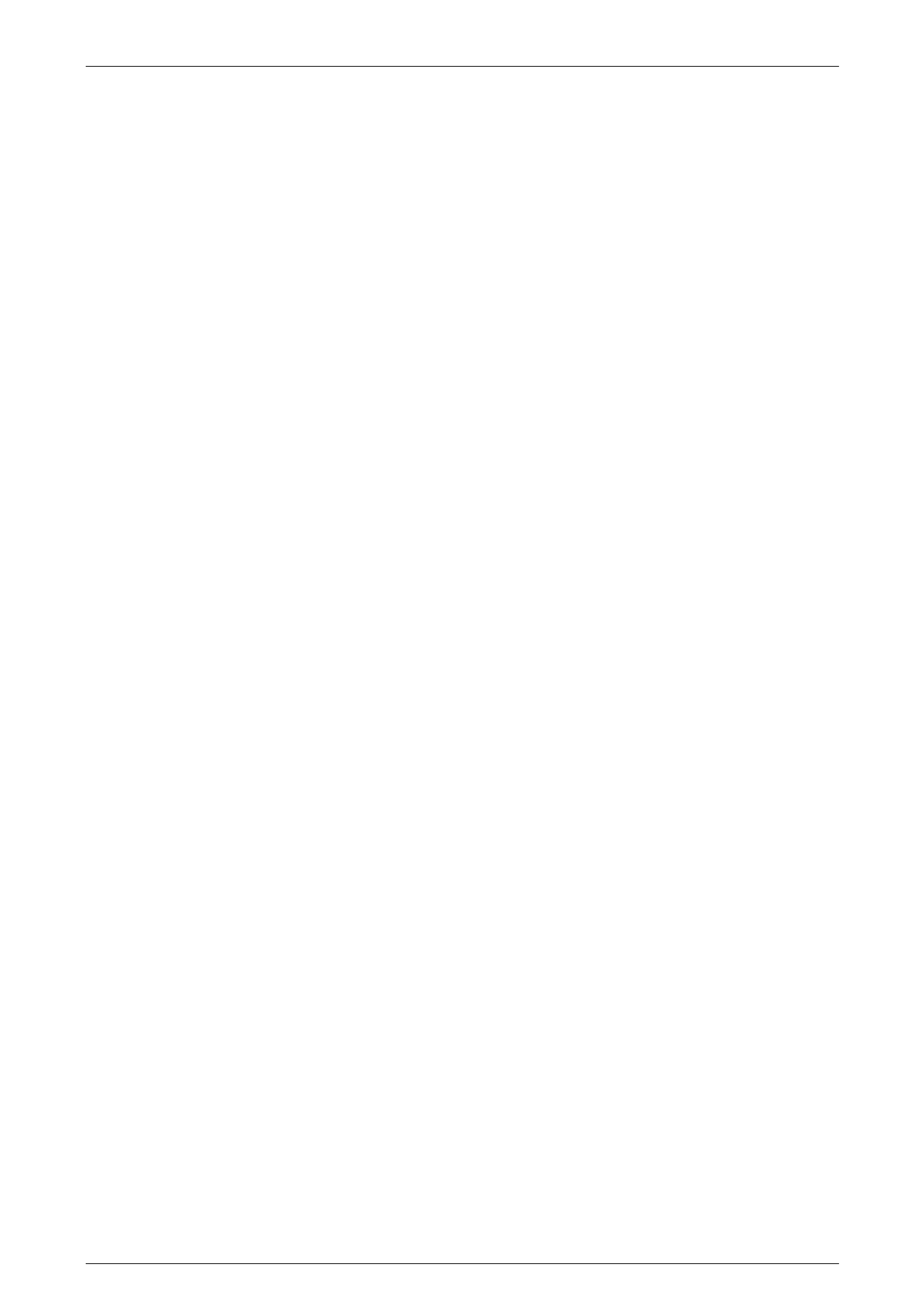
Engine Mechanical – V6 Page 6A1–6
Page 6A1–6
3.20 Camshaft ............................................................................................................................................................ 170
Remove............................................................................................................................................................... 170
Right-hand Side.............................................................................................................................................. 170
Left-hand Side................................................................................................................................................ 171
Clean................................................................................................................................................................... 173
Inspect ................................................................................................................................................................ 173
Camshaft Visual Inspection............................................................................................................................ 173
Camshaft Measurement................................................................................................................................. 173
Reinstall.............................................................................................................................................................. 176
Right-hand Side.............................................................................................................................................. 176
Left-hand Side (Bank 2) ................................................................................................................................. 178
3.21 Rocker Arm......................................................................................................................................................... 182
Remove............................................................................................................................................................... 182
Clean and Inspect.............................................................................................................................................. 182
Reinstall.............................................................................................................................................................. 183
3.22 Stationary Hydraulic Lash Adjuster ................................................................................................................. 184
Remove............................................................................................................................................................... 184
Clean and Inspect.............................................................................................................................................. 184
Reinstall.............................................................................................................................................................. 185
3.23 Cylinder Head Assembly................................................................................................................................... 186
Remove............................................................................................................................................................... 186
Right-hand Side (Bank 1) Cylinder Head ....................................................................................................... 186
Left-hand Side (Bank 2) Cylinder Head.......................................................................................................... 187
Disassemble....................................................................................................................................................... 188
Clean................................................................................................................................................................... 191
Inspect ................................................................................................................................................................ 191
Visual Inspection............................................................................................................................................ 191
Cylinder Head Measurement.......................................................................................................................... 192
Valve Spring Inspection and Measurement.................................................................................................... 194
Valve and Seat Grinding ................................................................................................................................ 194
Assemble............................................................................................................................................................ 199
Reinstall.............................................................................................................................................................. 202
Right-hand Side (Bank 1) Cylinder Head ....................................................................................................... 202
Left-hand Side (Bank 2) Cylinder Head.......................................................................................................... 204
3.24 Engine Mounts and Brackets............................................................................................................................ 206
Remove............................................................................................................................................................... 206
Inspect ................................................................................................................................................................ 207
Reinstall.............................................................................................................................................................. 207
4 Major Service Operations..................................................................................................................208
4.1 Engine Assembly............................................................................................................................................... 209
Remove............................................................................................................................................................... 209
Disassemble....................................................................................................................................................... 215
Reassemble........................................................................................................................................................ 216
Reinstall.............................................................................................................................................................. 216
4.2 Oil Pan and Oil Pump Suction Pipe Assembly................................................................................................ 217
Remove............................................................................................................................................................... 217
Disassemble....................................................................................................................................................... 217
Clean................................................................................................................................................................... 218
Inspect ................................................................................................................................................................ 218
Reassemble........................................................................................................................................................ 219
Reinstall.............................................................................................................................................................. 220
4.3 Flexplate Assembly ........................................................................................................................................... 221
Remove............................................................................................................................................................... 221
Clean................................................................................................................................................................... 222
Inspect ................................................................................................................................................................ 222
Reinstall.............................................................................................................................................................. 223