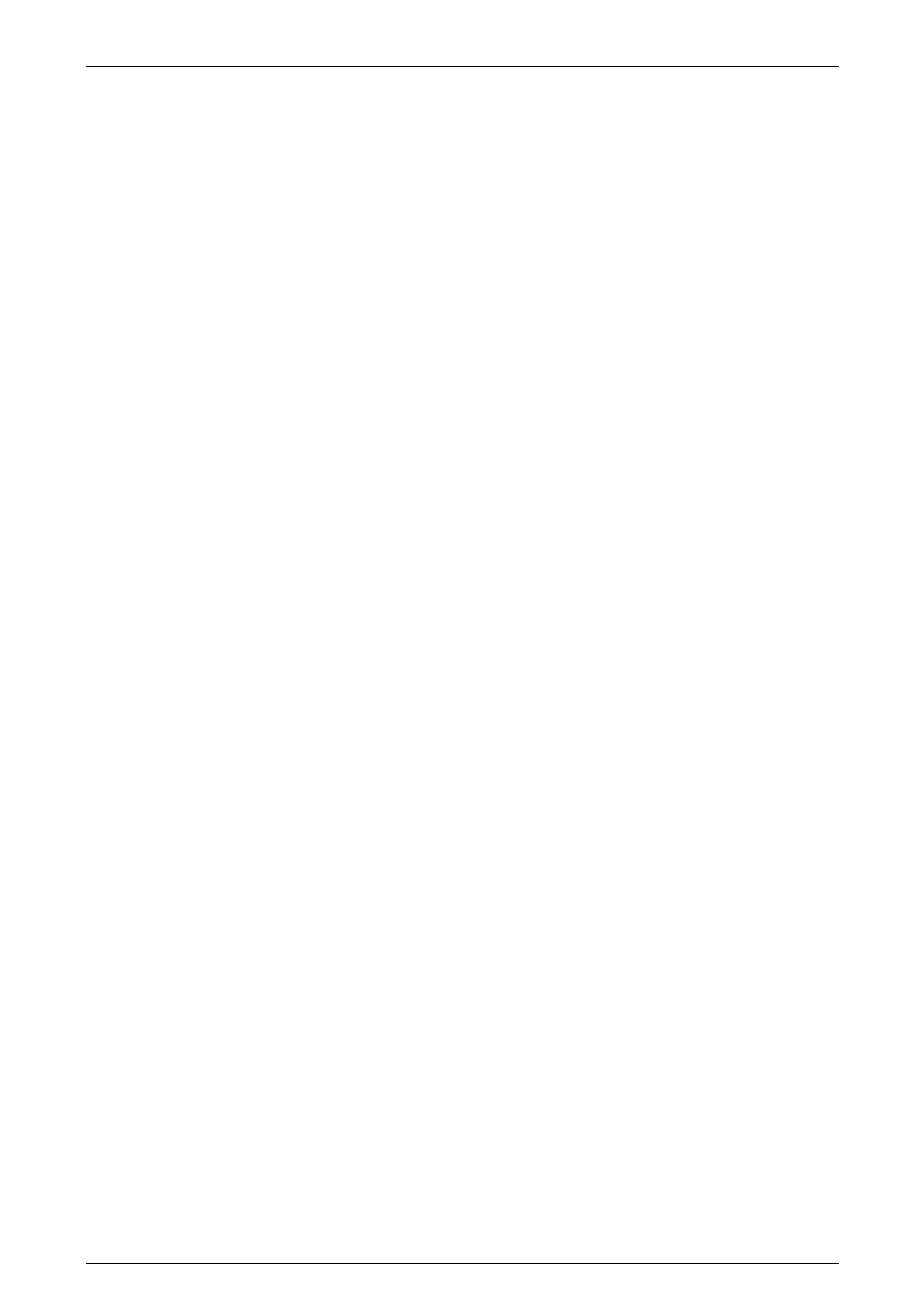
Powertrain Interface Module – GEN III V8 Page 6E3–4
Page 6E3–4
8.8 DTC B1019 – Configuration Mismatch............................................................................................................... 40
DTC Description................................................................................................................................................... 40
Circuit Description............................................................................................................................................... 40
Additional Information......................................................................................................................................... 40
Conditions for Running the DTC........................................................................................................................ 40
Conditions for Setting the DTC........................................................................................................................... 40
Action Taken when the DTC Sets....................................................................................................................... 40
Condition for Clearing the DTC .......................................................................................................................... 40
Test Description................................................................................................................................................... 40
DTC B1019 Diagnostic Table .............................................................................................................................. 41
8.9 DTC B3027 – Starter Enable Circuit Range / Performance............................................................................... 42
DTC Description................................................................................................................................................... 42
Circuit Description............................................................................................................................................... 42
Additional Information......................................................................................................................................... 42
Conditions for Running the DTC........................................................................................................................ 42
Condition for Setting the DTC............................................................................................................................. 42
Action Taken when the DTC Sets....................................................................................................................... 42
Condition for Clearing the DTC .......................................................................................................................... 42
Test Description................................................................................................................................................... 42
DTC B3027 Diagnostic Table .............................................................................................................................. 43
8.10 DTC P1554 – Cruise Control Cancel Circuit Malfunction ................................................................................. 44
DTC Description................................................................................................................................................... 44
Circuit Description............................................................................................................................................... 44
Additional Information......................................................................................................................................... 44
Conditions for Running the DTC........................................................................................................................ 44
Condition for Setting the DTC............................................................................................................................. 44
Action Taken when the DTC Sets....................................................................................................................... 44
Condition for Clearing the DTC .......................................................................................................................... 44
Test Description................................................................................................................................................... 44
DTC P1554 Diagnostic Table............................................................................................................................... 45
8.11 DTC P1585 – Cruise Control Enable Circuit Malfunction ................................................................................. 46
DTC Description................................................................................................................................................... 46
Circuit Description............................................................................................................................................... 46
Additional Information......................................................................................................................................... 46
Conditions for Running the DTC........................................................................................................................ 46
Condition for Setting the DTC............................................................................................................................. 46
Action Taken when the DTC Sets....................................................................................................................... 46
Condition for Clearing the DTC .......................................................................................................................... 46
Test Description................................................................................................................................................... 46
DTC P1585 Diagnostic Table............................................................................................................................... 47
9 Service Operations...............................................................................................................................48
9.1 Safety and Precautionary Measures .................................................................................................................. 48
9.2 Powertrain Interface Module............................................................................................................................... 49
Remove................................................................................................................................................................. 49
Reinstall................................................................................................................................................................ 50
10 PIM Security and Programming................................................................................................... .......51
10.1 Security and Programming Information ............................................................................................................ 51
Vehicle Security Card.......................................................................................................................................... 51
10.2 PIM Configuration................................................................................................................................................ 52
Configuring a New PIM........................................................................................................................................ 52
Changing Existing PIM Variant Configuration................................................................................................... 52
Programming the VIN.......................................................................................................................................... 53
10.3 BCM Link to PCM / PIM........................................................................................................................................ 54
11 Special Tools ........................................................................................................................................55