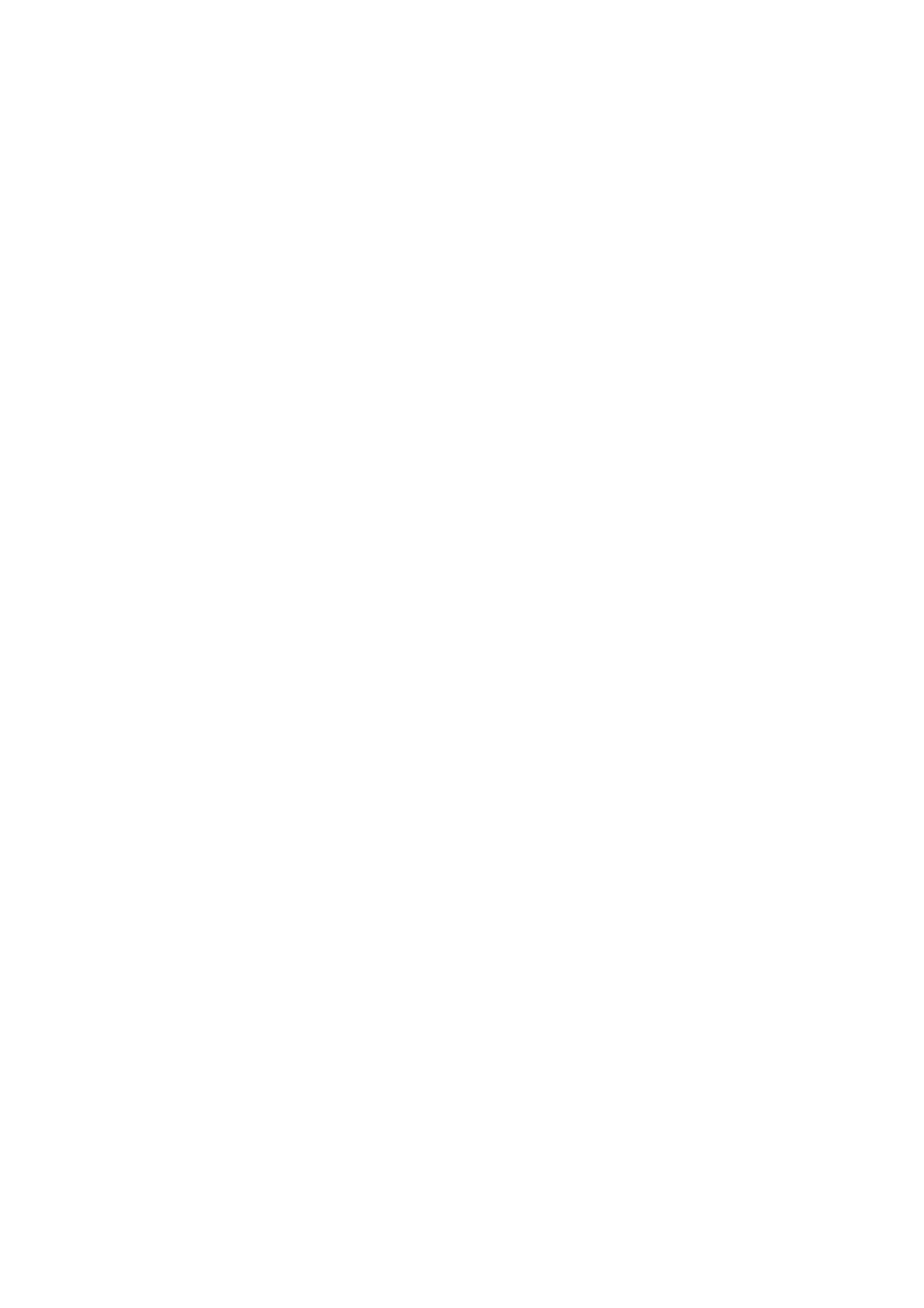
57 - BATTERY FEED - This s upplies the PCM with full time B+ volts . This c irc uit s tays hot even when the ignition is
turned off. The battery voltage feed circuit receives it's voltage fuse F31.
58 - SERIAL DATA (CLASS II) -This is a dedicated line for the Tech 2 scan tool communication. The circuit
connects the PCM, PIM, ABS/ETC, and BCM. T he Tech 2 s c an tool can talk to each of these modules by sending a
message to a controller and asking only it to respond. The communication carried on Class II data streams are
prioritised. The normal voltage on this line is 0 volts, but when the Tech 2 scan tool is connected, the voltage will
about 7 volts indicating communication.
59 - NOT USED
60 - THROTTLE POSITION SENSOR EARTH - This terminal should have zero volts. This circuit is connected
directly to the earth through the PCM.
61 - CAMSHAFT POSITION SENSOR REFERENCE LOW - This terminal should always be zero volts. It is
connected from the PCM to the CMP sensor and provided the earth signal needed for the sensor to operate.
62 - NOT USED
63 - OIL PRESSURE SENSOR EARTH - This terminal should always be zero volts. It is connected from the PCM
to the oil pressure sensor and provides the earth signal needed for the sensor to operate.
64 - NOT USED
65 - NOT USED
66 - BANK 2 SENSO R 1 OXY GEN SENSOR SIG NAL HIGH - With the ignition ON and the engine not running, the
voltage should be 350 - 450 millivolts (0.350 0.450 volts). This is the PCM supplied HO2S circuit bias voltage. When
the HO2S is hot, and the engine is r unning, the voltage should be rapidly changing, somewhere between 10 - 1000
millivolts (0.010 - 1000 volts).
67 - NOT USED
68 - NOT USED
69 - BANK 1 SENSOR 1 HEATED OXYGEN SENSOR SIGNAL HIGH - With the ignition ON and the engine not
running, the voltage should be 350 - 450 millivolts (0.350 0.450 volts). This is the PCM supplied HO2S circuit bias
voltage. When the HO2S is hot, and the engine is running, the voltage should be rapidly changing, somewhere
between 10 - 1000 millivolts (0.010 - 1000 volts).
70 - NOT USED
71 - ECONOM Y/POWER SWITCH INPUT - T he PCM sends a signal of about 12 volts, and monitors the status of
this circuit. In the ECONOMY position the switch is open, the PCM voltage status signal remains high - about 12
volts, and the PCM does not allow shift point changes. When the transmission switch is pressed to the POWER
position the switch is momentarily closed and the PCM voltage status signal is momentarily pulled low. The PCM
senses the momentary voltage signal drop and enables power mode shifting only if other criteria are met. These
criteria include throttle position and engine speed.
72 - PRNDL B - This circuit along with the circuits on PCM connector pins J1 32, 34 & J2 62 indicate to the PCM
what transm ission gear the driver has selected. The PCM will then send a com mand via the serial data line to the
instrument panel cluster (smart cluster) to indicate to the driver what gear has been selected.
73 - CAMSHAFT POSITION SENSOR INPUT SIGNAL - This signal indicates to the PCM when number 1 cylinder
is on the compression stroke.
74 - ENGINE COOLANT TEMPERATURE SENSOR SIGNAL - The PCM sends a 5 volt signal voltage to the
Engine Coolant Temperature sensor, which is a temperature variable resistor called thermistor. The sensor, being
also connected to earth, will alter the voltage according to engine coolant temperature. As the engine coolant
temper ature incr eases, the voltage s een on term inal C1 74 decr eases. At 0 degrees C engine coolant tem perature,
the voltage will be above 4 volts. At normal operating temperature the voltage will be less than 2 volts. The PCM
uses this signal for fueling.
75 - NOT USED
76 - FUEL INJECTOR #5 DRIVER - W ith the engine OFF and the ignition ON, the voltage should be B+. W ith the
engine running at idle, the charging s ystem increas es the battery voltage slightly, so this voltage will increas e. W ith
higher engine RPM or more engine load, the resulting increase in injector pulse frequency or injector pulse width will
cause this voltage to become slightly less.
77 - FUEL INJECTOR #8 DRIVER - W ith the engine OFF and the ignition ON, the voltage should be B+. W ith the
engine running at idle, the charging s ystem increas es the battery voltage slightly, so this voltage will increas e. W ith
higher engine RPM or more engine load, the resulting increase in injector pulse frequency or injector pulse width will
cause this voltage to become slightly less.
78 - NOT USED
79 - 3-2 SHIFT SOLENOID CONTROL- The 3- 2 s hif t s olenoid is a normally closed, pulse width modulated solenoid
used to control the 3-2 downshift. The PCM operates the 3-2 shift solenoid at a frequency of 50 Hz (cycles per
second). The solenoid is constantly fed B+ and the PCM controls the length of time the path to earth for the
electrical circuit is closed.