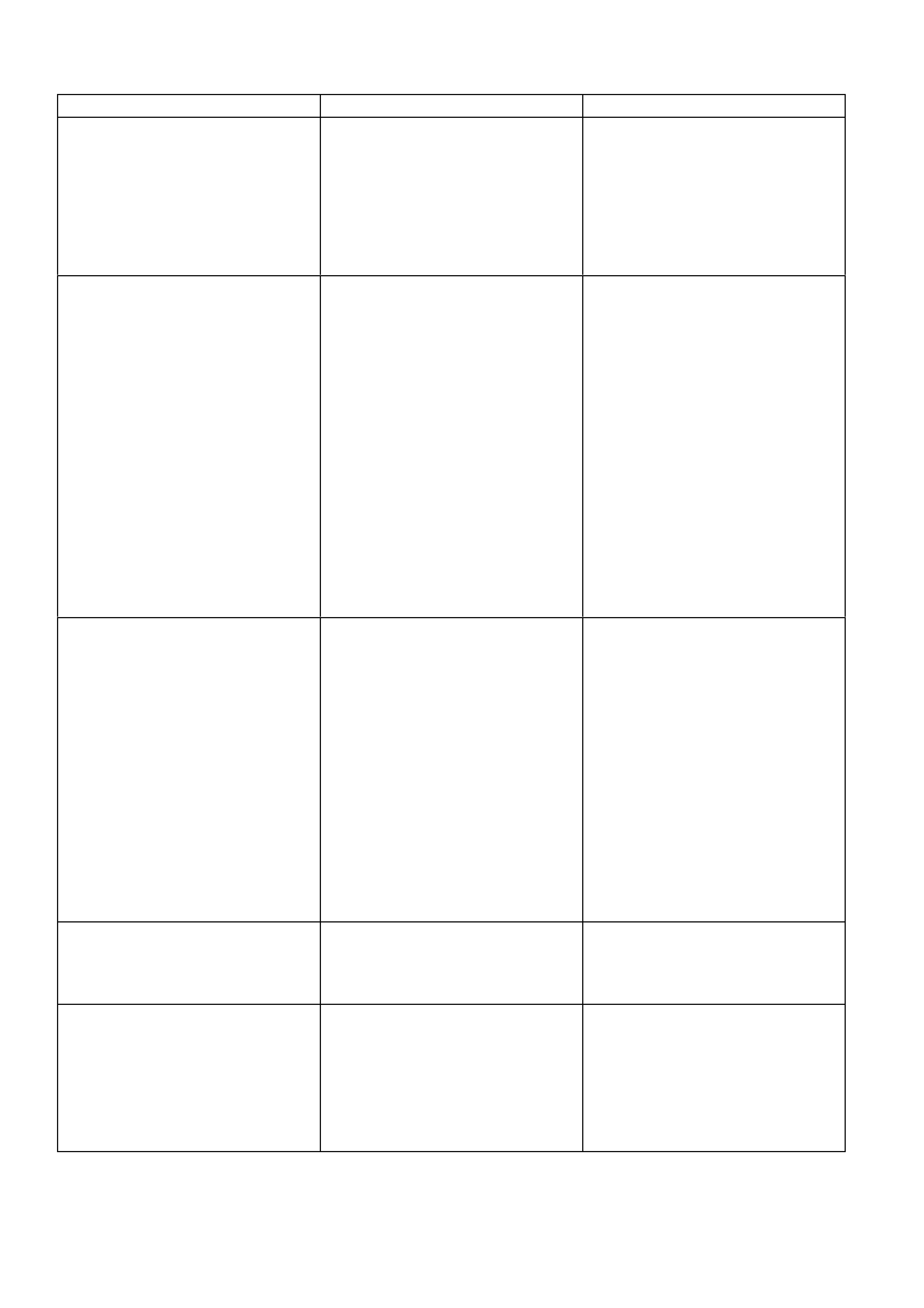
4. DIAGNOSIS
CONDITION PROBABLE CAUSE CORRECTIVE ACTION
SLlPPING Worn or oil-soaked lining.
Driven plate sticking on transmission
input shaft splines.
Weak or broken diaphragm spring
Master or slave cylinder defective
Replace driven plate, correct oil leak.
Clean splines and appl
10%
mol
bdenum disulphide
rease to
Holden’s Specification HN 1271.
Replace pressure plate assembl
.
Refer Operation 3.8 Clutch and
Pressure Plates, in this Section.
Overhaul defective cylinder as outlined
under 3.3 Master Cylinder or 3.4 Clutch
Slave Cylinder, in this Section.
DRAG OR FAILURE TO RELEASE Air trapped in hydraulic system.
Leak In hydraulic system.
Clutch master or slave cylinder
defective.
Cracked or oil-soaked linings.
Excessive driven plate run-out or
distorted.
Driven plate sticking on splines.
Transmission input shaft spigot
partially seized in crankshaft spigot
bush.
Bleed system as outlined under 3.2
Clutch Hydraulic System Bleed, in this
Section.
Correct leak and bleed hydraulic
system.
Replace defective cylinder as outlined
under 3.3 Master Cylinder or 3.4 Clutch
Slave Cylinder, in this Section.
Replace driven plate. Refer Operation
3.8 Clutch and Pressure Plates, in this
Section.
Replace driven plate. Refer Operation
3.8 Clutch and Pressure Plates, in this
Section.
Clean and free splines and apply 10%
molybdenum disulphide grease to
Holden’s Specification HN 1271.
Remove clutch, Iubricate or replace
bush. Refer Operation 3.10 Crankshaft
Spigot Bush, in this Section.
GRAB OR CHATTER Oil on linings.
Worn transmission input shaft splines.
Rou
h, or
rooved, fl
wheel o
pressure plate.
Loose engine mountings.
Loose or worn universal joints or loose
rear universal joint flange.
Defective clutch driven plate.
Replace driven plate, correct oil leak.
Replace transmission input shaft. Refer
Section 7B3 TRANSMISSION of the
VT Series II Service Information.
Replace fl
wheel or replace both
fl
wheel and pressure plate. Refe
Operation 3.8 Clutch and Pressure
Plates or 3.9 En
ine Fl
wheel, in this
Section.
Ti
hten or replace mountin
s. Refe
Section 6A3 ENGINE MECHANICAL
GEN III V8 ENGINE of the VT Series II
Service Information.
Ti
hten or replace universal
oint/s
and/or flan
e. Refer 4C PROPELLER
SHAFT AND UNIVERSAL JOINTS of
the VT Series I Service Information.
Replace clutch driven plate. Refer
Operation 3.8 Clutch and Pressure
Plates, in this Section.
HARD OR STIFF CLUTCH ACTlON Clutch pedal bush seized or ti
ht on
pedal shaft.
Blockage in fluid hydraulic pipe.
Replace bushes as detailed in 3.6
Clutch Pedal in this Section.
Clean lines and bleed hydraulic
system. Refer 3.2 Clutch Hydraulic
System Bleed in this Section.
CLUTCH ENGAGEMENT TOO SLOW Blocka
e in fluid h
draulic pipe.
Clutch master or slave c
linde
defective.
Incorrect brake fluid used.
Clean lines and bleed h
draulic
s
stem. Refer 3.2 Clutch H
draulic
System Bleed in this Section.
Replace defective cylinder as outlined
under 3.3 Master Cylinder or 3.4 Clutch
Slave Cylinder, in this Section.
Flush and bleed hydraulic system.
Refer 3.2 Clutch Hydraulic System
Bleed in this Section.