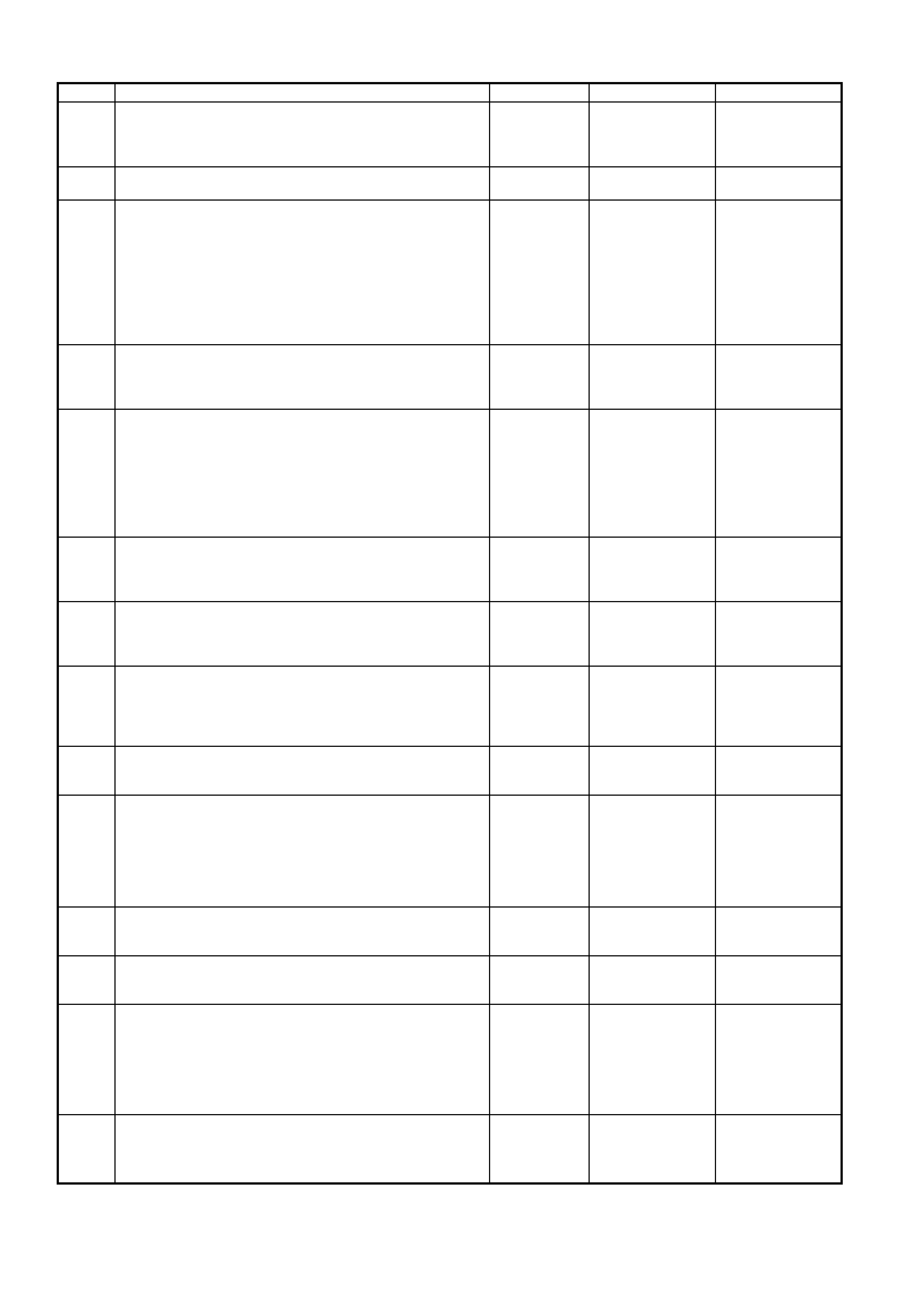
GEN III V8 PCM ELECTRONIC IGNITION SYSTEM DIAGNOSIS
Step Action Value(s) Yes No
1 Did you perform the Powertrain On-Board Diagnostic
(OBD) System Check? Go to Step 2 Go to Powertrain
OBD System
Check Table in
Section 6C3-2A
2 Are DTCs P0335, P0336, P0351-P0358 set? Go to Applicable
DTC table Go to Step 3
3 Important: This table assumes that there are no Ignition
Coil/Module circuit malfunctions or mechanical, and
DTCs P0351, P0352, P0353, P0354, P0355, P0356,
P0357, P0358 are not set.
1. Install the scan tool.
2. Start and idle the engine.
3. Monitor all the Ignition Coils on the Engine Data List
(There are a total of 8). using a scan tool.
Are any of the Ignition Coils indicating FAULT?
Go to Step 4 Intermittent
Condition. Go to
Diagnostic Aids
4 1. Turn ON the ignition leaving the engine OFF
2. Using a test light connected to earth, probe both sides
of both Ignition/Injector fuses.
Does test light illuminate at both terminals of both fuses?
Go to Step 5 Go to Step 8
5 1. Turn OFF the ignition.
2. Disconnect the ignition coil 8-way harness connector
for the Ignition Coil module that is indicating FAULT.
3. Turn ON the ignition leaving the engine OFF.
4. Probe the ignition feed circuit at the 8-way harness
connector using a test lamp J 34142-B connected
battery to earth.
Does the test lamp illuminate?
Go to Step 6 Go to Step 10
6 Using a test lamp J 34142-B probe the ignition feed
circuit at the 8-way connector to the ignition coil/module
earth circuit.
Does the test lamp illuminate?
Go to Step 7 Go to Step 13
7 Using a test lamp J 34142-B probe the ignition feed
circuit at the ignition coil/module electrical 8-way
connector to the ignition coil/module reference low circuit.
Does the test lamp illuminate?
Go to Step 21 Go to Step 17
8 1. Inspect for an open ignition coil/module fuse.
2. Locate and repair the ignition feed circuit for a earthed
circuit if the fuse is open.
3. Replace the fuse.
Did you find and correct the problem?
System OK Go to Step 9
9 Repair open in the ignition feed circuit between the EFI
relay and the splice.
Is the action complete?
System OK
10 1. Disconnect the ignition 8-way coil/module harness
connector for the Ignition Coil that is indicating
FAULT.
2. Probe the ignition feed circuit at the ignition
coil/module main 8-way connector using a test lamp
J 34142-B connected to battery earth.
Does the test lamp illuminate?
Go to Step 11 Go to Step 12
11 Repair the open circuit between the splice and the
ignition coil/module connector.
Is the action complete?
System OK
12 Repair the open ignition feed circuit between the fuse
block (open fuse) and splice.
Is the action complete?
System OK
13 1. Disconnect the ignition 8-way coil/module harness
connector for the Ignition Coil that is indicating
FAULT.
2. Using a test light J3414-B probe the ignition feed
circuit at the ignition coil/module 8-way connector to
the ignition coil/module earth circuit.
Does the test lamp illuminate?
Go to Step 14 Go to Step 16
14 1. Check for a poor connection at the ignition
coil/module electrical 8-way connector.
2. Repair poor connections as necessary.
Did you find and correct the problem?
System OK Go to Step 15