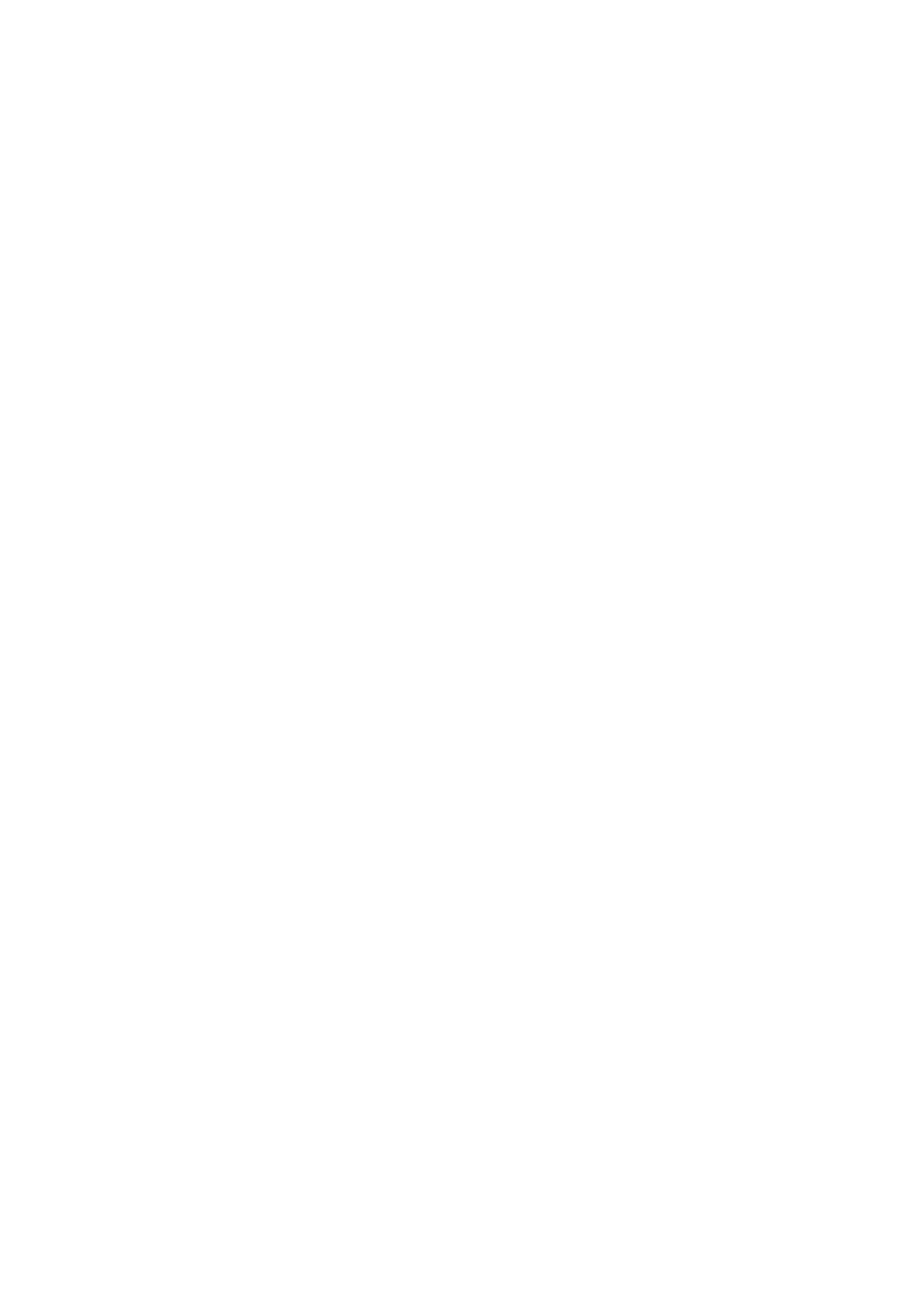
4.5 INTERMITTENT FAILURES
As with most electronic systems, intermittent failures may be difficult to accurately diagnose. The following is a
method to try to isolate an intermittent failure, especially wheel speed circuit failures.
If the control module detects an ABS fault, the ABS warning lamp will illuminate during the ignition cycle in which the
fault was detected and a Diagnostic Trouble Code (DTC) will be logged in memory of the control module.
If an ETC fault occurs, either the TRAC OFF and /or ABS warning lamp will illuminate, if the fault is specific to the
ETC system, both the TRAC OFF and the ABS warning lamps will illuminate, if the fault is common to both systems.
If an intermittent problem occurs, the TRAC OFF and/or ABS warning lamp will go out (if the fault corrects itself)
after the ignition has been cycled off and on. Also stored in the control module memory, will be the history data of
the DTC at the time the fault occurred. This history data includes the number of Ignition Cycles since the DTC
occurred, if the Ignition Cycle is zero, then the DTC is Current, if the Ignition Cycles is greater than zero, then the
DTC is a history DTC. TECH 2 can be used to read ABS or ABS/ETC data;
1. If a system fault has been detected, record all current trouble codes and trouble code history information. Also,
if available, record any specific driving condition during which the problem or failure occurs. This information
can help in duplicating the condition.
2. Clear any trouble codes that are stored in the control module memory, refer 'CLEARING DTC's' in this Section.
3. Using the TECH 2 in Snapshot Mode while test-driving the vehicle, try to duplicate the condition in which the
problem or fault occurs. Refer to 4.7 TECH 2 Diagnostics in this Section for additional information on the use of
TECH 2.
NOTE:
IN CERTAIN DIAGNOSTIC MODES, THE ANTI-LOCK BRAKING SYSTEM IS DISABLED WHILE TECH 2 IS
COMMUNICATING WITH THE ABS OR ABS/ETC CONTROL MODULE.
If an intermittent condition is still undetected, or not related to the wheel speed circuitry, go to the appropriate
Diagnostic Trouble Code (DTC) or symptom chart in this Section. Follow through the Chart while moving or wiggling
the associated ABS or ABS/ETC wiring harnesses and connectors, and at the same time looking for intermittent
type failures in the circuitry.
Most intermittent problems are caused by faulty electrical connections or wiring. When an intermittent failure is
encountered, check suspect circuits for:
a. Poor mating of connector body halves or terminals not fully seated in the connector body (backed out).
b. Improperly formed or damaged terminals. If damaged, carefully reform terminals in a suspected circuit.
c. Poor terminal to wire connection. This requires removing the terminal from the connector body to inspect (refer
to Section 12P WIRING DIAGRAMS).
Also, due to the sensitivity of ABS or ABS/ETC components to Electro-Magnetic Interference (EMI), the following
checks should be performed if an intermittent malfunction is suspected:
a. Check for proper installation of wiring harnesses resulting from add-on options such as a C.B. radio or cellular
telephone etc.
b. Visually inspect wheel speed sensors and pulse rings for looseness, damage, foreign material accumulation
and proper mounting. Replace damaged components, remove any foreign material and/or properly attach all
components.
c. Check for proper routing of front wheel speed sensor wiring near spark plug leads. Refer to Section 6D1-3
(V6) or Section 6D2-3 (V8) for spark plug lead routing.
d. Measure resistance of spark plug leads (refer to Section 6D1-3 (V6) or Section 6D2-3 (V8) for details).
Replace any leads if not to specification.
e. While test driving vehicle, monitor wheel speeds using TECH 2. If any wheel speed drops or displays erratic
speed, refer to the appropriate wheel speed DTC chart in this Section.
If detected, ABS failures will disable the anti-lock brake function of an entire ignition cycle, even if the condition
clears itself before the ignition is switched off. However, the clearing of low voltage failure conditions during an
ignition cycle will allow ABS operation to resume.
If an ETC failure is detected, both the anti-lock braking and traction control functions will be disabled for an entire
ignition cycle, even if the condition clears itself before the ignition is switched off. However, the clearing of low
voltage failure conditions during an ignition cycle will allow ABS and ETC operation to resume.