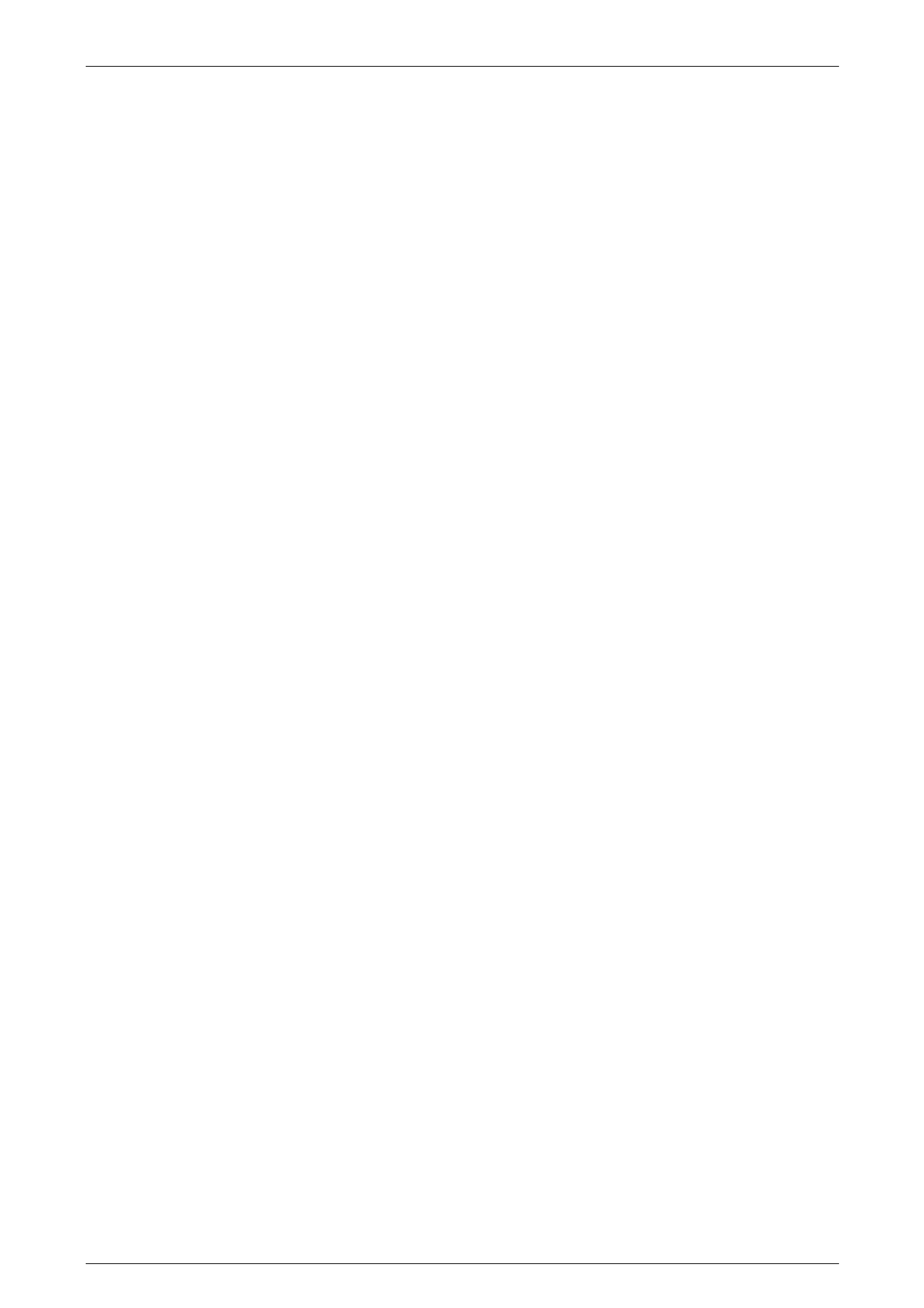
Fuel System Page 8A1–3
Page 8A1–3
Tool No. AU533 .................................................................................................................................................... 83
Remove............................................................................................................................................................ 83
Reinstall ........................................................................................................................................................... 85
Tool Nos. 7370 and 7371 ..................................................................................................................................... 86
Remove............................................................................................................................................................ 86
Reinstall ........................................................................................................................................................... 86
6.2 Fuel Tank Siphon Procedure .............................................................................................................................. 87
6.3 Fuel Tank.............................................................................................................................................................. 90
Remove................................................................................................................................................................. 90
Reinstall................................................................................................................................................................ 97
6.4 Fuel Filler Neck Assembly .................................................................................................................................. 98
6.5 Modular Fuel Pump and Sender Assembly ....................................................................................................... 99
Remove................................................................................................................................................................. 99
Test ..................................................................................................................................................................... 101
Disassemble....................................................................................................................................................... 102
Reassemble........................................................................................................................................................ 106
Reinstall.............................................................................................................................................................. 106
6.6 Fuel Level Sender Assembly ............................................................................................................................ 108
6.7 Suction Filter...................................................................................................................................................... 109
Remove............................................................................................................................................................... 109
Reinstall.............................................................................................................................................................. 109
6.8 Modular Fuel Pump............................................................................................................................................ 110
Remove............................................................................................................................................................... 110
Reinstall.............................................................................................................................................................. 111
6.9 Fuel Filter Assembly.......................................................................................................................................... 112
6.10 Pressure Regulator............................................................................................................................................ 113
Remove............................................................................................................................................................... 113
Reinstall.............................................................................................................................................................. 114
6.11 Modular Fuel Pump and Sender Assembly O-rings........................................................................................ 115
6.12 Fuel Tank Pressure Sensor............................................................................................................................... 116
Remove............................................................................................................................................................... 116
Reinstall.............................................................................................................................................................. 116
6.13 Fuel Fill Limiter Vent Valve Assembly ............................................................................................................. 117
Remove............................................................................................................................................................... 117
Reinstall.............................................................................................................................................................. 117
6.14 Fuel Filler Cap.................................................................................................................................................... 118
Remove............................................................................................................................................................... 118
Reinstall.............................................................................................................................................................. 118
6.15 Fuel Pipes........................................................................................................................................................... 119
Remove............................................................................................................................................................... 119
Reinstall.............................................................................................................................................................. 121
7 Service Operations — Regular Cab and Crew Cab, and Crew Cab with 'Delete Tub' Option....123
7.1 Quick-connect Fittings...................................................................................................................................... 123
Quick-connect Fittings (Metal Collar) .............................................................................................................. 123
Remove.......................................................................................................................................................... 123
Reinstall ......................................................................................................................................................... 124
Quick-connect Fittings (Plastic Collar)............................................................................................................ 126
Remove.......................................................................................................................................................... 126
Reinstall ......................................................................................................................................................... 127
Tool No. AU533 .................................................................................................................................................. 128
Remove.......................................................................................................................................................... 128
Reinstall ......................................................................................................................................................... 130
Tool Nos. 7370 and 7371 ................................................................................................................................... 131
Remove.......................................................................................................................................................... 131
Reinstall ......................................................................................................................................................... 131
7.2 Fuel Tank............................................................................................................................................................ 132
Regular Cab and Crew Cab with 'Delete Tub' Option ..................................................................................... 132
Remove.......................................................................................................................................................... 132