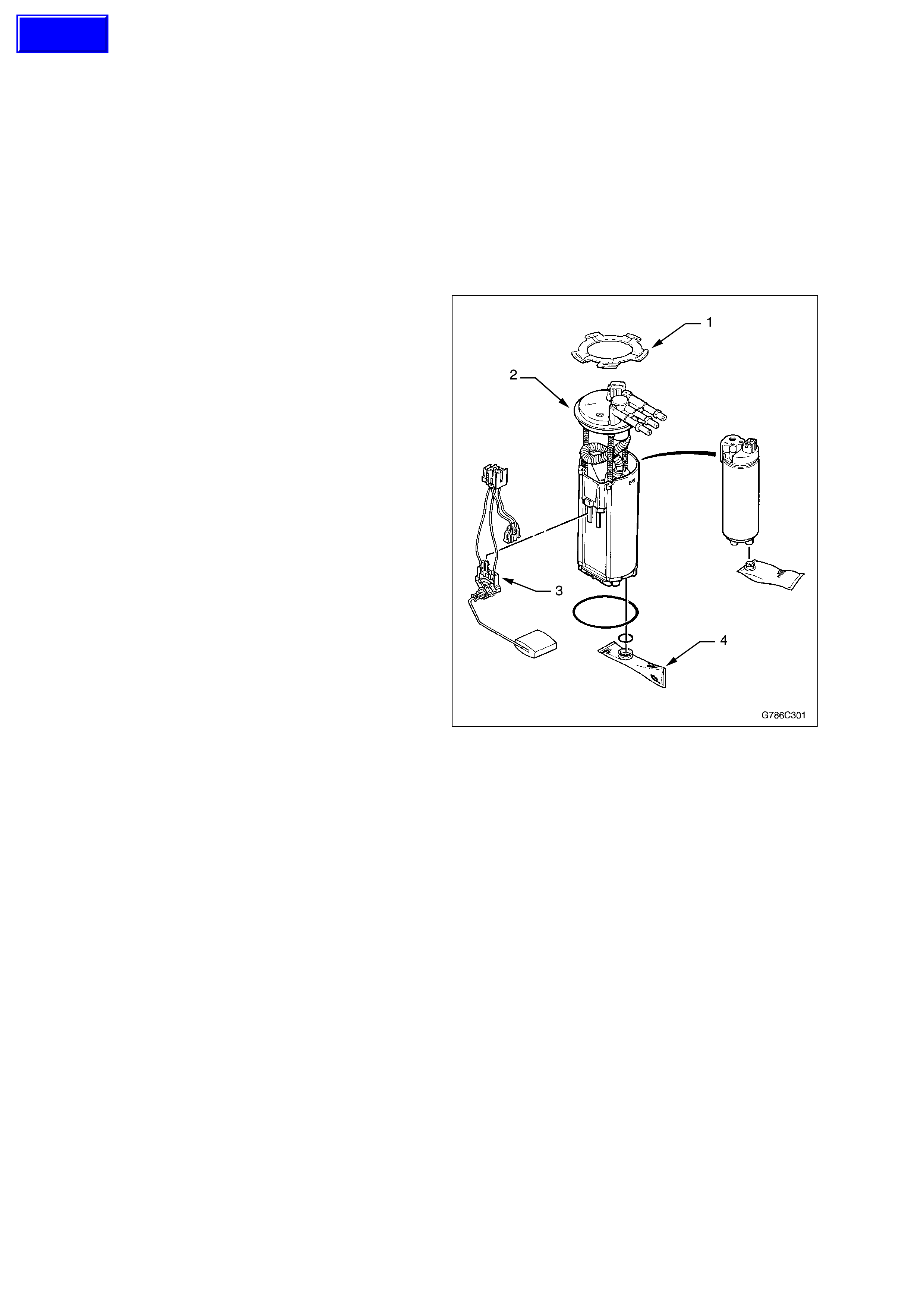
MODULAR FUEL SENDER ASSEMBLY
This Section describes the removal and installation
procedure for the modular fuel sender assembly,
and fuel level sensor. A full description of the
operation is provided in Section 8A, Fuel Tank in
the VT Series II Service Information.
NOTE: The modular fuel sender assembly is not
serviceable except for the fuel level sensor. If any
other part is found to be faulty, the complete fuel
sender assembly must be replaced.
Remove
TOOL REQUIRED: J 39765 Fuel Sender Locknut
Wrench.
CAUTION: In order to reduce the risk of fire or
personal injury that may result from fuel leakage,
always replace the fuel sender gasket when
reinstalling the fuel sender assembly.
NOTE: Do Not handle the fuel sender assembly by
the fuel pipes. The amount of leverage generated
by handling the fuel pipes could damage the joints.
1. Disconnect the negative battery cable.
2. Relieve the fuel system pressure. Refer to the
Fuel Pressure Relief Procedure in this
Section.
3. Drain and remove the fuel tank. Refer to
Section 8A, Fuel Tank, of the VT Series II
Service Information.
4. Remove the fuel sender assembly retaining ring
(1) using the J 39765 Fuel Sender Locknut
Wrench.
NOTE: The modular fuel sender assembly will
spring-up when the locking ring is removed.
5. Pull the modular fuel sender assembly (2)
straight up while draining the fuel from the
reservoir.
IMPORTANT: The reservoir bucket on the sender
assembly is full of fuel. Tip the assembly slightly
during removal in order to avoid damage to the fuel
level sensor (3) float. Place any remaining fuel into
an approved container once the modular fuel
sender assembly is removed from the fuel tank.
6. Clean the gasket sealing surfaces.
7. If required, remove the fuel level sensor by
disconnecting the wiring connector and
squeezing the retainer tabs and sliding the
sensor from the sender assembly.
Modular Fuel Sender Assembly
Reinstall
1. Fit the fuel level sensor to the modular fuel
sender assembly, ensuring the retaining tangs
are seated correctly.
2. Install the new gasket on the fuel sender
assembly.
IMPORTANT: The fuel strainer (4) must be in a
horizontal position when the sender assembly is
installed. Ensure the fuel strainer does not block
the travel of the float arm.