55
Remove................................................................................................................................................................. 55
Test ....................................................................................................................................................................... 58
Dismantle.............................................................................................................................................................. 58
Reassembly.......................................................................................................................................................... 59
Reinstall................................................................................................................................................................ 59
3.9 Coolant Recovery Reservoir............................................................................................................................... 61
Remove................................................................................................................................................................. 61
Inspect .................................................................................................................................................................. 61
Install .................................................................................................................................................................... 62
3.10 Air Baffle and Chutes .......................................................................................................................................... 63
Remove................................................................................................................................................................. 63
Standard Air Baffle Configuration – Vi ew ‘C’.................................................................................................... 63
Calais / S / SV6 Vehicles – View ‘D’................................................................................................................. 64
AWD Vehicles (Wagon and Crew Cab) – View ‘E’........................................................................................... 64
Cross 6 Vehicles – View ‘F’.............................................................................................................................. 64
Install .................................................................................................................................................................... 64
3.11 Coolant Pump....................................................................................................................................................... 65
Remove................................................................................................................................................................. 65
Inspect .................................................................................................................................................................. 71
Reinstall................................................................................................................................................................ 71
3.12 Coolant Outlet Housing....................................................................................................................................... 73
MY2006 VZ Models............................................................................................................................................... 73
Remove............................................................................................................................................................ 73
Reinstall ........................................................................................................................................................... 74
MY2006 VZ Update Models.................................................................................................................................. 75
Remove............................................................................................................................................................ 75
Reinstall ........................................................................................................................................................... 76
3.13 Coolant Inlet Pipe................................................................................................................................................. 77
Remove................................................................................................................................................................. 77
Reinstall................................................................................................................................................................ 78
3.14 Cooling Fan and Shroud Assembly ................................................................................................................... 80
Remove................................................................................................................................................................. 80
Install .................................................................................................................................................................... 82
Disassemble......................................................................................................................................................... 83
Reassemble.......................................................................................................................................................... 83
3.15 Flexible Transmission Cooler Hose ................................................................................................................... 84
Replace................................................................................................................................................................. 84
3.16 Radiator ................................................................................................................................................................ 86
Remove................................................................................................................................................................. 86
Reinstall................................................................................................................................................................ 88
Page 6B1–2