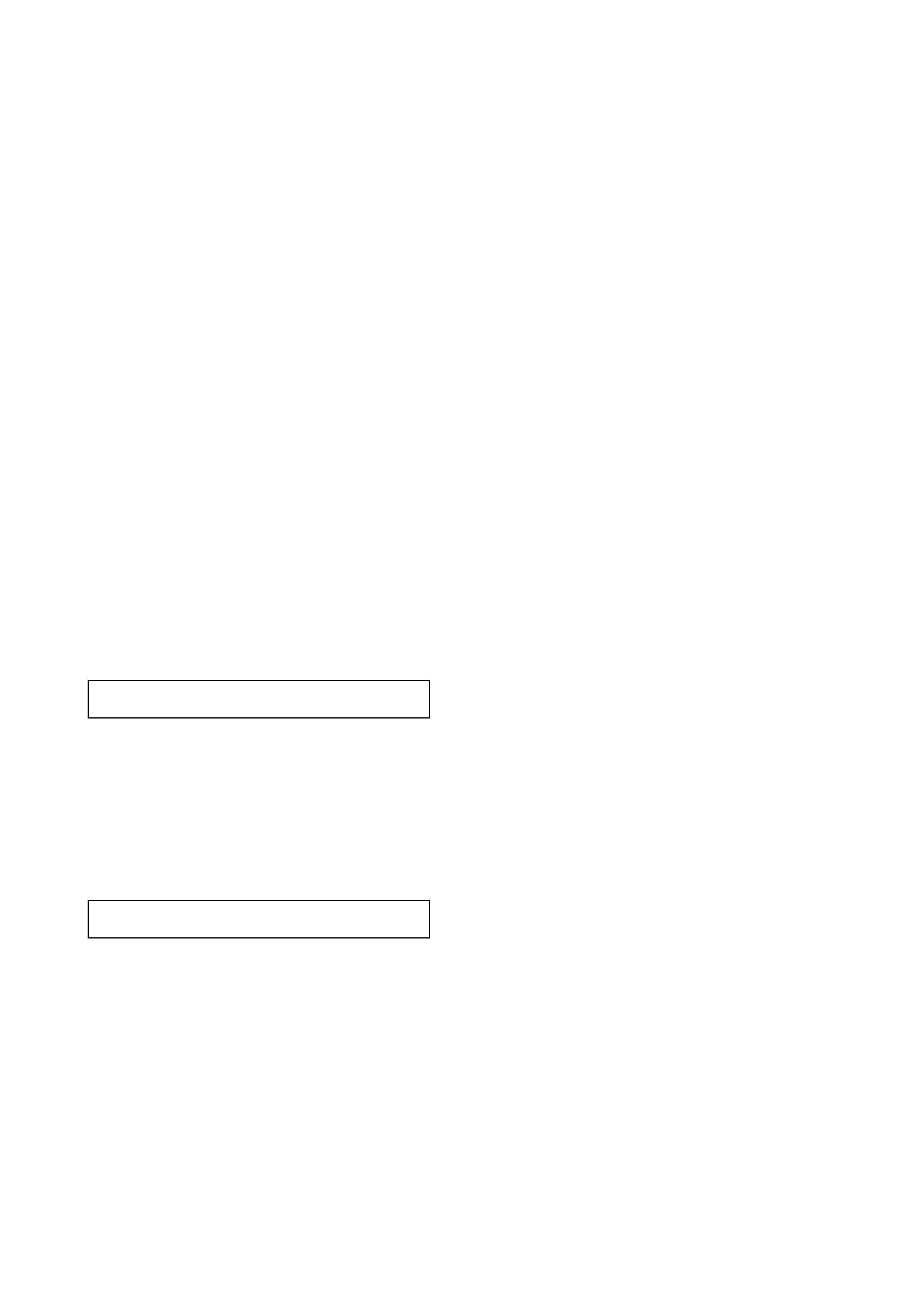
2. SERVICE OPERATIONS
The differential oil must be changed at 1500 km and then at 45,000 km intervals. Use synthetic hypoid gear oil to
HN2040 such as 'Mobilube SHC 80W-140 ID'.
The viscous coupling cartridge assembly is a sealed unit and must be replaced as a complete assembly if required.
General service operations are the same as those described in the Holden VT Series Service Information CD, refer
SECTION 4B - FINAL DRIVE AND DRIVE SHAFTS, however, to determine if the Hydratrak coupling cartridge is
faulty, undertake the following torque check. The Hydratrak rear axle assembly is covered by the current Axle
Warranty Changeover agreement between GMHAL and Spicer Axle Australia (refer GMHA Dealer Bulletins).
TORQUE CHECK
i. Place transmission in neutral with engine turned 'OFF'.
ii. Jack up one rear wheel, then release park brake lever to fully 'OFF' position. Support vehicle body on a safety
stand.
iii. Remove centre cap (alloy wheels).
iv. Mark relationship of road wheel to axle flange. Remove road wheel attaching nuts and remove wheel.
v. Remove caliper attaching bolts and remove caliper from mounting, refer Section 5 BRAKES in the Holden VT
Series Service Information CD. Support caliper on a wire hook. Remove brake disc.
CAUTION:
DO NOT ALLOW CALIPER TO HANG BY BRAKE HOSE.
vi. Using a torque wrench in conjunction with adaptor, Tool No. 4A48, and torque wrench adaptor E6662B, rotate
axle shaft in forward direction. If the unit is operating satisfactorily, a torque reading of 35 Nm should be
obtained whilst turning the axle shaft at 20 rpm (e.g. one third of a turn per second).
If a torque reading of less than 25 Nm or more than 80 Nm (@ 20 rpm) is obtained, remove differential case
and inspect the differential components and repair or replace as necessary.
However, if the Hydratrak Coupling cartridge unit is faulty it will require replacement with a new Coupling unit,
as it is a sealed, non-serviceable fluid filled component.
CAUTION:
DO NOT ATTEMPT TO REPAIR OR WELD THE COUPLING UNIT.
vii. Install brake disc and caliper. Tighten caliper attaching bolts to the correct torque specification.
CALIPER ATTACHING BOLT
TORQUE SPECIFICATION 55 - 70
Nm
viii. Install road wheel.
NOTE:
When installing the wheel, align the marks made prior to removal.
ix. Remove safety stand and lower vehicle.
x. Tighten road wheel attaching nuts to the correct torque specification.
ROAD WHEEL ATTACHING NUT
TORQUE SPECIFICATION 110-140
Nm
xi. Refit wheel cover/centre cap.