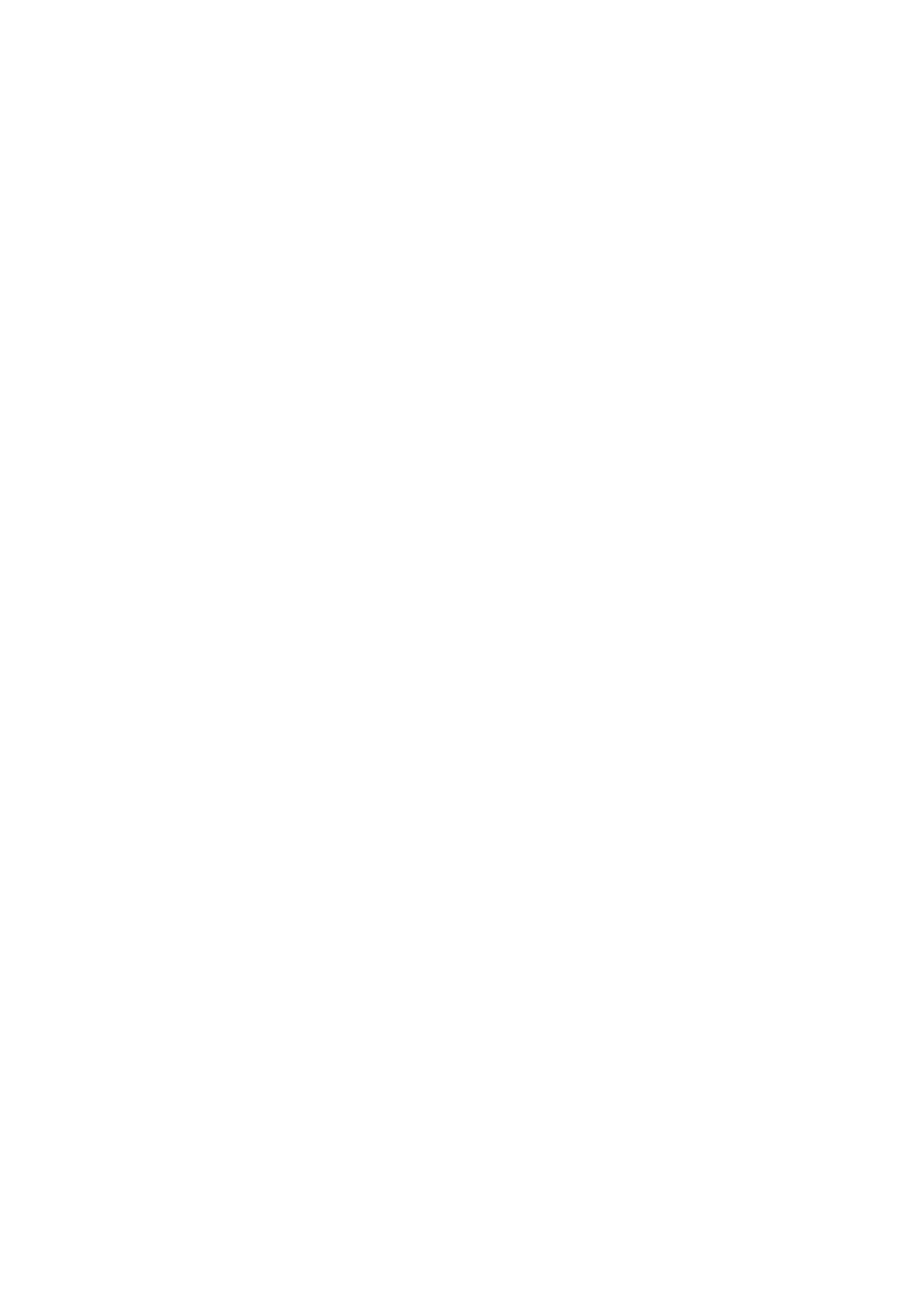
1. PLATE, TRANSMISSION ADAPTER
2. PLUG
3. PIN, DOWEL
4. PIN, DOWEL
5. BUSHING, SHIFT RAIL
6. SEAL, INPUT SHAFT
7. SHIM, INPUT SHAFT
8. RACE, INPUT SHAFT BEARING
9. BEARING, INPUT SHAFT TAPERED
10. SHAFT, INPUT
11. RACE, INPUT SHAFT BEARING
12. RING, 4H GEAR BLOCKER
13. RING, SNAP
14. SYNCHRONIZER ASSEMBLY 3RD/4TH
15. SPRING, 3RD/4TH SYNCHRONIZER
16. KEY, 3RD/4TH SYNCHRONIZER
17. HUB, 3RD/4TH SYNCHRONIZER
18. SLEEVE, 3RD/4TH SYNCHRONIZER
19. RING, 3RD GEAR BLOCKER
20. GEAR, 3RD SPEED
21. BEARING, 3RD GEAR NEEDLE
22. BEARING, MAINSHAFT SMALL
TAPERED
23. MAINSHAFT
24. BEARING, 2ND GEAR NEEDLE
25. GEAR, 2ND SPEED
26. WASHER, THRUST
27. CONE, INNER
28. CONE, FRICTION
29. RING, 2ND GEAR BLOCKER
30. SYNCHRONIZER ASSEMBLY, 1ST/2ND
31. SPRING, 1ST/2ND SYNCHRONIZER
32. KEY, 1ST/2ND SYNCHRONIZER
33. HUB, 1ST/2ND SYNCHRONIZER
34. SLEEVE, 1ST/2ND SYNCHRONIZER
35. RING, 1ST GEAR BLOCKER
36. CONE, FRICTION
37. CONE, INNER
38. WASHER, THRUST
39. RING, SNAP
40. BEARING, 1ST GEAR NEEDLE
41. GEAR, 1ST SPEED
42. BEARING, MAINSHAFT LARGE
TAPERED
43. RACE, MAINSHAFT BEARING
44. CASE, TRANSMISSION
45. BOLT, SHIFT LEVER GUIDE
46. BOLT, SHIFT LEVER GUIDE
47. BOLT, SHIFT DETENT COVER
48. COVER, SHIFT DETENT
49. BUSHING, SHIFT RAIL
50. PIN, FRONT OFFSET LEVER ROLL
51. LEVER, FRONT OFFSET
52. SPRING, SHIFT DETENT
53. BALL, SHIFT DETENT
54. BOLT, SHIFT GUIDEPLATE
55. PLATE, SHIFT GUIDE
56. DETENT ASSEMBLY, SHIFT
57. MAGNET
67. RETAINER, REVERSE
SYNCHRONIZER KEY
68. WASHER, THRUST
69. RING, SNAP
70. RING, REVERSE GEAR BLOCKER
71. WASHER, WAVE
72. BEARING, REVERSE GEAR
NEEDLE
73. GEAR, REVERSE]
74. WASHER, THRUST
75. RING, SNAP
76. SPACER
77. BEARING, REAR MAINSHAFT
78. SPACER
79. RING, SNAP
80. RING, SNAP
81. GEAR, SPEEDOMETER
(ELECTRONIC)
82. RING, SNAP
83. SPACER
84. RING, SNAP
85. RACE, MAINSHAFT BEARING
86. HOUSING, TRANSMISSION
EXTENSION
87. SENSOR, ELECTRONIC SPEED
88. BOLT, SPEED SENSOR
89. SOLENOID, REVERSE LOCKOUT
90. BOLT, REVERSE LOCKOUT
ASSEMBLY
91. BODY ASSEMBLY, REVERSE
LOCKOUT
92. BUSHING, SHIFT RAIL
93. LEVER, REAR OFFSET SHIFT
94. PIN, REAR OFFSET SHIFT LEVER
ROLL
95. CUP, ISOLATOR
96. SHIFTER ASSEMBLY
97. BOLT, SHIFTER ASSEMBLY
98. BOOT, SHIFTER
99. SEAL AND BOOT, REAR OUTPUT
100. BOLT, TRANSMISSION
EXTENSION HOUSING
101. PLUG, DRAIN
102. SHIM, COUNTERSHAFT
103. RACE, COUNTERSHAFT
TAPERED
104. BEARING, COUNTERSHAFT
TAPERED
105. COUNTERSHAFT
106. BEARING, COUNTERSHAFT
TAPERED
107. RACE, COUNTERSHAFT
BEARING
108. WASHER, THRUST
109. GEAR, 6TH DRIVE
110. BEARING, 6TH GEAR NEEDLE
111. FORK, REVERSE SHIFT
112. PAD, REVERSE SHIFT FORK
113. RING, SNAP
114. RING, 6TH GEAR BLOCKER
115. SPACER
116. RING, SNAP
126.GEAR, 5TH DRIVE
127.BEARING, 5TH GEAR NEEDLE
128.EXTENSION, COUNTERSHAFT
129.BEARING, COUNTERSHAFT
EXTENSION TAPERED
130.RACE, COUNTERSHAFT
EXTENSION BEARING
131.SHIM, COUNTERSHAFT
EXTENSION
132.FUNNEL, OIL
133.BOLT, REVERSE IDLER SHAFT
BRACKET
134.BRACKET, REVERSE IDLER
SHAFT
135.WASHER, REVERSE IDLER GEAR
THRUST
136.GEAR, REVERSE IDLER
137.BEARING, REVERSE IDLER GEAR
ROLLER
138.SHAFT, REVERSE IDLER GEAR
139.WASHER, REVERSE IDLER GEAR
THRUST
140.RAIL ASSEMBLY, 5TH/6TH SHIFT
141.PIN, ROLLER
142.COLLAR
143.RAIL, SHIFT
144.LEVER, 5TH/6TH SHIFT RAIL
145.PAD, 5TH/6TH SHIFT RAIL LEVER
146.BUSHING, 5TH/6TH SHIFT RAIL
LEVER
147.PIN, ROLL
148.LEVER, REVERSE SHIFT RAIL
149.RAIL ASSEMBLY, 1ST/2ND 3RD/4TH
SHIFT
150.FORK, 1ST/2ND SHIFT
151.PAD, 1ST/2ND SHIFT FORK
152.LINK, SHIFT
153.RAIL ASSEMBLY, 1ST/2ND 3RD/4TH
SHIFT
154.PIN, ROLL
155.PIN, SELECTOR
156.PLATE, INTERLOCK
157.LINK, SHIFT
158.FORK, 3RD/4TH SHIFT
159.PAD, 3RD/4TH SHIFT FORK
160.O-RING, REVERSE LOCKOUT
ASSEMBLY
161.TUBE, VENT
162.HOUSING, CLUTCH ADAPTER
163.BOLT, CLUTCH ADAPTER
HOUSING
164.FORK, CLUTCH
165.T-HANDLE, CLUTCH FORK PIVOT
166.BOLT, CLUTCH FORK PIVOT
167.HOUSING, CLUTCH ACTUATOR
ADAPTER
168.BOLT, CLUTCH ACTUATOR
ADAPTER HOUSING
169.RING, SNAP
170.PLUNGER, REVERSE LOCKOUT
171.SPRING, REVERSE LOCKOUT
OUTER
172.COLLAR, REVERSE LOCKOUT